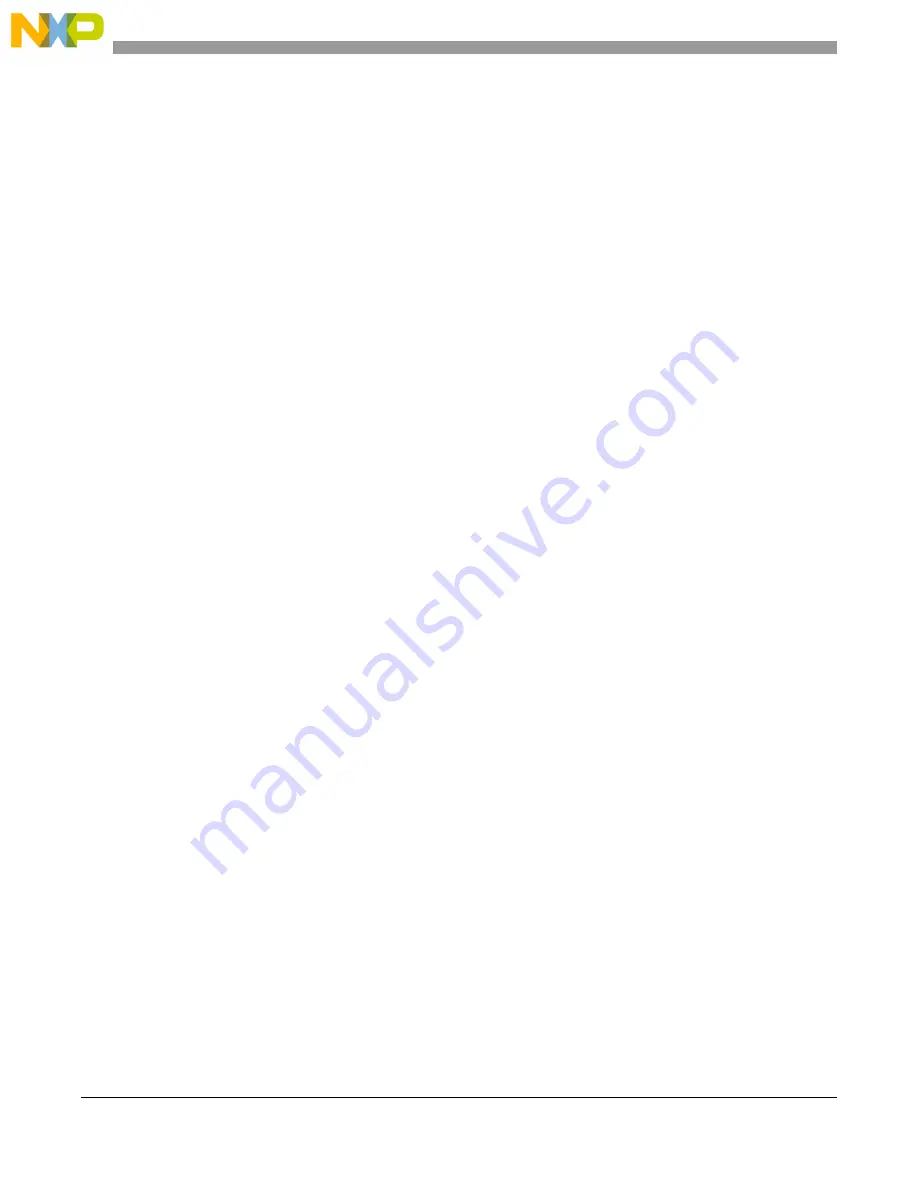
Enhanced Time Processing Unit (eTPU2)
MPC5644A Microcontroller Reference Manual, Rev. 6
900
Freescale Semiconductor
24.5.7.3
Acceleration and deceleration
Acceleration and deceleration affect the new tooth period relative to the known period of the last tooth.
Changes in tooth period may be extreme at very low engine RPM (such as cold start and warm start). The
worst case of tooth period changes is caused during missing teeth, since there is more time for changes in
angular velocity to be unnoticed by the EAC hardware. For example, on cold start (~20 RPM) there may
be extreme acceleration: the ratio between a known tooth period before two missing teeth and the new
tooth period after the missing teeth can be very high (up to a factor of 75). Acceleration and deceleration
effects from tooth to tooth are less extreme as the engine climbs to high RPM.
In case of deceleration, the estimated tooth period ends before the actual tooth detection arrives. In this
case, the EAC hardware waits at the end of the current tooth period, when it is said to be in
Halt mode
,
until the real tooth indication is received, then continues with normal operation (
Normal mode
). See
.
In case of acceleration, the actual tooth period is shorter than the estimated tooth period. As a result, a new
physical tooth indication arrives before the end of the estimated tooth period. In this case the EAC closes
the gap on
High Rate mode
by counting on system clock divided by eight to the end of the tooth, advances
to the next tooth, and switches back to normal operation mode. See
The reason that the EAC does not jump directly to the next tooth is the need to provide sequential angle
count throughout the whole tooth period, for channels or external STAC clients (if TCR2 is a STAC
server) which compare angle in “equal” mode. These peripherals must get all the valid angle values in a
sequential manner, to avoid missing angle matches.
TCR2 advancing from one tooth to another is a continuous count, and can be optionally reset at the end of
the tooth. An estimated tooth is generated after the Tooth Tick Counter reaches the TICKS programmed
value.
The EAC works continuously and switches automatically between Normal, Halt and High Rate modes. It
relies on the microcode to calculate the estimated tooth period on every tooth, and to update the correct
angle tick and tooth parameters in the EAC control registers. On high RPM, tooth period changes are
reduced from tooth to tooth, and the EAC may follow the angle with good accuracy for several teeth
without microcode intervention.
The EAC handles missing teeth by insertion of “dummy” teeth, or by enlarging the expected tooth period.
It is a good practice to locate the flywheel missing teeth in non-critical angles, since a missing tooth may
increase the angle measurement error (acceleration and deceleration is detected late).
24.5.7.4
Angle tick generator
The Angle Tick Generator is responsible for generating a programmed number of angle ticks in the tooth
period. It generates the ticks in an average rate which ensures completion of the correct number of angle
counts in the estimated period of the tooth, since the count of one tooth in angle ticks is independent on
engine RPM. The main output of the Angle Tick Generator is the tick clock that feeds TCR2 in Angle
Mode, as well as the internal Tooth Tick Counter (see
). The Tooth Tick Counter counts ticks
within a tooth, from 0 up to TICKS, is controlled by the Angle Tick Generator logic and cannot be accessed
by microcode. Refer to
for a generic presentation of the angle tick count and the
measurement of a single tooth period.
Summary of Contents for MPC5644A
Page 2: ...MPC5644A Microcontroller Reference Manual Rev 6 2 Freescale Semiconductor...
Page 24: ...MPC5644A Microcontroller Reference Manual Rev 6 24 Freescale Semiconductor...
Page 26: ...MPC5644A Microcontroller Reference Manual Rev 6 26 Freescale Semiconductor...
Page 52: ...Introduction MPC5644A Microcontroller Reference Manual Rev 6 52 Freescale Semiconductor...
Page 56: ...Memory Map MPC5644A Microcontroller Reference Manual Rev 6 56 Freescale Semiconductor...
Page 1228: ...Decimation Filter MPC5644A Microcontroller Reference Manual Rev 6 1228 Freescale Semiconductor...
Page 1440: ...FlexCAN Module MPC5644A Microcontroller Reference Manual Rev 6 1440 Freescale Semiconductor...