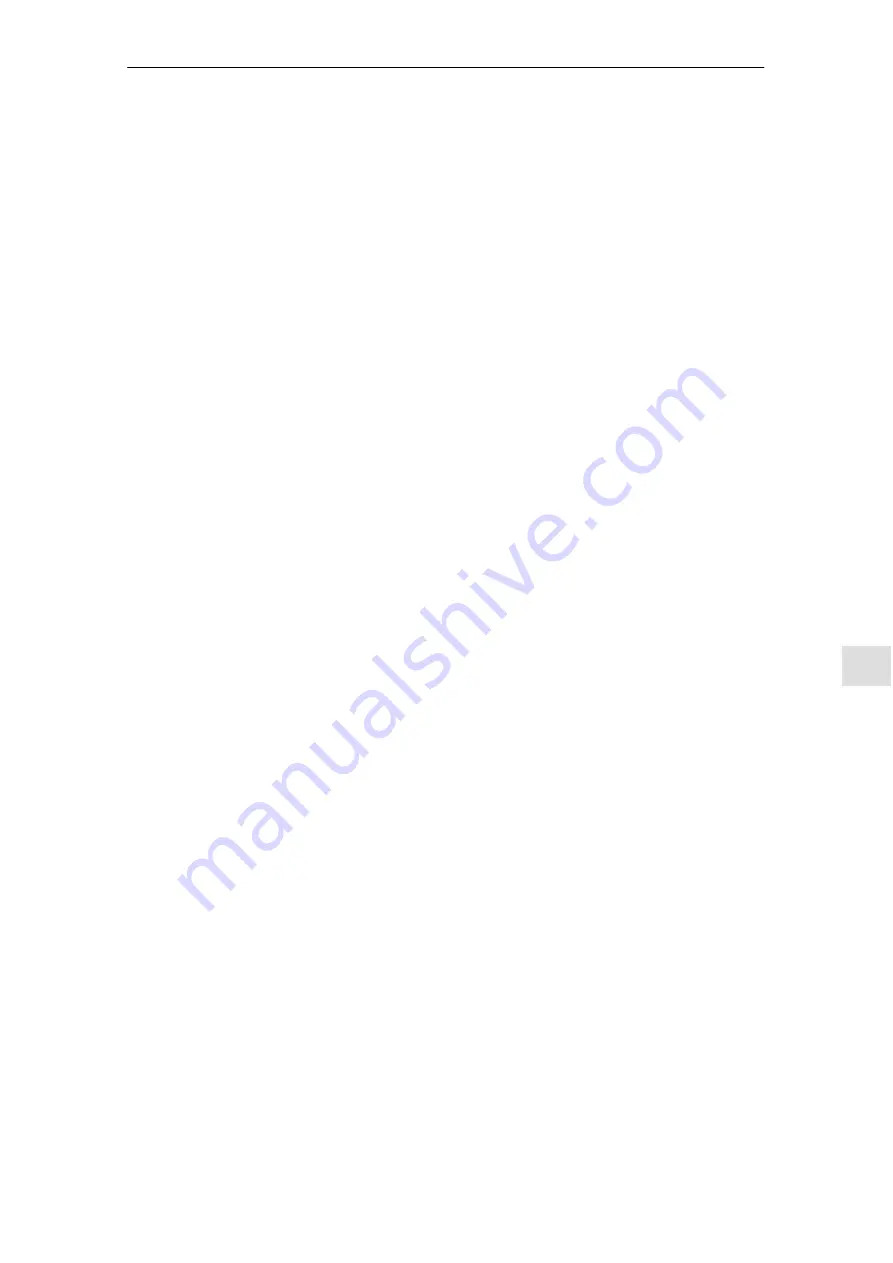
7
7.3
List of faults and warnings
7-679
Siemens AG 2005 All Rights Reserved
SIMODRIVE 611 universal Description of Functions (FBU) – 04.05 Edition
719
Motor not parameterized for delta operation
Cause
When the star-delta changeover is activated using P1013, the motor is
not parameterized for delta operation (motor 2).
Remedy
Check and enter the parameters for delta operation (motor 2).
Acknowledgement POWER ON
Stop response
STOP II (SRM, SLM) STOP I (ARM)
720
Invalid maximum motor speed
Cause
Due to the high maximum motor speed in P1401 and the speed con-
troller cycle in P1001, high partial speeds can occur which can result in
a format overflow.
Remedy
Check and correct P1401 and P1001.
The drive software is designed for large reserve margins, so that the
displayed alarm can only occur as a result of a parameterizing error.
Example:
For a speed controller cycle time of 125 microseconds, a motor speed
of 480 000 RPM can still be processed correctly!
Acknowledgement RESET FAULT MEMORY
Stop response
STOP II (SRM, SLM) STOP I (ARM)
721
Spindle speed too high
Cause
The modulo value can no longer be correctly calculated as a result of
the high spindle speed and the interpolation clock cycle (P1010).
Remedy
Shorten the interpolation clock cycle.
If possible, increase the modulo range of the rotary axis (P0242).
Calculating the spindle speed limit [RPM] = 7 / IPO clock cycle[ms] x
60 x 1000 (for the modulo range, 360 degrees = 1 spindle revolution)
Example:
IPO clock cycle = 4ms, for max. 7 revolutions ( up to 7 x modulo range)
per IPO clock cycle a maximum spindle speed of 105000/min is ob-
tained.
Acknowledgement RESET FAULT MEMORY
Stop response
STOP II (SRM, SLM) STOP I (ARM)
723
Axial deviations in STS configuration
Cause
On a 2-axis module, the gating unit configuration (P1003) is different
for the two gating units.
Remedy
Check P1003 and set the bits for the two module axes the same (do
not change the standard setting, this represents the optimum configura-
tion).
Acknowledgement POWER ON
Stop response
STOP II (SRM, SLM) STOP I (ARM)
7 Fault Handling/Diagnostics
01.99
04.05