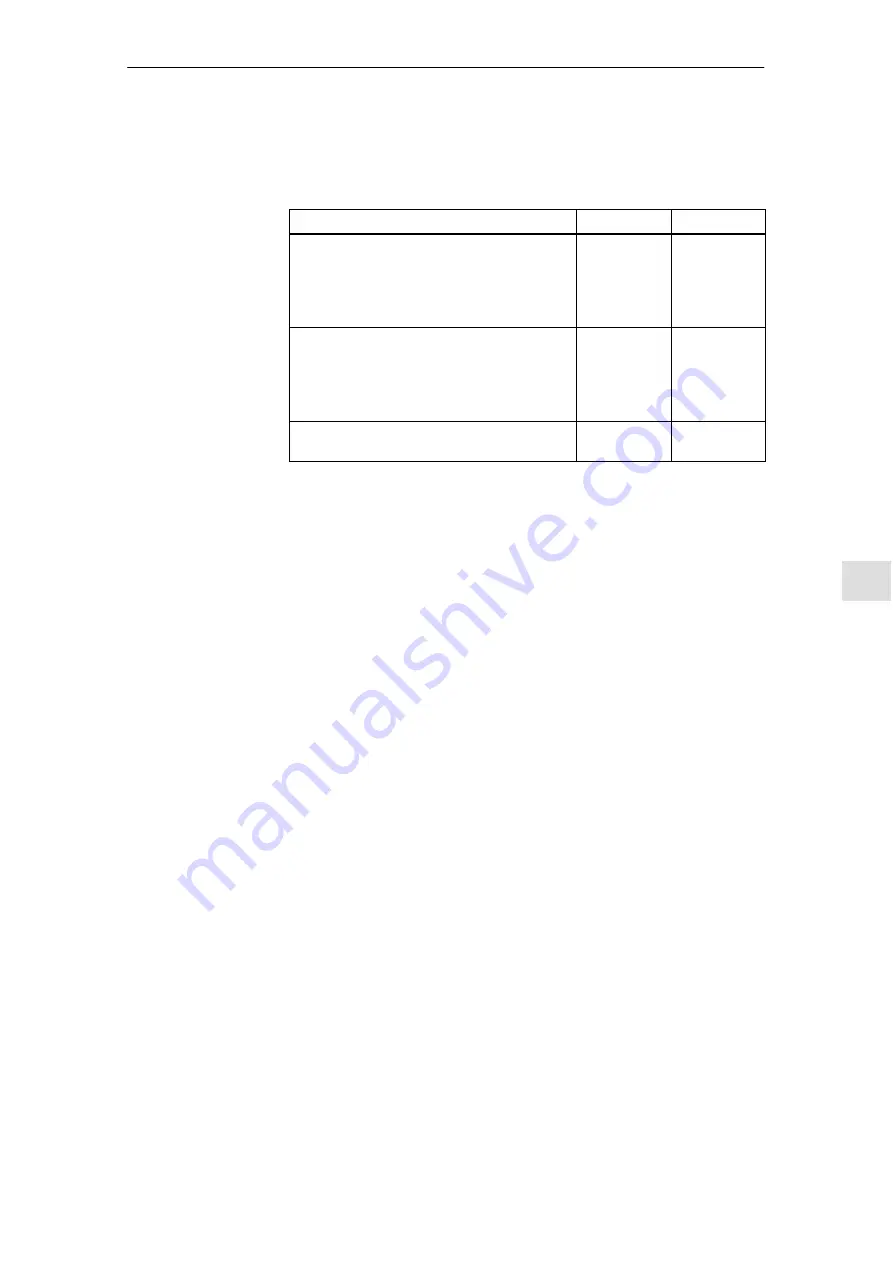
6
6.15 Spindle positioning (from SW 5.1)
6-611
Siemens AG 2005 All Rights Reserved
SIMODRIVE 611 universal Description of Functions (FBU) – 04.05 Edition
P0250 and P0174 must be set to the existing measuring system.
Table 6-72
Encoder configuration for spindle positioning
P0250
P0174
Indirect measuring system (motor encoder)
with encoder zero mark
In addition, the gearbox ratio must be entered
into P0237 (encoder revolutions) and P0238
(load revolutions)
0
1
Indirect measuring system (motor encoder)
with external zero mark
In addition, the gearbox ratio must be entered
into P0237 (encoder revolutions) and P0238
(load revolutions)
0
2
Direct measuring system with encoder zero
mark
1
1
It is possible to select position actual value inversion using parameter
P0231.
For spindle drives with gearboxes, an external zero mark
(BERO) should be provided as reference point if the spindle has to be
positioned.
For multi–stage gearboxes, the gearbox stage ratios must be taken into
account. The ratios must be entered via parameter P0237 (gearbox
revolutions) and P0238 (load revolutions). For parameter set 0, the ra-
tio of the first gearbox stage can be defined using SimoCom U in the
menu screen ”Mechanical system” (1:1 is the basic setting).
Additional gearbox stage ratios must be entered using the Expert list
(P0237:x, P0238:x; x = 1 to 7).
Example:
If a changeover gearbox with a ratio of 1:1 or 1:4 is used, for the 1st
gearbox stage, parameters P0237:0 and P0238:0 remain unchanged
(because 1:1) and for the ratio 1:4, the following values are entered into
parameters P0237:1 = 1 and P0238:1 = 4. These values become valid
after ”Power on”.
The ratio can be checked using parameter P0132. In this case, the
distance between two zero marks is displayed in degrees. If the values
which are displayed deviate from 360 degrees, then the gear–up/gear–
down ratio was not correctly parameterized.
Encoder
configuration
Spindle drive with
gearbox (BERO)
6 Description of the Functions
01.99
02.02
! not 611ue !