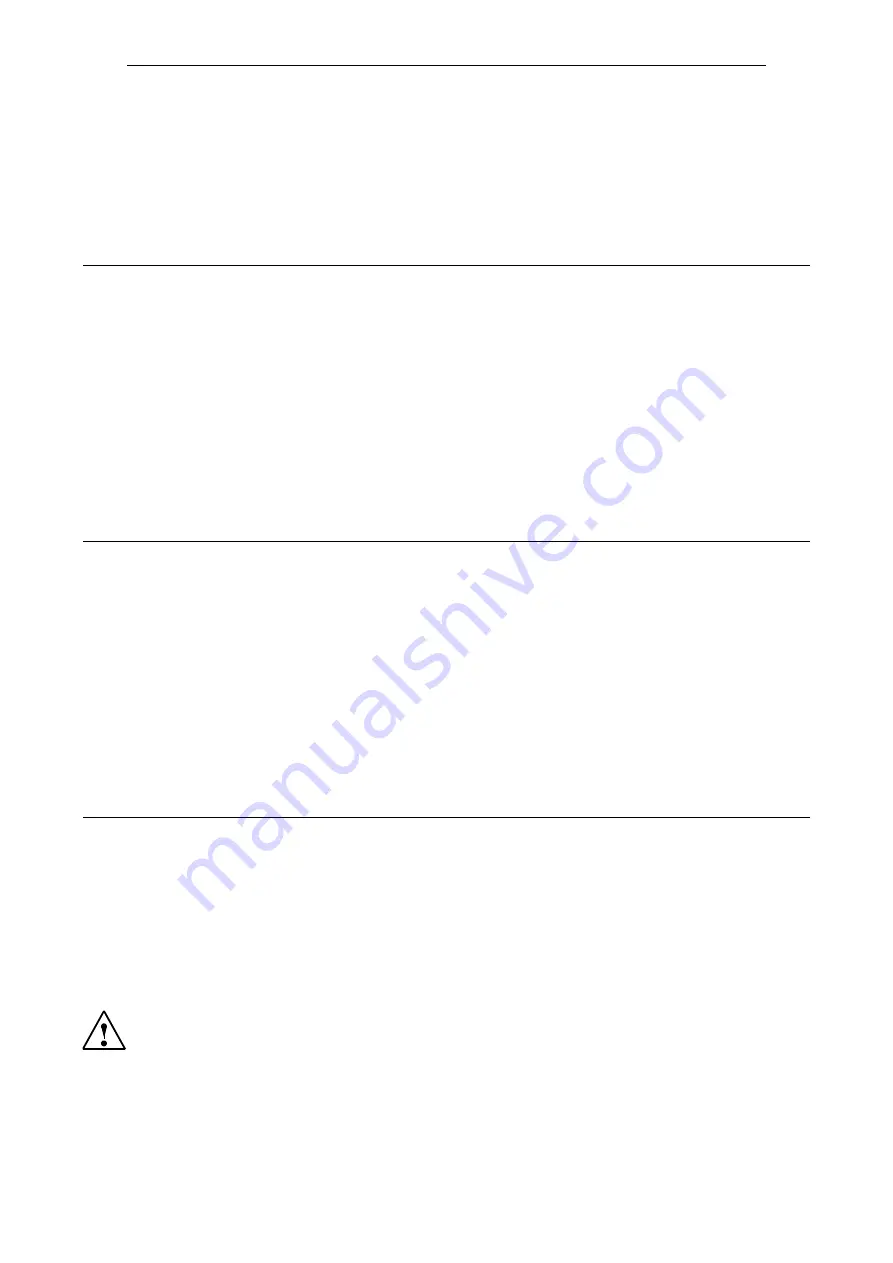
List of parameters
Parameters
1-635
© Siemens AG 2007 All Rights Reserved
SINAMICS S List Manual (LH1), 07/2007
After the positioning monitoring time expires, it is checked once as to whether the difference between the setpoint
and actual position lies within the positioning window and if required an appropriate fault is output.
Value = 0 --> The positioning monitoring function is de-activated.
Dependency:
Refer to: p2542, p2545, r2684
Refer to: F07451
Note:
The following applies for the setting of the standstill and positioning window:
Standstill window (p2542) >= positioning window (p2544)
Description:
Sets the positioning monitoring time for the positioning monitoring.
After the positioning monitoring time expires, it is checked once as to whether the difference between the setpoint
and actual position lies within the positioning window and if required an appropriate fault is output.
Dependency:
Refer to: p2543, p2544, r2684
Refer to: F07451
Note:
The following applies for the setting of the standstill and positioning monitoring time:
Standstill monitoring time (p2543) <= positioning monitoring time (p2545)
Description:
Sets the tolerance for the dynamic following error monitoring.
If the dynamic following error (r2563) exceeds the selected tolerance, then an appropriate fault is output.
Value = 0 --> The dynamic following error monitoring is de-activated.
Dependency:
Refer to: r2563, r2684
Refer to: F07452
Note:
The tolerance bandwidth is intended to prevent the dynamic following error monitoring incorrectly responding due to
operational control sequences (e.g. during load surges).
Description:
Sets the cam switching position 1.
Dependency:
Refer to: p2548, r2683
Caution:
Only after the axis has been referenced can it be guaranteed that the cam switching signals when output have a
"true" position reference.
Note:
Position actual value <= cam switching position 1 --> r2683.8 = 1 signal
Position actual value > cam switching position 1 --> r2683.8 = 0 signal
p2545
LR positioning monitoring time / t_pos_monit
SERVO (Pos ctrl),
VECTOR (Pos ctrl)
Can be changed:
U, T
Calculated:
-
Access level:
1
Data type:
Floating Point
Dynamic index:
-
Func. diagram:
4020
P-Group:
Closed loop position control
Units group:
-
Unit selection:
-
Not for motor type:
-
Expert list:
1
Min Max
Factory
setting
0.00 [ms]
100000.00 [ms]
1000.00 [ms]
p2546[0...n]
LR dynamic following error monitoring tolerance / s_delta_monit tol
SERVO (Pos ctrl),
VECTOR (Pos ctrl)
Can be changed:
U, T
Calculated:
-
Access level:
1
Data type:
Unsigned32
Dynamic index:
DDS, p0180
Func. diagram:
4025
P-Group:
Closed loop position control
Units group:
-
Unit selection:
-
Not for motor type:
-
Expert list:
1
Min Max
Factory
setting
0 [LU]
2147483647 [LU]
1000 [LU]
p2547
LR cam switching position 1 / Cam position 1
SERVO (Pos ctrl),
VECTOR (Pos ctrl)
Can be changed:
U, T
Calculated:
-
Access level:
1
Data type:
Integer32
Dynamic index:
-
Func. diagram:
4025
P-Group:
Closed loop position control
Units group:
-
Unit selection:
-
Not for motor type:
-
Expert list:
1
Min Max
Factory
setting
-2147483648 [LU]
2147483647 [LU]
0 [LU]
Содержание SINAMICS S Series
Страница 1: ...sinamics s SINAMICS S List Manual 07 2007 ...
Страница 2: ......
Страница 1422: ...Function Diagrams Braking Module external 2 1422 Siemens AG 2007 All Rights Reserved SINAMICS S List Manual LH1 07 2007 ...
Страница 1750: ...Faults and Alarms List of faults and alarms 3 1750 Siemens AG 2007 All Rights Reserved SINAMICS S List Manual LH1 07 2007 ...
Страница 1778: ...Appendix List for motor code encoder code A 1778 Siemens AG 2007 All Rights Reserved SINAMICS S List Manual LH1 07 2007 ...
Страница 1812: ...Index D 1812 Siemens AG 2007 All Rights Reserved SINAMICS S List Manual LH1 07 2007 ...