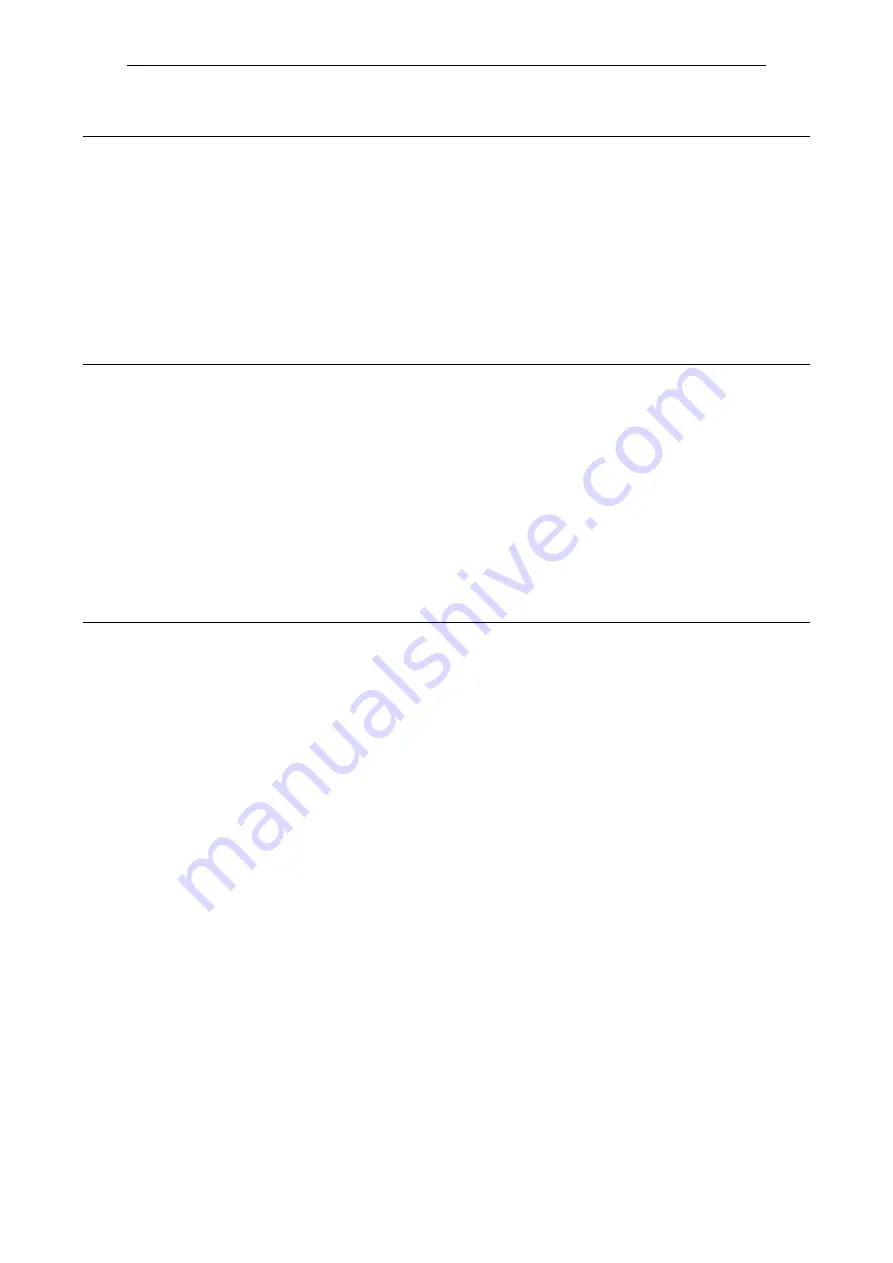
Faults and Alarms
List of faults and alarms
3-1538
© Siemens AG 2007 All Rights Reserved
SINAMICS S List Manual (LH1), 07/2007
F07410
Drive: Current controller output limited
Drive object:
SERVO, VECTOR
Reaction:
OFF2 (NONE, OFF1)
Acknowledge:
IMMEDIATELY
Cause:
The condition "I_act = 0 and Uq_set_1 longer than 16 ms at its limit" is present and can be caused by the following:
- motor not connected or motor contactor open.
- no DC link voltage present.
- Motor Module defective.
- the "flying restart" function is not activated.
Remedy:
- connect the motor or check the motor contactor.
- check the DC link voltage (r0070).
- check the Motor Module.
- activate the "flying restart" function (p1200).
F07411
Drive: Flux controller output limited
Drive object:
SERVO
Reaction:
OFF2 (NONE, OFF1)
Acknowledge:
IMMEDIATELY
Cause:
The specified flux setpoint cannot be reached although 90% of the maximum current has been specified.
- incorrect motor data.
- motor data and motor configuration (star/delta) do not match.
- the current limit has been set too low for the motor.
- induction motor (sensorless, open-loop controlled) in I2t limiting.
- the Motor Module is too small.
Remedy:
- correct the motor data.
- check the motor configuration.
- correct the current limits (p0640, p0323).
- reduce the induction motor load.
- if required, use a larger Motor Module.
F07412
Drive: Commutation angle incorrect (motor model)
Drive object:
SERVO, VECTOR
Reaction:
ENCODER (NONE, OFF2)
Acknowledge:
IMMEDIATELY
Cause:
An incorrect commutation angle was detected, that can result in a positive coupling in the speed controller.
Possible causes:
- the motor encoder is incorrectly adjusted with respect to the magnet position.
- the motor encoder is damaged.
- the angular commutation offset is incorrectly set (p0431).
- data to calculate the motor model has been incorrectly set (p0356 (motor-stator leakage inductance) and/or p0350
(motor-stator resistance) and/or p0352 (cable resistance).
- the changeover speed for the motor model is too low (p1752). The monitoring function only becomes effective
above the changeover speed.
- the motor encoder speed signal is faulted.
- the control loop is instable due to incorrect parameterization.
Fault value (r0949, interpret decimal):
SERVO:
0: The comparison of the pole position angle from the encoder and the motor model resulted in an excessively high
value (> 80 ° electrical).
1: -
VECTOR:
0: The comparison of the pole position angle from the encoder and the motor model resulted in an excessively high
value (> 45 ° electrical).
1: The change in the speed signal from the motor encoder has changed by > p0492 within a current controller clock
cycle.
Содержание SINAMICS S Series
Страница 1: ...sinamics s SINAMICS S List Manual 07 2007 ...
Страница 2: ......
Страница 1422: ...Function Diagrams Braking Module external 2 1422 Siemens AG 2007 All Rights Reserved SINAMICS S List Manual LH1 07 2007 ...
Страница 1750: ...Faults and Alarms List of faults and alarms 3 1750 Siemens AG 2007 All Rights Reserved SINAMICS S List Manual LH1 07 2007 ...
Страница 1778: ...Appendix List for motor code encoder code A 1778 Siemens AG 2007 All Rights Reserved SINAMICS S List Manual LH1 07 2007 ...
Страница 1812: ...Index D 1812 Siemens AG 2007 All Rights Reserved SINAMICS S List Manual LH1 07 2007 ...