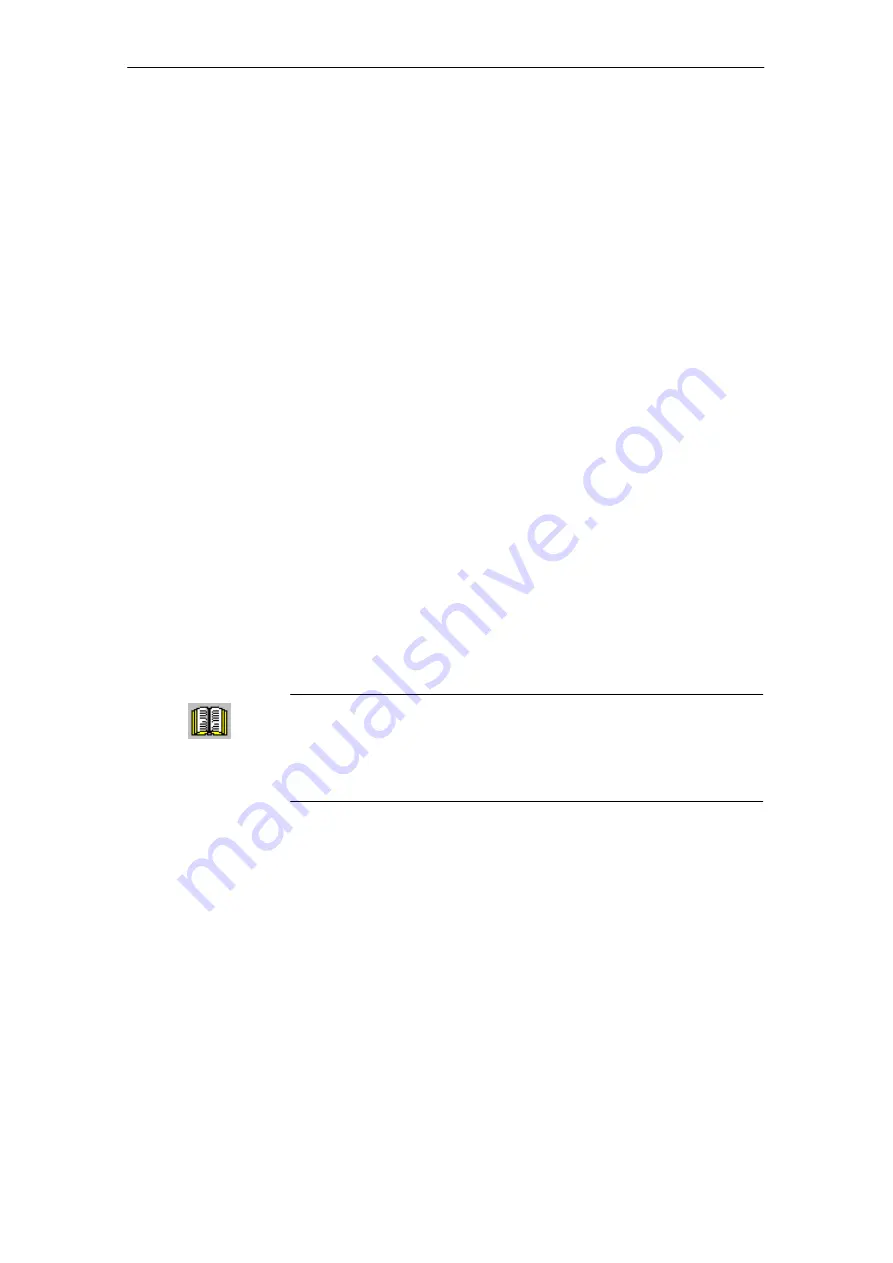
6
6.1
Operating mode, speed/torque setpoint (P0700 = 1)
6-336
Siemens AG 2005 All Rights Reserved
SIMODRIVE 611 universal Description of Functions (FBU) – 04.05 Edition
6.1.4
Optimizing the closed–loop current and speed controller
When optimizing the cascaded control structure (current, speed con-
troller), you generally proceed from the inside to the outside.
At the first commissioning or later, the current controller is pre–set
using the ”Calculate controller data” function, and generally no longer
has to be optimized.
However, all parameters for the current control loop can be adapted via
the expert list of the ”SimoCom U” tool.
At the first start–up (first commissioning) or later, the speed controller is
pre–set using the ”Calculate controller data”.
This speed controller setting is calculated for a motor operating under
no–load conditions, and corresponds to a ”safe” setting.
In order to be able to fully utilize the dynamic performance of the drive
including the mechanical system, some post–optimization will be nec-
essary.
Optimizing using the ”SimoCom U” tool
The controller setting for ”SIMODRIVE 611 universal” can be auto-
matically executed using the ”SimoCom U” tool (only in online oper-
ation).
Call:
Press the ”Execute automatic controller setting” button under ”Con-
troller” and execute the steps offered.
Reader’s note
Recommendation when optimizing the controller:
Optimize the control loop with ”SimoCom U” and the ”Execute
automatic controller setting” function.
Optimization using the display and operator control unit:
– Remove write protection ––> set P0651 to 4
– Increase the proportional gain Kp (P1407:8) until the motor
makes a whistling sound
– Reduce the proportional gain Kp (P1407:8) until this whistling
sound disappears
– The integral action time T
N
(P1409:8) can be retained
Optimizing the
current controller
Optimization
speed controller
6 Description of the Functions
01.99