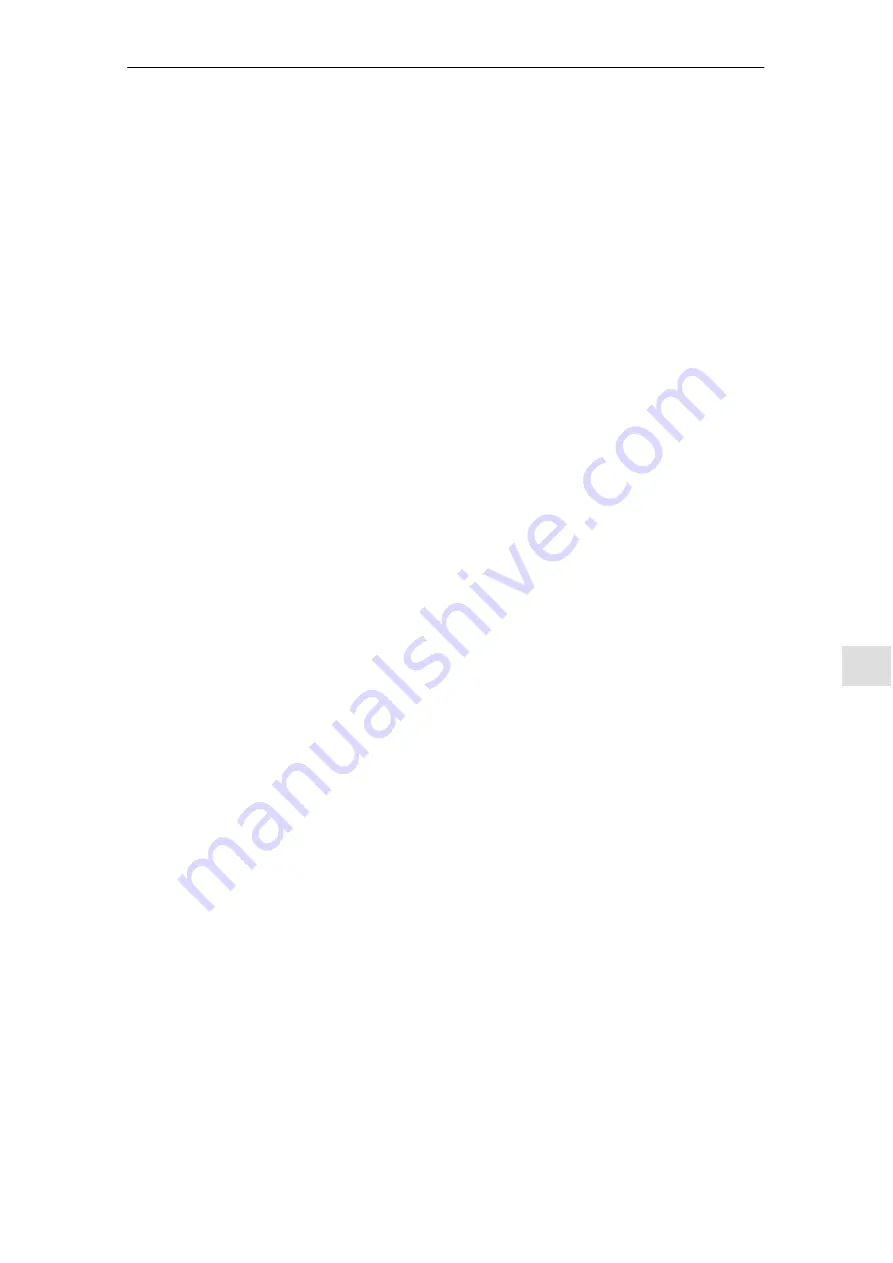
7
7.3
List of faults and warnings
7-667
Siemens AG 2005 All Rights Reserved
SIMODRIVE 611 universal Description of Functions (FBU) – 04.05 Edition
601
Error in AD conversion, terminal 56/14 or 24/20
Cause
A timing error was identified when reading-out the A/D converter for
terminal 56.x/14.x or 24.x/20.x. The read values are probably incor-
rect/faulty.
Remedy
Replace closed-loop control module
Acknowledgement RESET FAULT MEMORY
Stop response
parameterizable
602
Open-loop torque controlled oper. w/o encoder is not
perm.
Cause
In the IM mode, open-loop torque controlled operation was selected via
an input terminal or via PROFIBUS-DP or the bus interface.
Remedy
Deselect the torque-controlled operation or leave the IM mode (change-
over speed P1465).
Acknowledgement RESET FAULT MEMORY
Stop response
parameterizable
603
Changeover to non-parameterized motor data set
Cause
An attempt was made to change over to a motor data set which was
not parameterized.
Remedy
Parameterizing motor data set
Acknowledgement RESET FAULT MEMORY
Stop response
parameterizable
604
Motor encoder is not adjusted
Cause
For an EnDat motor measuring system, it was identified that the serial
number does not match that saved, i.e. the encoder has still not run
with this drive.
Remedy
1FN3 linear motors (if P1075=1):
Measure the rotor position offset to the EMF of the U_R phase and add
to P1016 as the commutation angle offset. Then set P1017 to –1 in
order to save the serial number of the EnDat encoder.
otherwise:
To determine commutation angle offset in P1016, initiate the rotor posi-
tion identification routine via P1017=1. The rotor position identification
routine is executed by acknowledging the fault and setting the enable
signals.
Note:
also refer to description of P1017
Acknowledgement RESET FAULT MEMORY
Stop response
parameterizable
7 Fault Handling/Diagnostics
01.99
04.05