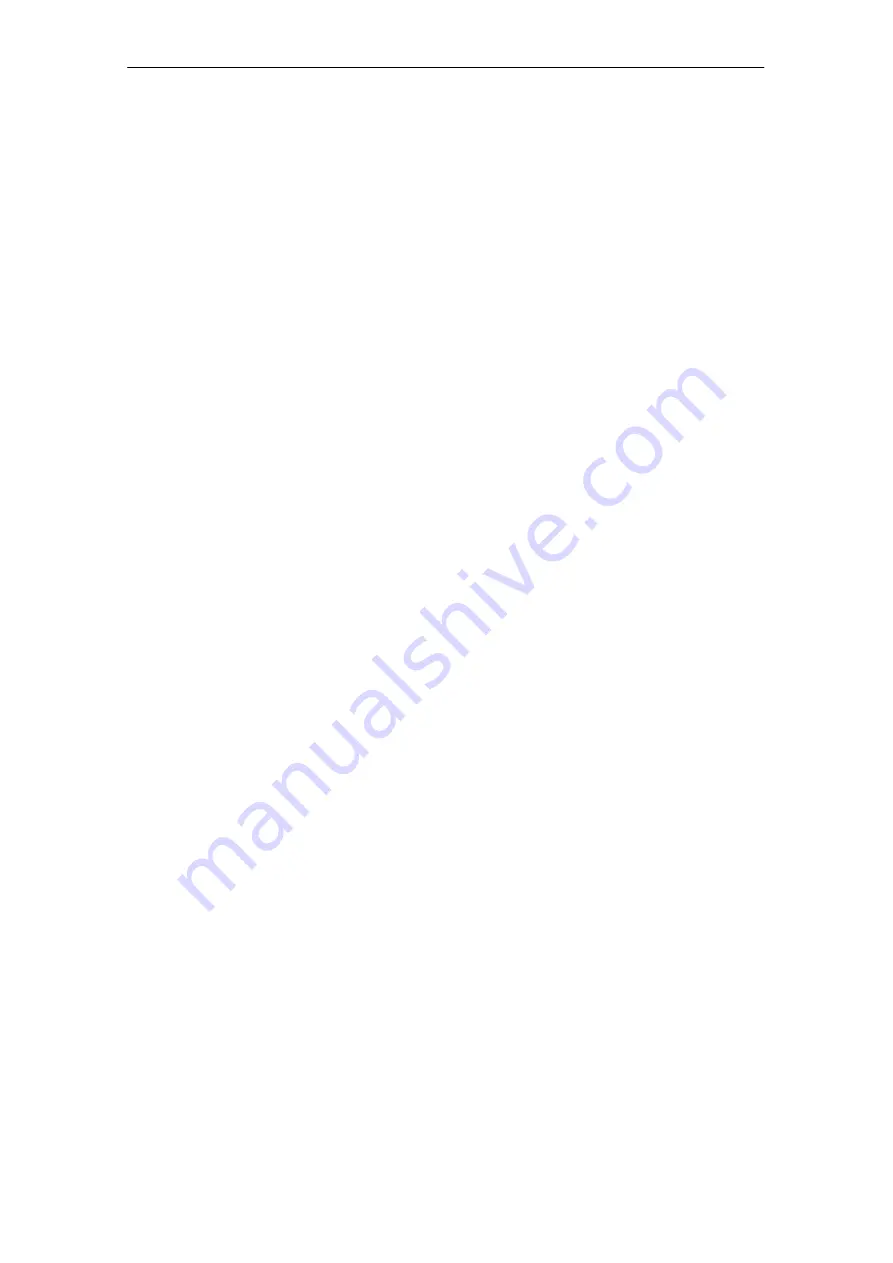
7
7.3
List of faults and warnings
7-684
Siemens AG 2005 All Rights Reserved
SIMODRIVE 611 universal Description of Functions (FBU) – 04.05 Edition
753
Current, rotor position identification less than the min.
value
Cause
A current was parameterized in P1019 (current, rotor position identifica-
tion) which is less than the minimum value permissible for the motor.
Remedy
Enter a current in P1019, which is not less than the permissible mini-
mum value for the motor (40% for third-party synchronous linear
motor). It may be necessary to use a larger power module.
If permissible for the motor used, suppress the fault by setting P1012,
bit 5.
Caution:
For motors with weak saturation effects (e.g. 1FN3 linear motors), as a
result of the low identification current, orientation may be erroneous,
thus resulting in uncontrolled motion.
Acknowledgement RESET FAULT MEMORY
Stop response
STOP II (SRM, SLM) STOP I (ARM)
756
Invalid speed hysteresis of the current setpoint
smoothing
Cause
The hysteresis of the speed for the current setpoint smoothing (P1246)
may not be greater than the threshold speed of the hysteresis (P1245),
as otherwise a ”negative” lower speed would be obtained.
Remedy
P1246 (standard value: 50 [RPM]) must be entered lower than the
threshold for the speeddependent setpoint smoothing (P1245, standard
value: 4 000 [RPM]).
Acknowledgement RESET FAULT MEMORY
Stop response
STOP II (SRM, SLM) STOP I (ARM)
757
PZD config.: illegal frame no. in P0922
Cause
The frame number set in P0922 is illegal or impermissible for the oper-
ating mode currently selected via P0700.
Remedy
Check P0922 and enter valid value.
Acknowledgement POWER ON
Stop response
STOP II
758
Setpoint source incorrectly parameterized. Supplemen-
tary info \%u
Cause
The selected setpoint source in P0891 is invalid.
1 Internal coupling not possible for POSMO or single-axis module
2 Internal coupling not possible for drive A
3 Coupling via PROFIBUS-DP or the bus interface selected, but the
matching option module is not inserted
Remedy
Check P891 and enter a valid value.
Acknowledgement POWER ON
Stop response
STOP II
7 Fault Handling/Diagnostics
01.99
04.05