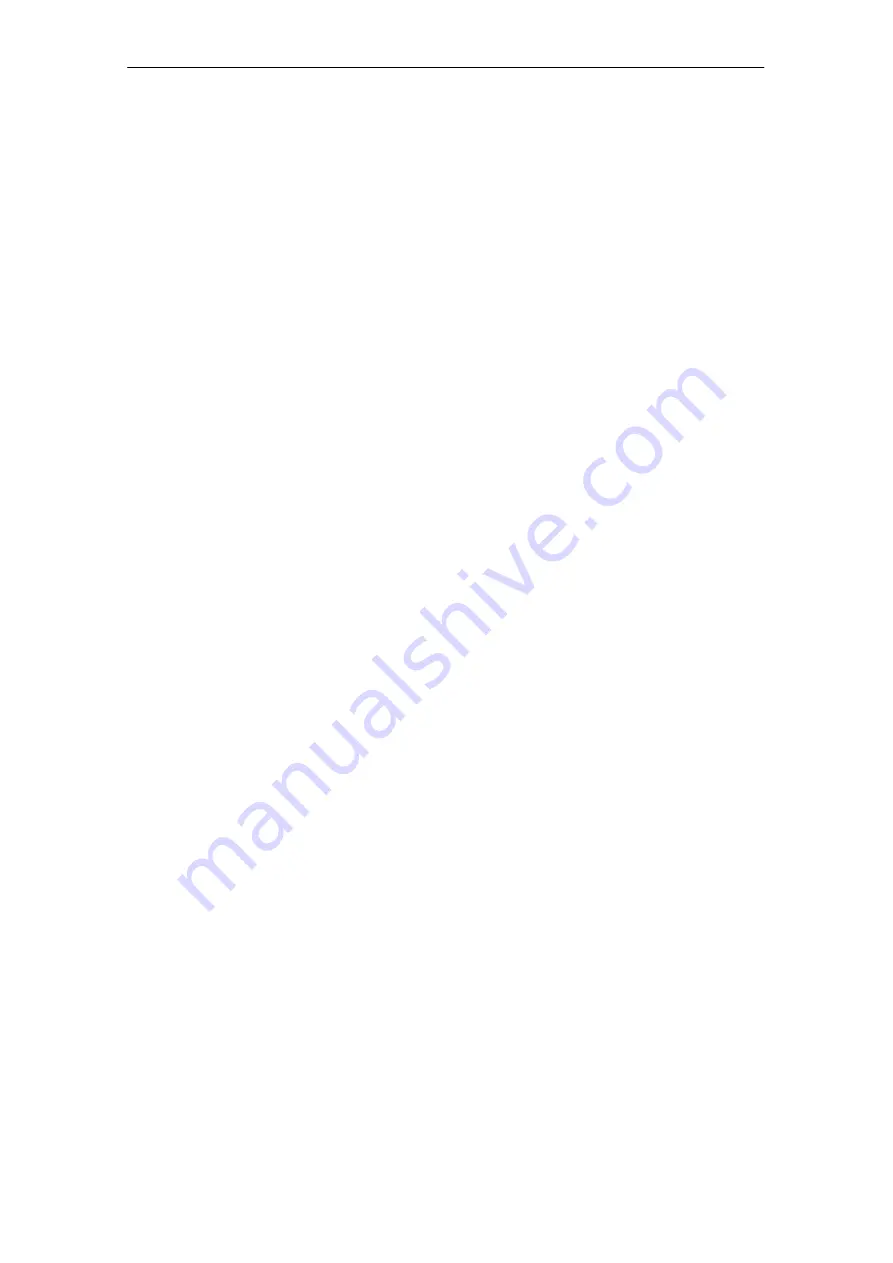
4
01.99
4.10 Linear motors (1FN1, 1FN3 motors)
4-178
Siemens AG 2005 All Rights Reserved
SIMODRIVE 611 universal Description of Functions (FBU) – 04.05 Edition
8. Set the setpoint limit switch
– P0314, P0315 and P0316
(refer under the index entry ”Software limit switch”)
9. Optimizing the axis controller settings
Note:
Generally, the automatic controller setting for linear motors does not
provide adequate results, as the measuring system mounting plays
a significant role in the closed–loop control characteristics.
– Current and speed controllers
(refer to Chapter 6.1.4)
– Position controller
(refer under the index entry
”Kv factor”)
10.Check and set the rotor position identification
To check the rotor position identification, using a test function,
you can determine the difference between the calculated rotor
angle position and that actually used by the closed–loop control.
Proceed as follows:
– Start the test function several times and evaluate the difference
Start
Set P1736 (test rotor position identification) to 1
Difference
P1737 (difference, rotor position identification)
= _ _ _ _ , _ _ _ _ , _ _ _ _ , _ _ _ _ , _ _ _ _
– Is the spread of the measured values less than 10 degrees elec-
trical?
Yes:
OK
No:
Increase P1019 (e.g. by 10 %)
and repeat the measurements
If OK after having repeated the measurements, then the
angular commutation offset can be re–determined:
For an incremental measuring system
(incremental – one zero mark):
as for Point 5. (determining the angular commutation off-
set)
For an absolute measuring system:
Power–down the drive (POWER ON–RESET)
Power–up the drive with the pulse or controller enable
signals switched–out
Set P1017.0 to 1
Switch–in the pulse and enable signals
––>
The angular offset is automatically
entered into P1016
––>
Fault 799
(Save to FEPROM and HW–RESET required)
is displayed
Save to FEPROM and carry–out a HW–RESET
For incremental measuring system
(incremental – no or several zero marks):
Save to FEPROM and carry–out a HW RESET
4 Commissioning