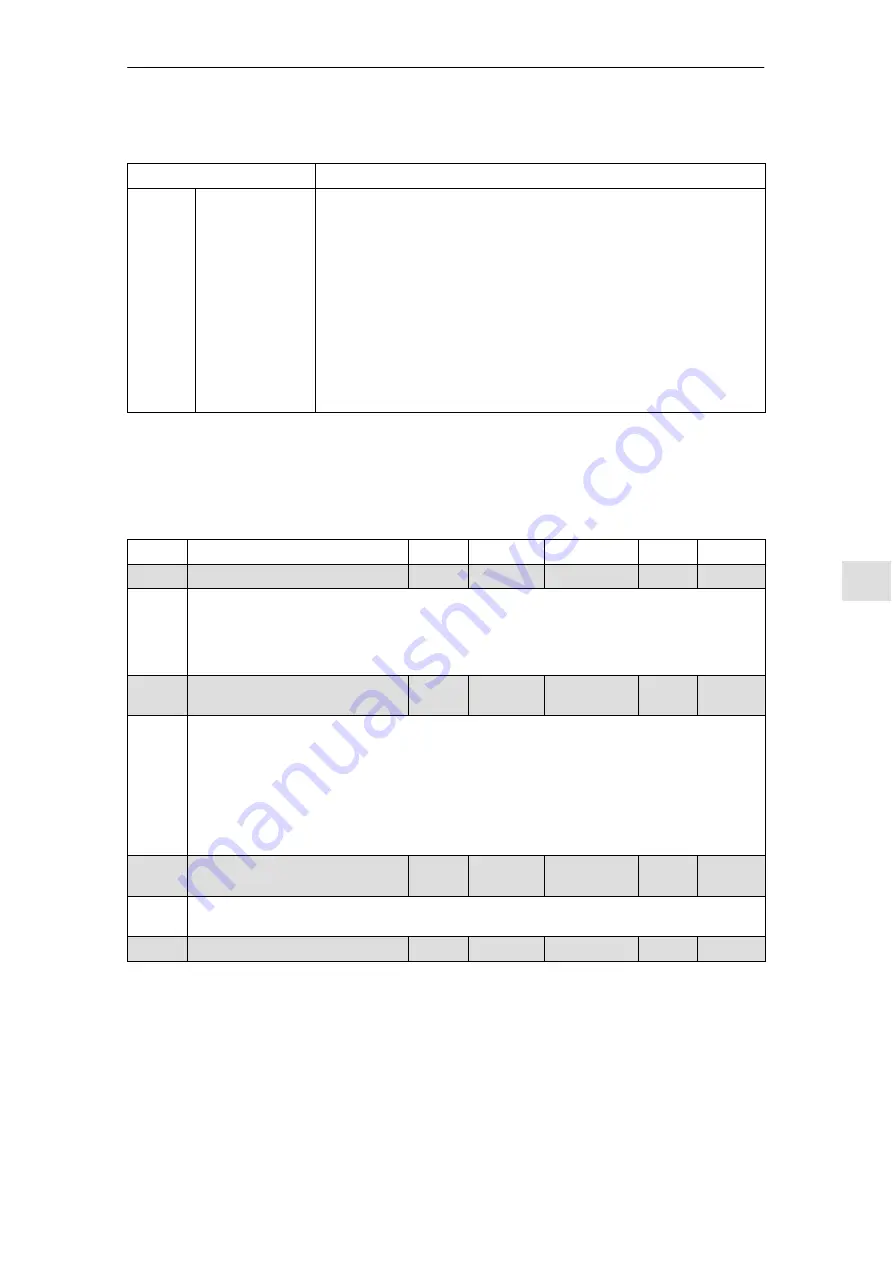
6
6.2
Positioning mode (P0700 = 3, from SW 2.1)
6-359
Siemens AG 2005 All Rights Reserved
SIMODRIVE 611 universal Description of Functions (FBU) – 04.05 Edition
Table 6-10
Restrictions for axis/encoder, continued
Axis/encoder
Restrictions
Rotary
axis
en-
dlessly
rotating
(modulo
rotary
axis)
Incremental en-
coder
For incremental encoders, the above condition is not checked.
If the mechanical machine design does not fulfill the condition above,
then the rotary axis must be re–referenced after each endless operation
and when being powered up.
The following is valid when evaluating the zero mark:
The evaluated zero mark must always be located at the same load
side position of the modulo range (the ratio is taken into account).
For several zero marks, one must be defined for evaluation (e.g. set
via cams).
If it is not possible to reference the system using the encoder zero
mark, then the equivalent zero mark must be used (e.g. BERO at the
input with the ”equivalent zero mark” function).
Table 6-11
Parameters for the encoder adaptation
No.
Name
Min.
Standard
Max.
Units
Effective
1027.4
IM configuration, encoder
–
–
–
hex
PO
The motor encoder type is specified using P1027, bit 4.
Bit 4
Linear measuring system
= 1
Linear motor encoder
= 0
Rotary motor encoder
1005
IM encoder pulse number (SRM,
ARM)
0
2048
65 535
–
PO
The parameter is only relevant for rotary motor encoders.
For encoders with voltage signals sin/cos 1 Vpp (rotary motor encoder)
The encoder pulses per revolution are specified using this parameter.
for resolvers
The parameter has no significance.
The ”fictitious” encoder pulses are internally calculated from the pole pair number (P1018)
of the resolver.
0236
Leadscrew pitch
1
10 000
8 388 607
MSR/
rev
PO
The spindle pitch is specified in this parameter (e.g. ballscrew spindle with 10 mm/revolution
and metric dimension system ––> P0236 = 10 000 MSR/rev).
0237:8
Encoder revolutions
1
1
8 388 607
–
PO
Parameter
overview
6 Description of the Functions
01.99
! not 611ue !