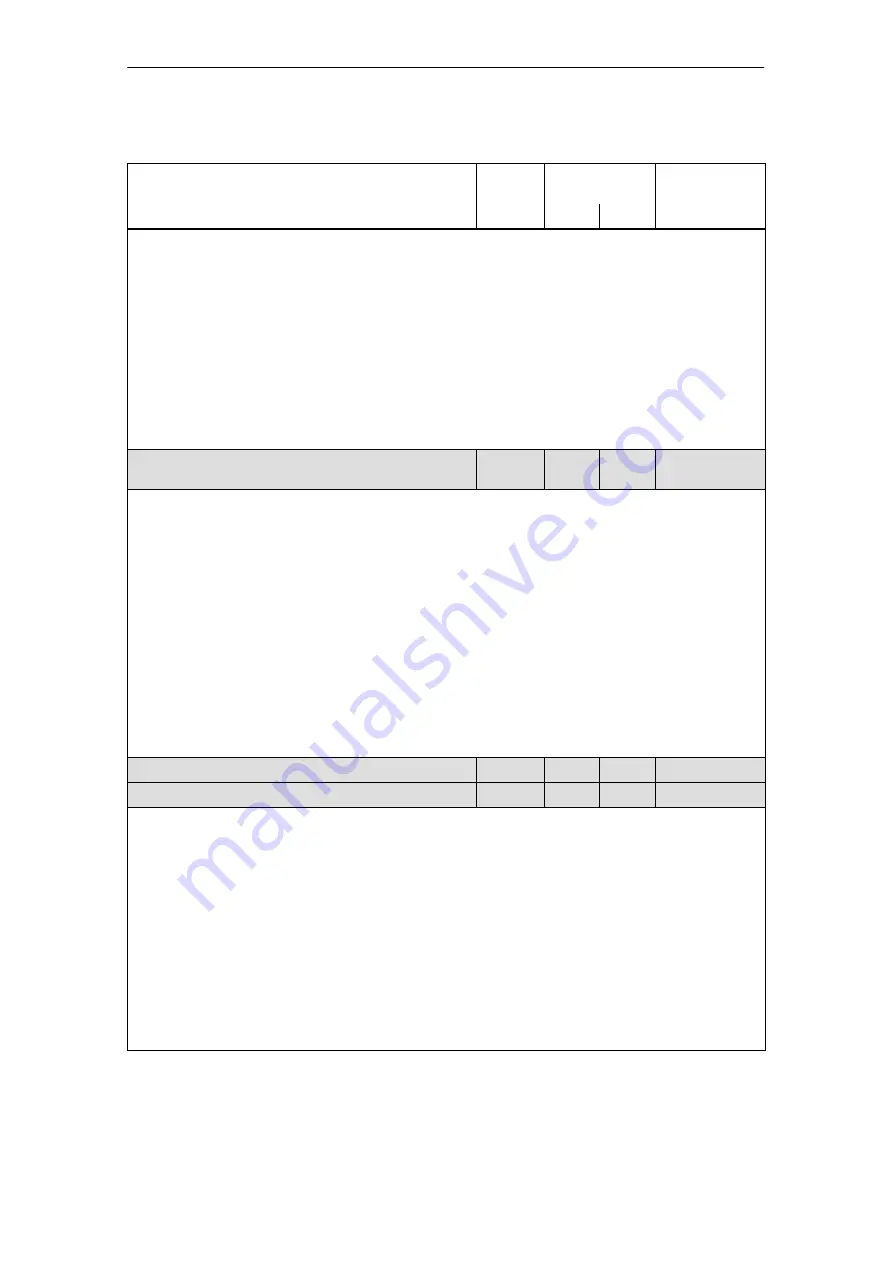
6
6.4
Input/output terminals of the control board
6-494
Siemens AG 2005 All Rights Reserved
SIMODRIVE 611 universal Description of Functions (FBU) – 04.05 Edition
Table 6-45
List of input signals, continued
Operating
mode
Signal name, description
PROFIBUS bit
pos
n–set
Fct. No.
Note:
This function must be executed via input terminal I0.x (fast input).
Activate the ”equivalent zero mark” function for an incremental measuring system:
–
refer to P0174
–
refer to P0879.13 or P0879.14
The equivalent zero mark is identified as a function of the direction.
The actual value can be inverted using P1011.0, P0231 and P0232.
–
There is no inversion, if none or 2 of these parameters are set to invert
––> increasing (decreasing) position actual value corresponds to a positive (negative) direction
–
The value is inverted, if one or all 3 parameters are set to invert.
––> increasing (decreasing) position actual value corresponds to a negative (positive) direction
Flying measurement/length measurement
(from SW 3.1)
80
x
–
–
The encoder actual value can be retrieved via an input with this function.
0/1 signal or
1/0 signal
The actual encoder value is retrieved
Note:
This function must be executed via the fast I0.x input.
The function is only available for ”Motion Control with PROFIBUS–DP”.
––> refer under the index entry ”Encoder interface (from SW 3.1)”
The function is only available for the control board ”SIMODRIVE 611 universal” from Order No.
6SN1118–xxxxx–0AA2 and control board ”SIMODRIVE 611 universal HR”.
This function cannot be executed for spindle positioning active (P0125=1).
The measuring probe signal is defined depending on the parameterized edge in control word
Gx_STW.0/1 (refer to Chapter 5.6.4).
The edge clearance must be at least 150 ms. Measuring probe edges that are received faster (low
clearance between signals) cannot be evaluated.
Plus hardware limit switch (NC contact)
81
x
1)
x
–
Minus hardware limit switch (NC contact)
82
x
1)
x
–
A hardware limit switch can be connected at an input with this function in order to limit the traversing
range in either the positive or negative direction.
1/0 signal
The plus or minus hardware limit switch has been actuated
The axis is braked. The drive remains in closed–loop control.
In the pos mode:
The axis can be moved away from the limit switch in the jog mode.
In the n–set mode (from SW 8.1):
The axis can be moved away from the limit switch using a setpoint that is opposite to the
approach direction.
1 signal
No significance
Note:
1) from SW 8.1
––> refer under the index entry ”hardware limit switch”
6 Description of the Functions
01.99
! 611ue diff !
08.01
06.04