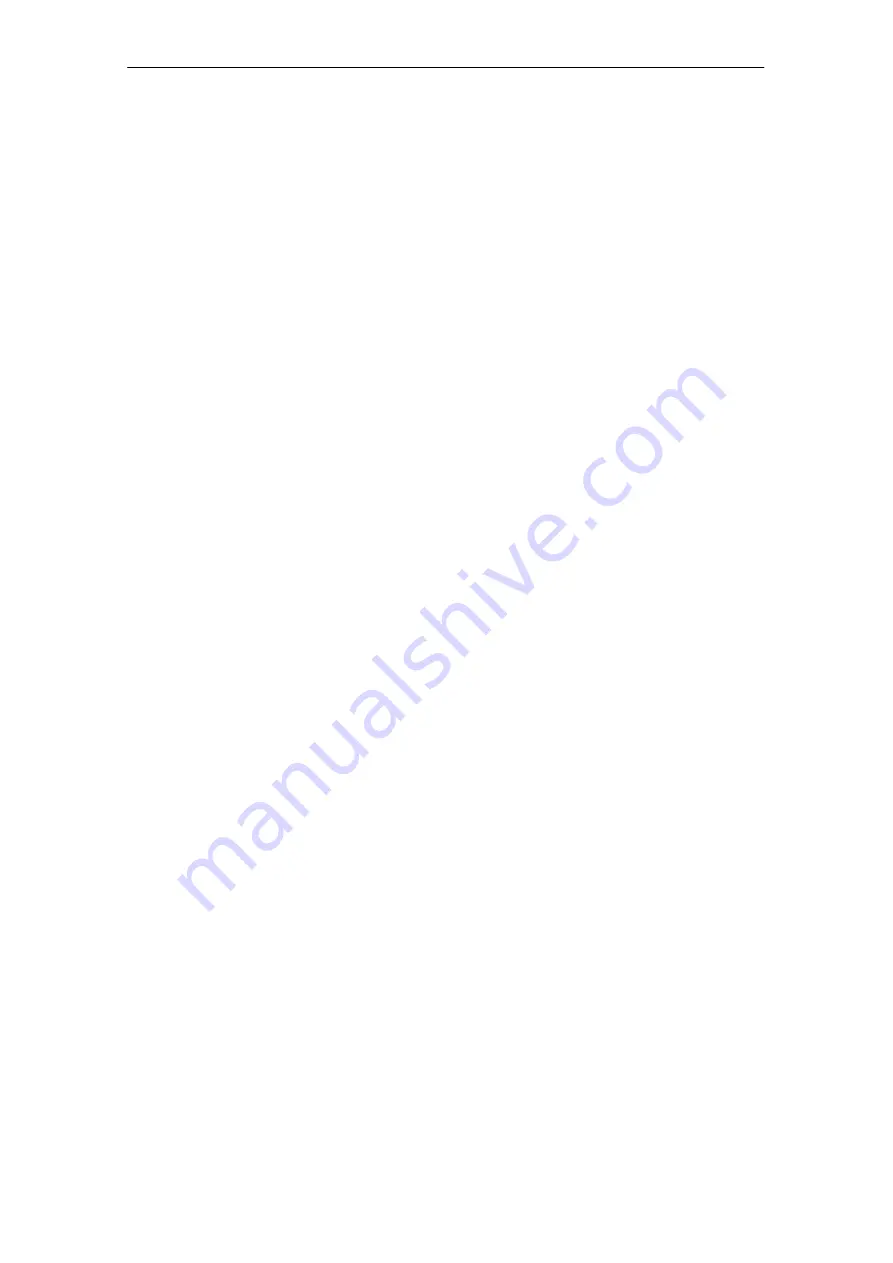
7
7.3
List of faults and warnings
7-662
Siemens AG 2005 All Rights Reserved
SIMODRIVE 611 universal Description of Functions (FBU) – 04.05 Edition
515
Power module temperature, exceeded
Cause
The power section temperature is sensed using a temperature sensor
on the heatsink. The drive is immediately shut down 20 seconds after
the heatsink temperature alarm in order to prevent the power section
being thermally destroyed (regenerative stop).
Remedy
Improve the drive module cooling, e.g. using:
– Higher airflow in the switching cabinet, possibly cool the ambient air
of the drive modules
– Avoid many acceleration and braking operations which follow quickly
one after the other
– Check that the power section for the axis/spindle is adequate,
otherwise use a higher-rating module
– Ambient temperature too high (refer to the Configuration Manual)
– Permissible installation altitude exceeded (refer to the Configuration
Manual)
– Pulse frequency too high (refer to the Configuration Manual)
– Check fan, if required, replace
– Maintain the minimum clearance above and below the power section
(refer to the Configuration Manual)
Acknowledgement POWER ON
Stop response
parameterizable
591
Pos.contr.clock cycle not equal to DP clock cycle/mas-
ter applic. clock cycle
Cause
For a 2-axis module, one axis is in the n-set mode and one axis in the
positioning mode. For the axis in the n-set mode, a position controller
clock cycle (of the master) is entered via the clock-cycle synchronous
Profibus or the bus interface. This position controller clock cycle differs
from the parameterized position controller clock cycle (P1009) of the
axis in the positioning mode. The position controller clock cycle of the
master is obtained, in the n-set mode, from the DP clock cycle (Tdp) or
the clock cycle of the bus interface multiplied by the time grid Tmapc.
Remedy
For a clock cycle synchronous PROFIBUS (isochronous) or the bus
interface, the clock cycles configured for the bus (parameterization) are
aligned with the position controller clock cycle P1009 from the position-
ing axis and n-set axis.
Acknowledgement POWER ON
Stop response
STOP II
7 Fault Handling/Diagnostics
01.99
04.05