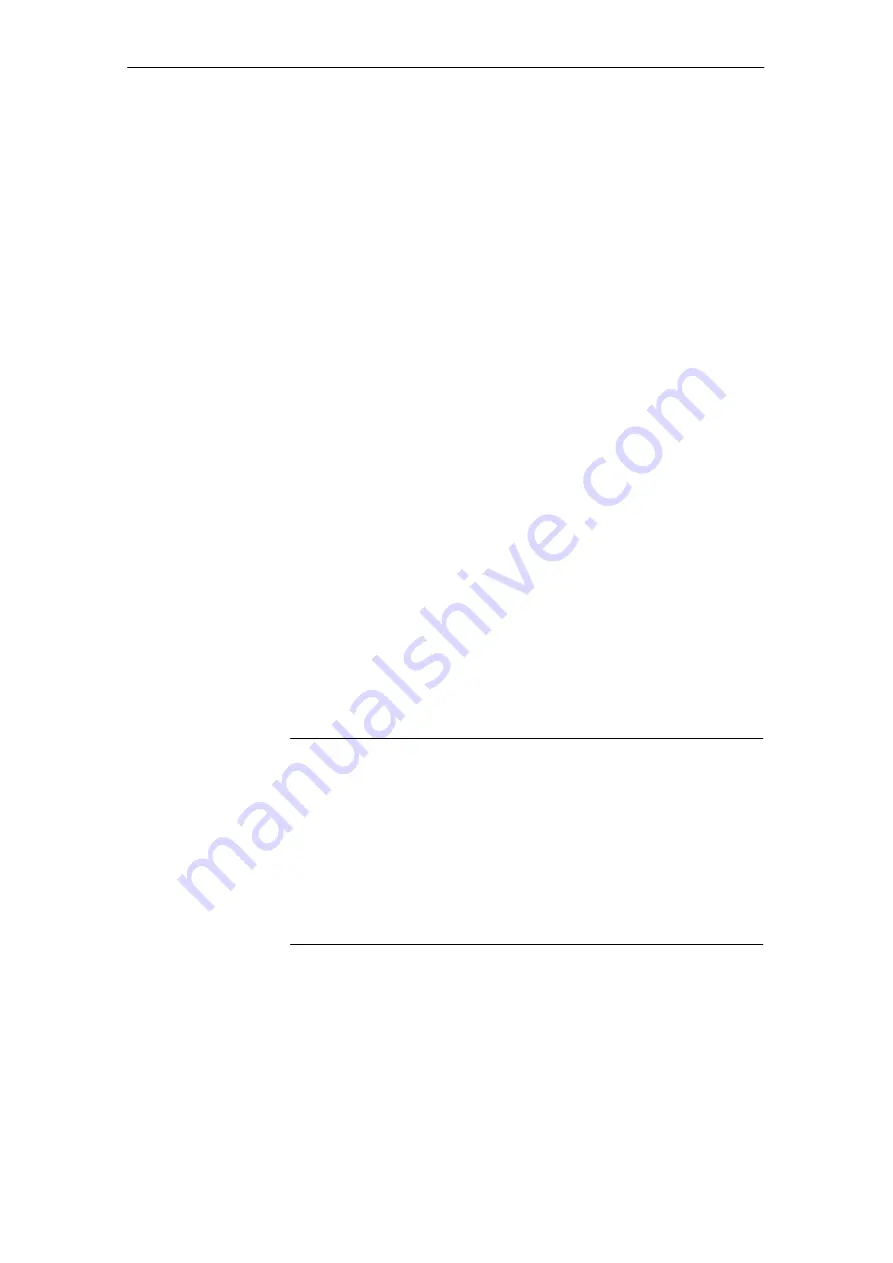
4
01.99
4.9
1FW6 build–in torque motors (from SW 6.1)
4-166
Siemens AG 2005 All Rights Reserved
SIMODRIVE 611 universal Description of Functions (FBU) – 04.05 Edition
Generally, a build–in torque motor comprises the following components:
Stator
This comprises an iron core and a three–phase winding. The wind-
ing is cast in polyurethane in order to better dissipate the power
losses. The motor can be force–cooled using a liquid heat ex-
changer (main heat exchanger) around its circumference.
Rotor
This is the reaction part of the motor. It comprises a cylindrical hol-
low steel shaft which has permanent magnets around its circumfer-
ence.
Cooling
The cooling version depends on the outer diameter.
Encoder system
– Absolute incremental encoder with EnDat
(e.g. RCN 723, Heidenhain)
– Incremental encoder (1V
pp
)
(e.g. RON 786, Heidenhain)
– Min. encoder pulse number z
min
= 2048
– Max. encoder pulse number z
max
= 65535
The prerequisites are as follows:
Control board
SIMODRIVE 611 universal (encoder interpolation depends on the
number of pulses of the incremental encoder)
Build–in torque motors should be set–up as feed motors
Maximum motor cable length = 50 m
Note
When build–in torque motors (direct drives) are connected to
controlled infeeds, an HFD commutating reactor with the appropriate
resistance must be used as otherwise electrical system oscillations
could occur.
When engineering the HFD commutating reactor with resistor, refer to:
Reference:
/PJU/
SIMODRIVE 611
Configuration Manual
Manufacturers Documentation
Components
of build–in torque
motors
System
prerequisites
4 Commissioning
02.03