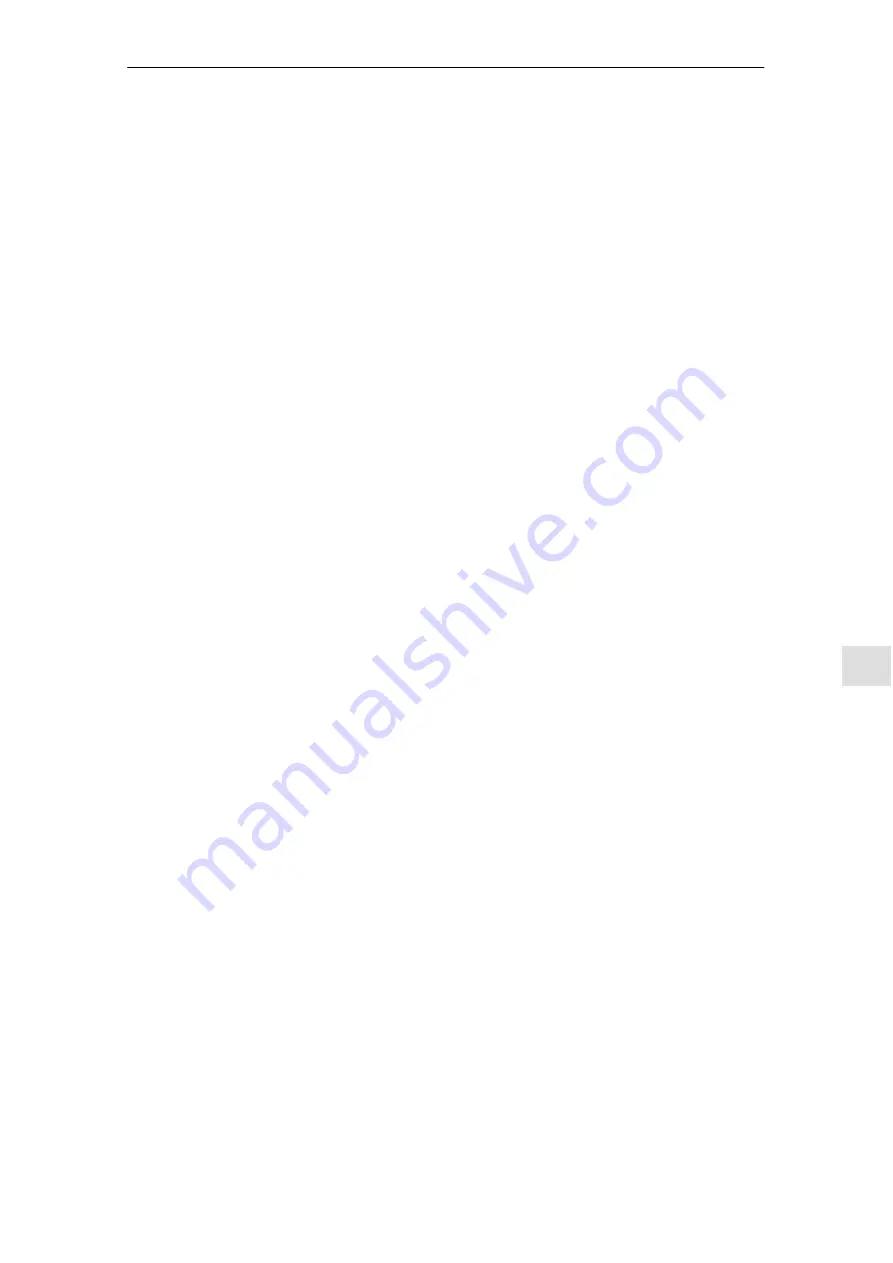
7
7.3
List of faults and warnings
7-669
Siemens AG 2005 All Rights Reserved
SIMODRIVE 611 universal Description of Functions (FBU) – 04.05 Edition
P1606 = 8000 rev/min
Induction motor:
Acceleration and braking with the maximum torque/current are usual in
operation, only a stalled drive (0 speed) is monitored.
P1605 = 200 ms
P1606 = 30 rev/min
1. At the first commissioning, after the software has been replaced or
the software has been upgraded, after the parameters have been en-
tered the ”calculate motor data” or ”calculate controller data” function
was not executed. The drive then keeps the default values (for the val-
ues to be calculated this is zero) which can, under certain circum-
stances, result in this fault (P1605 and P1606 should be adapted to the
mechanical and dynamic capabilities of the axis).
2. An undesirable input of a high torque reduction via the analog inputs
or via PROFIBUS and the bus interface. For PROFIBUS and the bus
interface, this effect especially occurs when changing from the position-
ing mode to the speed setpoint input mode (check as to whether a
torque reduction is entered. Diagnostics using P1717, 0%: No torque,
100%: Full torque).
Remedy
– Check connecting cable motor/converter (phase missing, exchanged)
– Check the motor contactor
– Check the torque reduction (P1717)
– DC link voltage present?
– Check the DC link voltage (check that the screws are tight)
– Unblock the motor
– Is the motor encoder connected?
– Check the motor encoder cable screen
– Is the motor grounded (PE connection)?
– Check the encoder pulse number (P1005)
– Does the encoder cable fit to the encoder type?
– Check the direction of rotation of the encoder tracks (e.g. toothed-
wheel encoder, P1011)
Adapt parameters P1605 and P1606 to the mechanical and dynamic
capabilities of the axis. Check whether a torque reduction has been
entered (diagnostics via P1717, 0%: no torque, 100%: full torque).
For linear motors:
– Check actual value inversion
– Check the reduction in the maximum motor current (P1105) and if
required increase the value
– Check the power cable connection
– For the parallel circuit configuration, are the motors correctly
assigned and electrically connected?
– Use monitoring function in the power section has responded (RESET
by powering off/powering on)
– Replace the power section or control module
Acknowledgement RESET FAULT MEMORY
Stop response
parameterizable
7 Fault Handling/Diagnostics
01.99
04.05