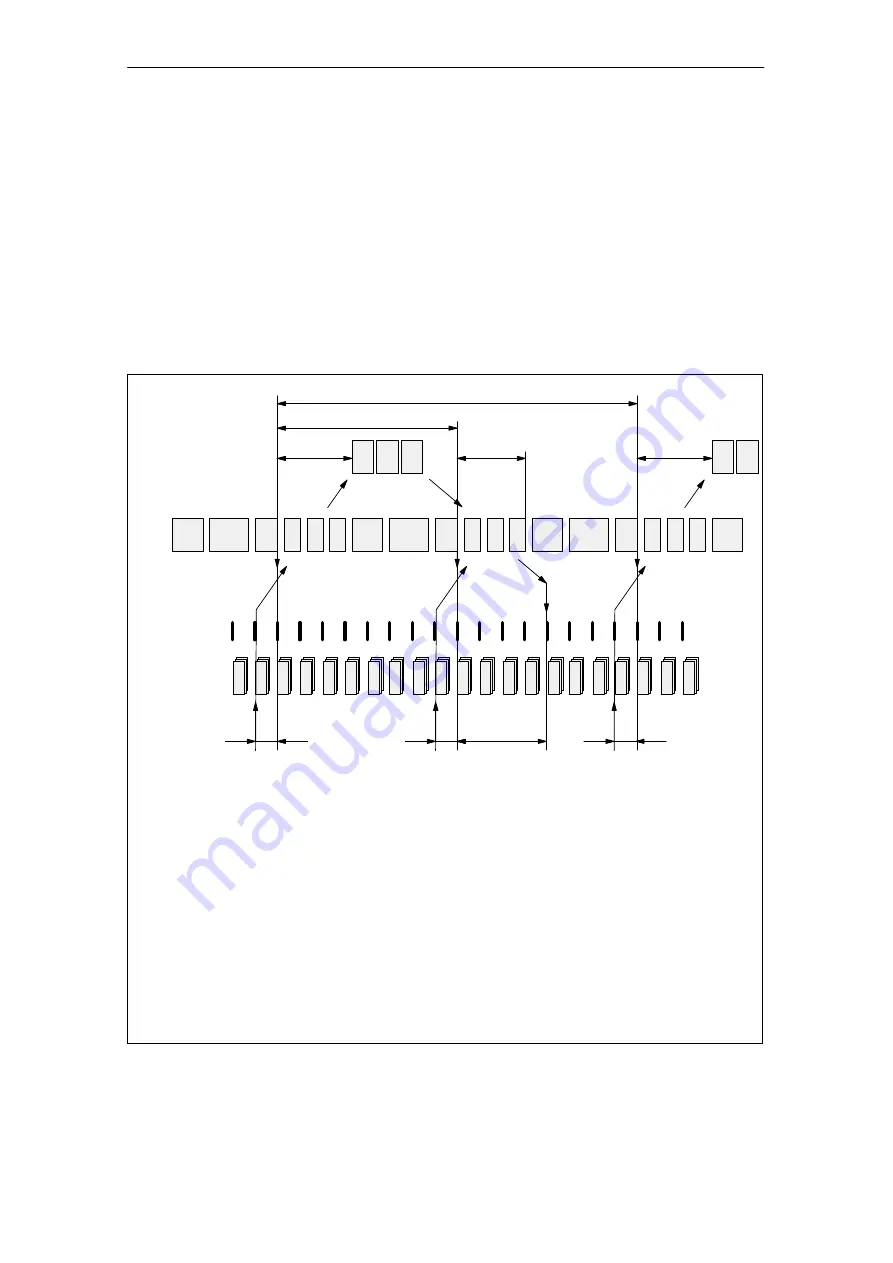
5
5.8
Motion Control with PROFIBUS–DP (from SW 3.1)
5-296
Siemens AG 2005 All Rights Reserved
SIMODRIVE 611 universal Description of Functions (FBU) – 04.05 Edition
The position actual value x
act
is read in to the telegram image at time T
I
before the start of each DP clock cycle, and is transferred to the DP
master at the next DP cycle.
The closed–loop DP master control starts at the time T
M
after each
position controller clock cycle, and uses the slave actual values which
were previously read. The master transfers the calculated setpoints to
the telegram image of the slave in the next DP cycle. The speed set-
point n
set
is input into the control at instant T
O
after the start of the DP
cycle.
By minimizing the times T
O
and T
I
the deadtime is also minimized in
the higher–level position control loop.
R
T
MAPC
Master Application Cycle Position controller cycle
T
DP
DP cycle time DP cycle time
T
DX
Data Exchange Time: Sum of the data transfer times of all of the slaves
T
M
Master time: Start of the closed–loop master control
T
I
Input time: Instant in time for the actual value sensing
T
O
Output time: Time of setpoint transfer
GC
Global Control Telegram (Broadcast Telegram)
R
Computation time, speed/position controller
Dx
Slaves: Net data transfer between master and slave 1 – n
MSG
Acyclical utilities (for example, DP/V1, token passing)
RES
Reserve: ”Active pause” until the isochronous (equidistant) cycle has expired
Dx
Dx
Dx
GC
MSG
RES
MSG
Dx
Dx
Dx
MSG
Dx
Dx
Dx
MSG
R
R
R
R
R
R
R
R
R
R
R
R
R
R
R
R
R
R
R
R
R
R
R
R
R
R
R
R
R
R
R
R
R
R
R
R
R
R
R
R
R
R
R
R
R
R
R
R
R
R
R
R
R
R
R
R
R
R
R
R
R
R
Speed
controller
clock cycle
Slave
1 to 3
Master
(position controller)
R1 R2 R3
Position
controller cycle
T
I
T
M
T
O
T
MAPC
= 2
T
DP
T
M
T
DP
T
I
RES
GC
RES
GC
T
I
R1 R2
T
DX
Fig. 5-26 Example: optimized DP cycle with T
MAPC
= 2
T
DP
Timing
5 Communications via PROFIBUS DP
08.99