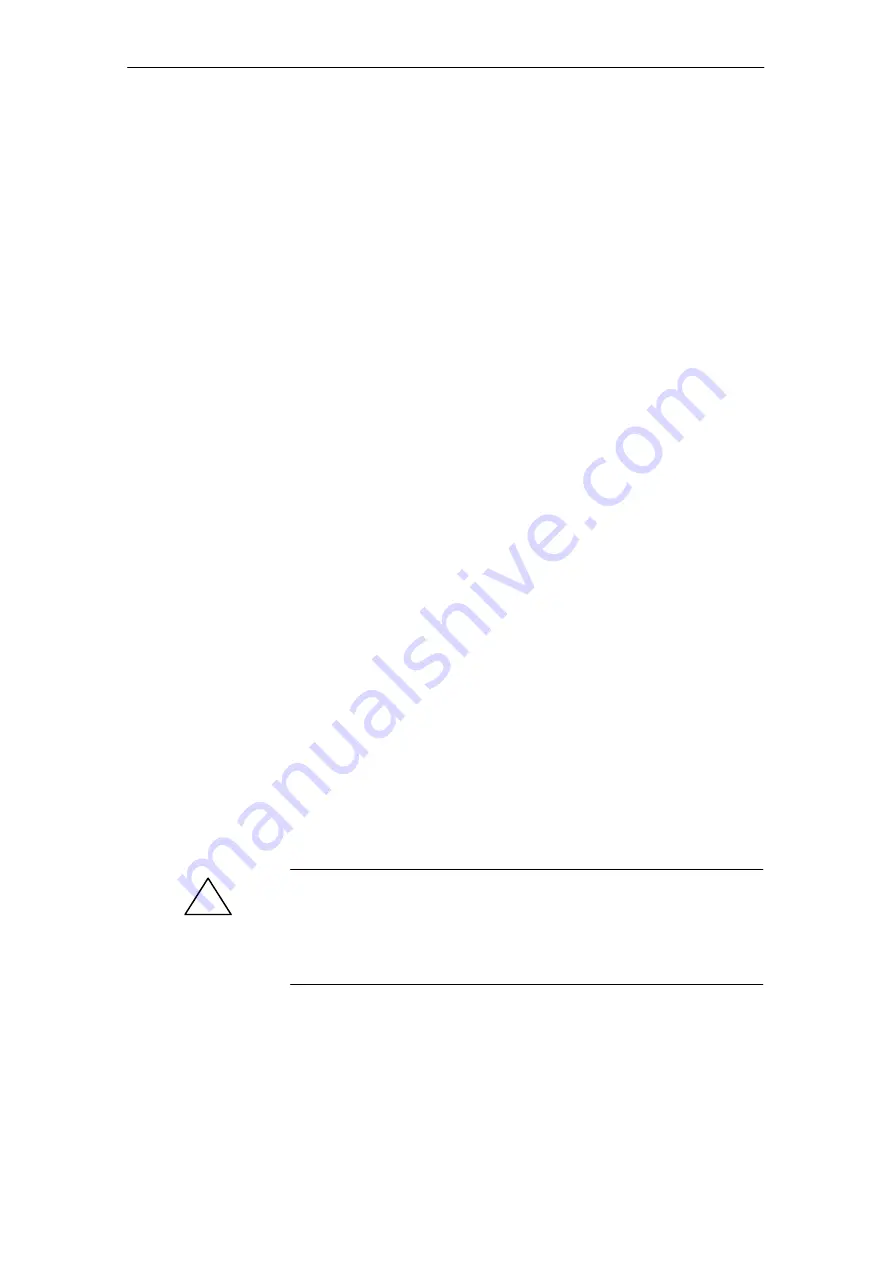
6
6.16 Rotor position synchronization/rotor position identification
6-616
Siemens AG 2005 All Rights Reserved
SIMODRIVE 611 universal Description of Functions (FBU) – 04.05 Edition
The following parameters are used for the rotor position synchroniza-
tion/rotor position identification:
P1011
IM configuration, actual value sensing
P1016
Angular commutation offset
P1017
Commissioning support
P1019
Current, rotor position identification
P1020
Maximum rotation, rotor position identification (SRM)
Maximum movement, rotor position identification (SLM)
P1075
Technique, rotor position identification (SRM, SLM)
P1076
Load moment of inertia RLI (SRM)
Load mass RLI (SLM)
The following diagnostics parameters are used rotor position synchro-
nization/rotor position identification:
P1734
Diagnostics, rotor position identification
P1736
Test, rotor position identification
P1737
Difference, rotor position identification
The following limitations/secondary conditions apply for the technique
based on both saturation and movement:
This technique can be used for both braked and non–braked mo-
tors.
The technique cannot be used for motors which are moving.
The current which is entered must be adequate in order to generate
a significant measuring signal.
The technique can only be started when the controller and pulses
are enabled as current must flow through the motor.
When using an absolute motor measuring system, the rotor position
identification can only be used to determine the commutation angle
offset (P1016).
The measurement and evaluation take approx. 250 ms.
!
Warning
W
hen the motors are not braked, the motor rotates or moves as a
result of the current impressed during the measurement. The
magnitude of the motion depends on the magnitude of the current and
the moment of inertia of the motor and load.
Parameter
overview
(refer to Chapter
A.1)
Limitations/
secondary
conditions
For the technique
based
on saturation
(P1075=1)
6 Description of the Functions
08.02