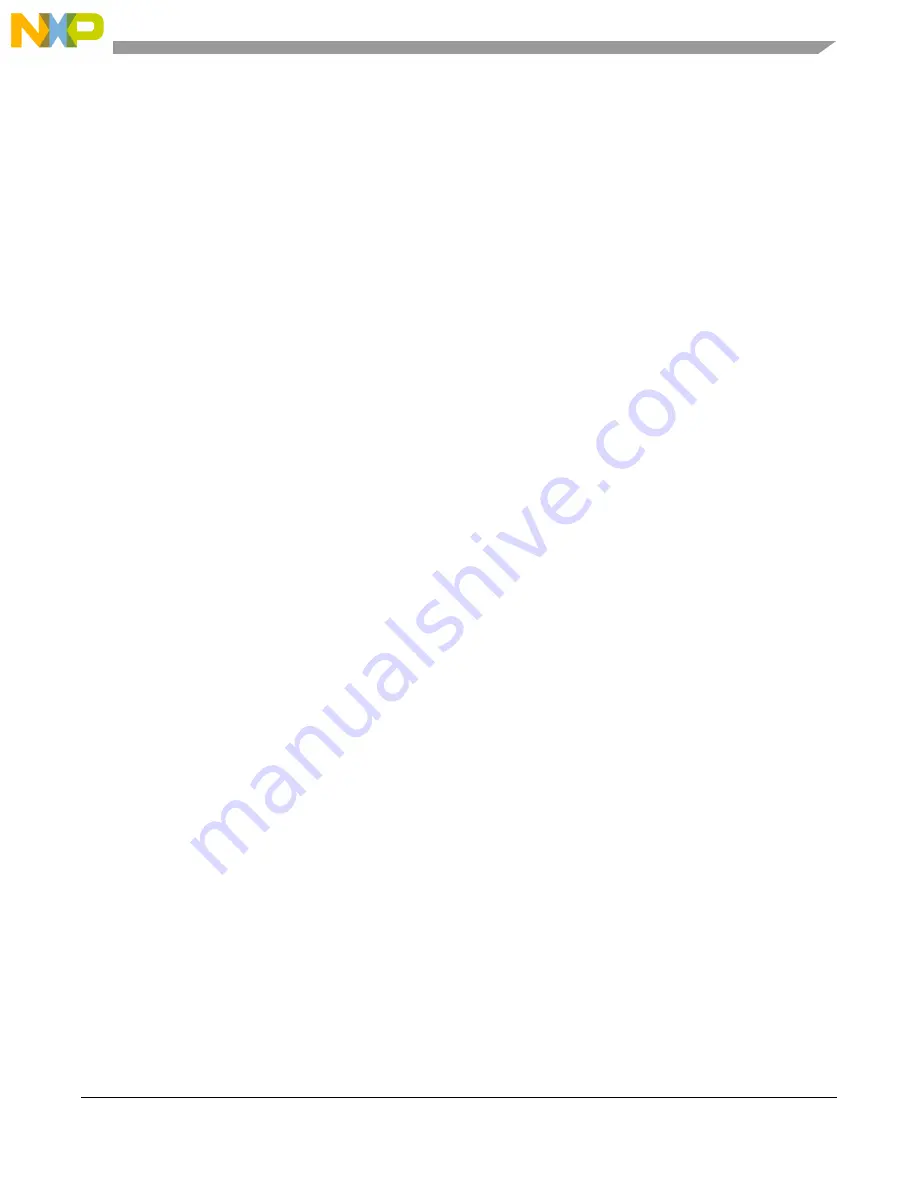
Enhanced Time Processing Unit (eTPU2)
MPC5644A Microcontroller Reference Manual, Rev. 6
Freescale Semiconductor
903
the correct estimated angle. This logic also includes the Tooth Program Register (TPR, see
Section 24.5.7.2, Angle mode registers
, for more information).
The Count Control and High Rate Logic handles deceleration, acceleration, missing teeth and last tooth.
On High Rate (acceleration) it ensures that the angle bus scans all valid angle values in a rate which can
be traced by the STAC bus. This operation enables external STAC clients (if TCR2 is a STAC server) or
channels working in “equal-only” comparator mode to match the TCR2 exported angle information in
“equal” mode, in an exact match.
Because the eTPU channels are capable of capturing either TCR1 or TCR2 due to signal transition, the
microcode can get either the angle or time of the physical pin transition. Since the EAC channel (0, 1 or
2) is connected to the physical tooth, the microcode can get the EAC error in angle domain (tooth appears
at the wrong angle) or time domain (physical tooth captured time into the EAC channel, relative to the
estimated tooth time). Note that in angle mode, the transition detect logic of the channel 0, if selected as
the EAC channel, is fed from the digital filter of the TCRCLK signal, and not from the channel 0 internal
digital filter. This ensures synchronous operation of channel 0 and the EAC hardware.
Another feature of the eTPU channel, when working in Single Match And Single Transition Enhanced
Mode (refer to
Section , Single Match Enhanced Mode (sm_st_e)
), is capturing a single time base due to
signal transition before and after the digital filter. This option allows subtracting the digital filter delay to
get accurate signal transition timing on the channel. This way, the TCRCLK signal may be programmed
with a slow and reliable digital filter, and get accurate time measurement of the digital filter delay.
To assert the end of the estimated tooth period the Count Control and High Rate logic compares the TICKS
field in TPR (refer to
Section 24.5.7.2, Angle mode registers
) with the current value of the tooth tick
counter. When the Tooth Tick value is greater or equal to TICKS, it determines the end of the estimated
tooth period. On acceleration this event occurs during High Rate mode operation, after the arrival of a
physical tooth. In deceleration, this event occurs during Normal Mode, before the arrival of a physical
tooth. On constant angular velocity, this event appears together with the arrival of a physical tooth.
The following sections describe the operation of the Counter Control and High Rate logic.
24.5.7.5.1
Normal mode
In Normal mode the Counter Control logic advances TCR2 and the Tooth Tick counter as if the engine has
a constant speed during the tooth period. It receives the angle ticks from the Angle Tick Generator in an
average rate which is determined by the Tooth Rate Register (TRR). This is the reset mode.
When the Tooth Tick Counter is about to reach the last value effectively stored in TPR field TICKS plus
one, the hardware detects the end of the estimated tooth period. If the physical tooth and the estimated
tooth arrive at the same time the EAC stays in Normal mode, the Tooth Tick Counter is reset, and TCR2
is incremented (depending on TPR bits LAST and MISSCNT). If the physical tooth and the estimated
tooth do not arrive at the same time, either acceleration or deceleration is detected, and the EAC switches
to the proper mode. See
for a detailed diagram of Normal Mode behavior.
The microcode which services the EAC channel physical tooth transition may update TRR according to
various conditions to give the best estimation of the current tooth period, according to the previous tooth
period and other engine parameters.
Summary of Contents for MPC5644A
Page 2: ...MPC5644A Microcontroller Reference Manual Rev 6 2 Freescale Semiconductor...
Page 24: ...MPC5644A Microcontroller Reference Manual Rev 6 24 Freescale Semiconductor...
Page 26: ...MPC5644A Microcontroller Reference Manual Rev 6 26 Freescale Semiconductor...
Page 52: ...Introduction MPC5644A Microcontroller Reference Manual Rev 6 52 Freescale Semiconductor...
Page 56: ...Memory Map MPC5644A Microcontroller Reference Manual Rev 6 56 Freescale Semiconductor...
Page 1228: ...Decimation Filter MPC5644A Microcontroller Reference Manual Rev 6 1228 Freescale Semiconductor...
Page 1440: ...FlexCAN Module MPC5644A Microcontroller Reference Manual Rev 6 1440 Freescale Semiconductor...