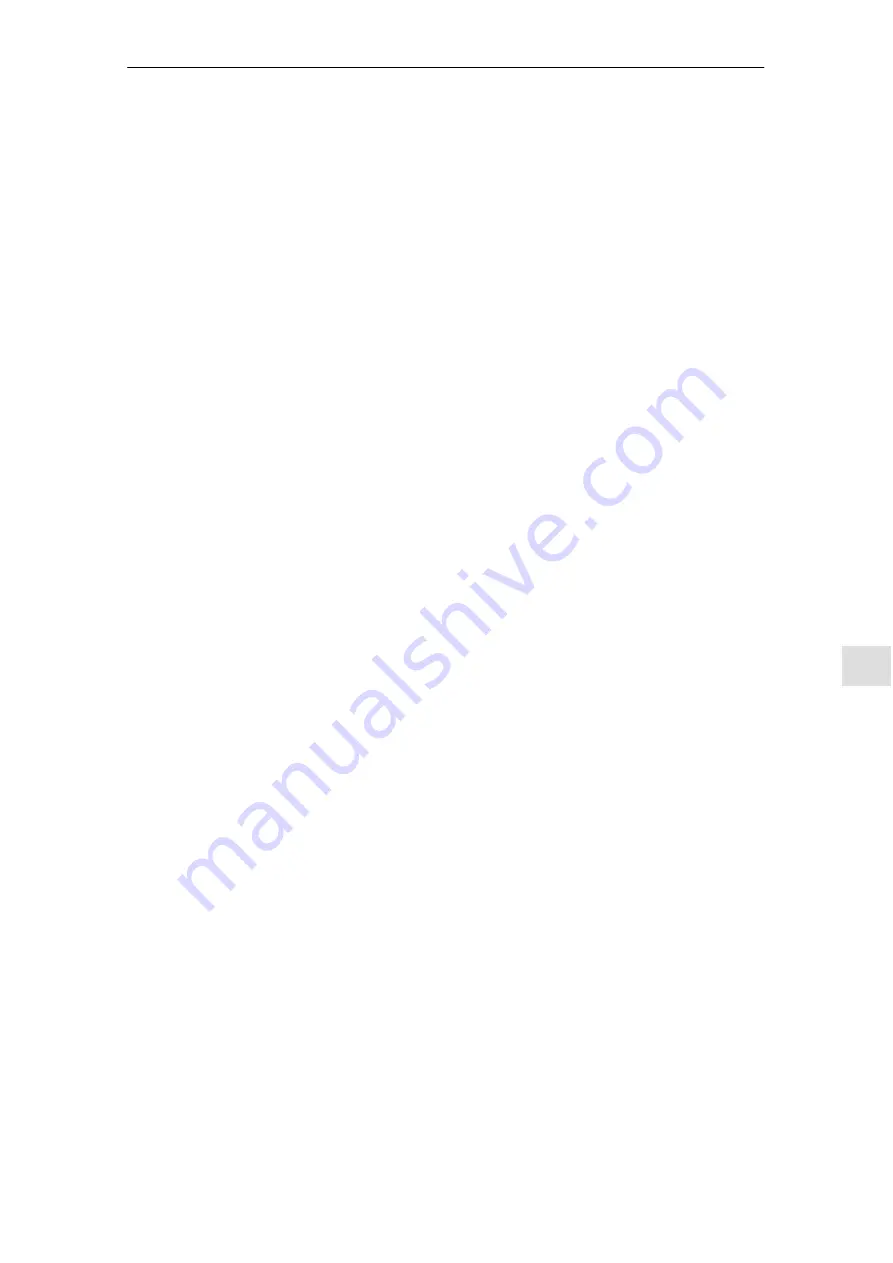
7
7.3
List of faults and warnings
7-677
Siemens AG 2005 All Rights Reserved
SIMODRIVE 611 universal Description of Functions (FBU) – 04.05 Edition
703
Invalid current controller cycle
Cause
An illegal value was entered in P1000.
Remedy
Enter a valid value in P1000.
Permissible values for P1000 are:
2 (62.5
µ
s) for single-axis positioning or for speed setpoint input
4 (125
µ
s) in each operating mode
Acknowledgement POWER ON
Stop response
STOP II (SRM, SLM) STOP I (ARM)
704
Invalid speed controller cycle
Cause
An illegal value was entered in P1001.
Remedy
Enter a valid value in P1001.
Permissible values for P1001 are 2 (62.5 us), 4 (125us), 8 (250us), 16
(500us).
Setting 2 (62.5us) is only permissible for single-axis operation.
Further, P1001 must be >= P1000.
Acknowledgement POWER ON
Stop response
STOP II (SRM, SLM) STOP I (ARM)
705
Invalid position controller cycle
Cause
The monitoring function identified a position controller cycle (P1009)
outside the permissible limits.
Remedy
Enter a valid value in P1009.
Permissible values for P1009 lie between 32 (1 ms) and 128 (4ms).
Further, the position control cycle must be a integral multiple of the
speed control cycle.
Acknowledgement POWER ON
Stop response
STOP II (SRM, SLM) STOP I (ARM)
706
Invalid interpolation cycle
Cause
The monitoring has identified an interpolation cycle (P1010) outside the
permissible limits, or an illegal ratio between the interpolation cycle and
the position controller cycle (P1009).
Remedy
Enter a valid value in P1010 or correct P1009.
Permissible values for P1010 lie between 128 (4ms) and 640 (20ms)
or, only for the 1-axis version, also 64 (2ms) if P1009 is also 64 (2ms).
Further, the interpolation cycle must be an integral multiple of the posi-
tion controller cycle.
Acknowledgement POWER ON
Stop response
STOP II (SRM, SLM) STOP I (ARM)
7 Fault Handling/Diagnostics
01.99
04.05