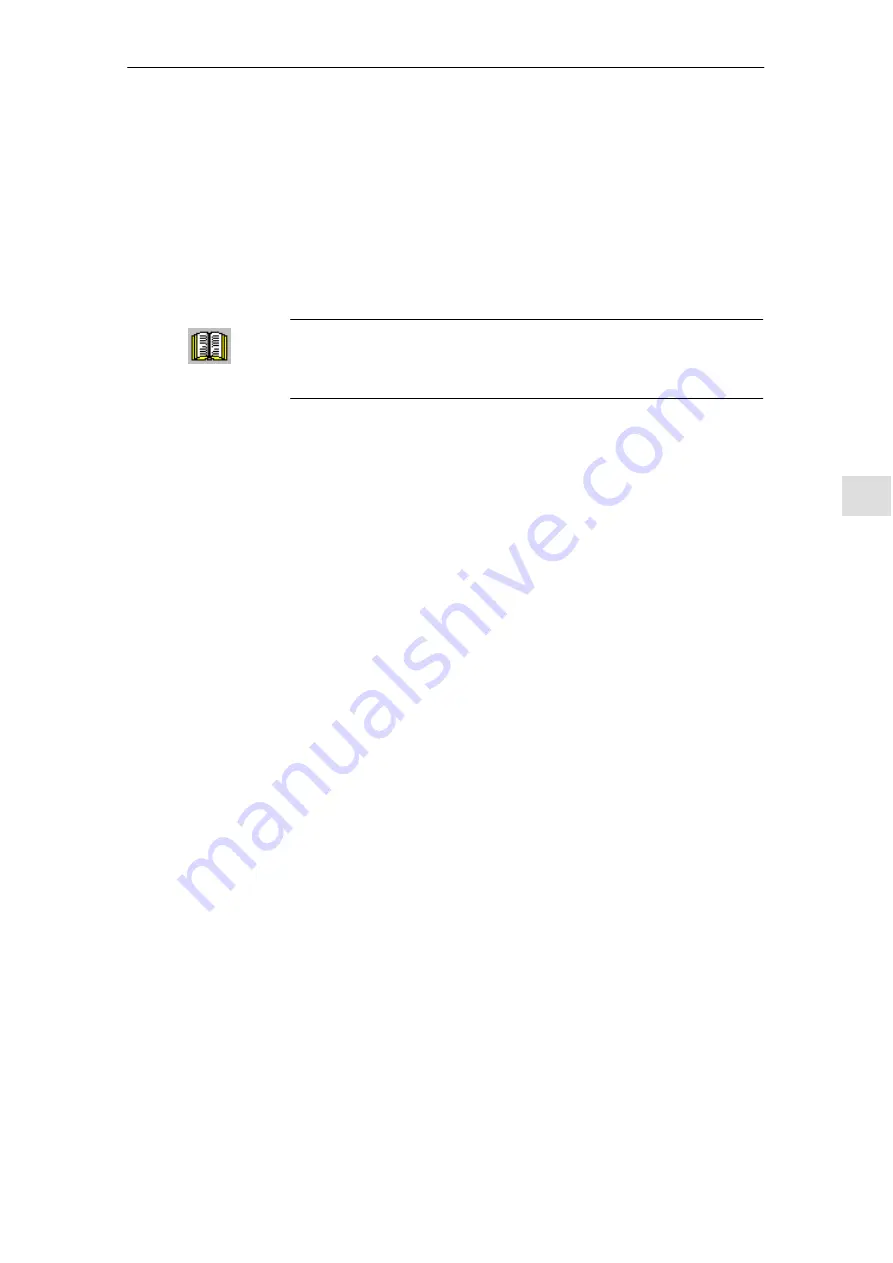
5
5.3
Basic functions of the non–cyclic data transfer
5-209
Siemens AG 2005 All Rights Reserved
SIMODRIVE 611 universal Description of Functions (FBU) – 04.05 Edition
Using PROFIdrive, it is possible to transfer parameters via DPV1 using
non–cyclic communications. The parameter definition and parameter
access via the DPV1 mechanism is defined in the PROFIdrive parame-
ter model, which is part of the PROFIdrive Profile Version 3.
The function blocks and project examples for SIMATIC S7 can be used
to transfer drive parameters in a non–cyclic fashion:
Product
Order No. (MLFB):
Drive ES SIMATIC
6SW1700–5JC00–2AA0
Note for the reader
Reference:
/KT654/, PROFIdrive–Profile Drive Technology,
Draft Version 3.1 July 2002, (Chapter 3.4)
A protocol has been defined for accessing parameters which comprises
tasks and the associated responses. The tasks are non–cyclically
transferred using the DPV1 utility ”write data” and the responses with
”read data”. Several drive parameters (e.g. traversing block) can be
simultaneously accessed using a task/response.
A DPV1 parameter task and a DPV1 parameter response with individ-
ual fields is defined and documented in the PROFIdrive profile.
When reading and writing parameters, that, depending on the current
configuring of the drive, are not valid – e.g. P1083 is only valid for in-
duction motors, however, a synchronous motor is configured – then the
Siemens–specific DPV1 error code 0x65 (parameter presently de–acti-
vated) is output.
Values of signal parameters (50000–type parameters) can only be read
if this was configured in the PROFIBUS telegram (P0915, P0916). A
negative acknowledgement (DPV1 error code 0x65) is output when
reading signal parameters using non–cyclic data transfer that were not
configured in the Profibus Telegram.
The parameters, defined by the profile, are documented in a list form
in the PROFIdrive profile.
This includes both parameters with the implementation rule ”manda-
tory”, i.e. parameters that are absolutely necessary in order to be in
conformance with the profile as well as parameters with the imple-
mentation rule ”optional” .
Parameter descriptions can be read so that now a master knows which
parameters a drive knows and the properties which each of these pa-
rameters has.
Parameter access
via DPV1
Parameters,
reading/writing
DPV1 (from SW
6.1)
Read the
parameter
description DPV1
(from SW 6.1)
5 Communications via PROFIBUS DP
08.99
08.02
07.03