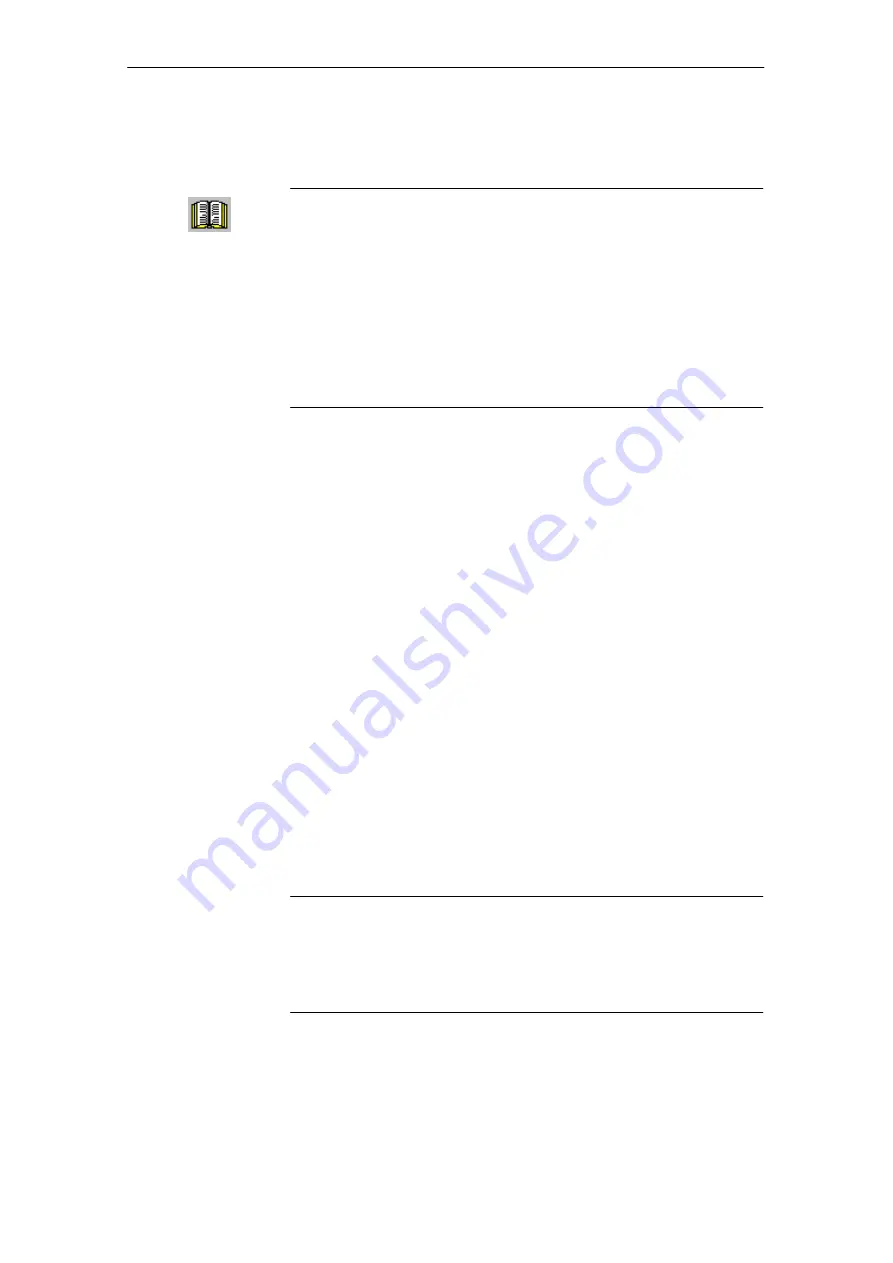
4
01.99
4.7
Induction motor operation with induction motor
4-148
Siemens AG 2005 All Rights Reserved
SIMODRIVE 611 universal Description of Functions (FBU) – 04.05 Edition
4.7.3
Motor data optimization, steps 1 to 4
Reader’s note
What happens to the faults occurring during motor data optimization?
Faults, which occur during the commissioning steps, are written into
P1084 as fault code (refer to the parameter list in Chapter A.1).
Prerequisites for the commissioning steps 1 to 4:
Switch in the pulse, controller and ramp–function generator enable
signal
Remove write protection (P0651 = 8)
Set the converter switching frequency (P1100) to 4 or 8 kHz
From SW 5.1, the ”SimoCom U” start–up tool supports motor data opti-
mization.
After ”motor data optimization” has been selected, a menu is displayed
in which, the following optimization steps can be selected one after
another from the ”Settings” selection box. These optimizing steps can
be started using the ”Start” button:
1. Step 1: Determining the resistances and reactances
2. Step 2: Finely defining the no–load current, magnetizing field reac-
tance
3. Step 3: Determining the speed at the start of field weakening
4. Step 4: Determining the moment of inertia
For the listed parameters, the results of the optimization steps are dis-
played, up–to–date, in the menu screen.
The motor can also be optimized as follows using parameter settings.
Determine the resistance and reactance values of the motor and an
improved no–load current value.
Note
The motor does not move and may not move during this
measurement.
Monitoring is not possible, as the induction motor does not have an
encoder.
Optimizing using
”SimoCom U”
Optimizing with
the parameter
settings
Commissioning
step 1
4 Commissioning
02.02