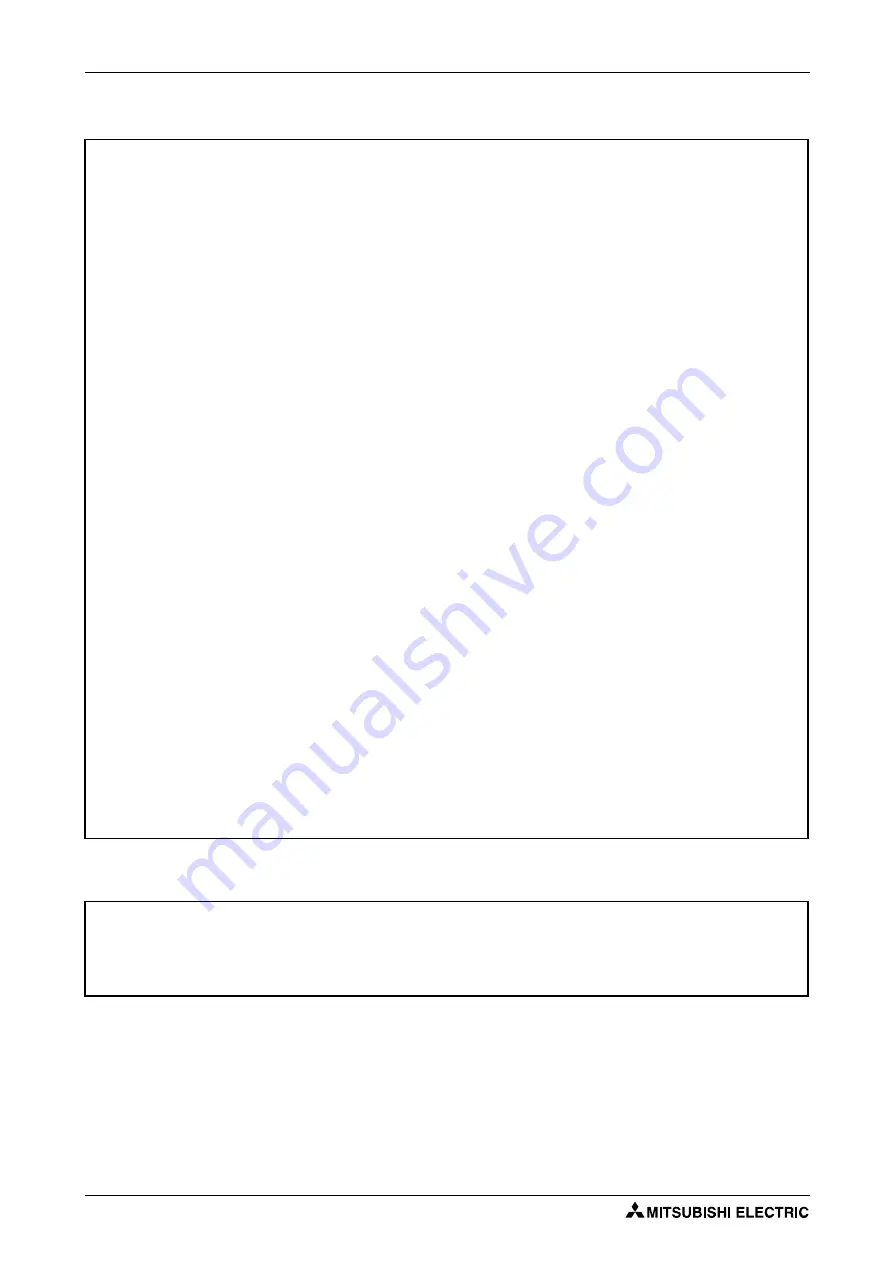
VI
Test operation and adjustment
E
CAUTION:
●
The electronic thermal relay function does not guarantee protection of the motor from
overheating. It is recommended to install both an external thermal and PTC thermistor for
overheat protection.
●
Do not use a magnetic contactor on the inverter input for frequent starting/stopping of the
inverter. Otherwise, the life of the inverter decreases.
●
Use a noise filter to reduce the effect of electromagnetic interference and follow the accepted
EMC procedures for proper installation of frequency inverters. Otherwise nearby electronic
equipment may be affected.
●
Take appropriate measures regarding harmonics. Otherwise this can endanger compensa-
tion systems or overload generators.
●
When driving a 400V class motor by the inverter, the motor must be an insulation-enhanced
motor or measures must be taken to suppress surge voltage. Surge voltage attributable to
the wiring constants may occur at the motor terminals, deteriorating the insulation of the
motor.
●
Use a motor designed for inverter operation. (The stress for motor windings is bigger than
in line power supply).
●
When parameter clear or all clear is performed, set again the required parameters before
starting operations. Each parameter returns to the initial value.
●
The inverter can be easily set for high-speed operation. Before changing its setting, fully
examine the performances of the motor and machine.
●
The DC braking function of the frequency inverter is not designed to continuously hold a
load. Use an electro-mechanical holding brake on the motor for this purpose.
●
Before running an inverter which had been stored for a long period, always perform inspec-
tion and test operation.
●
For prevention of damage due to static electricity, touch nearby metal before touching this
product to eliminate static electricity from your body.
●
Only one PM motor can be connected to an inverter.
●
A PM motor must be used under PM sensorless vector control. Do not use a synchronous
motor, induction motor, or synchronous induction motor.
●
Do not connect a PM motor in the induction motor control settings (initial settings). Do not
use an induction motor in the PM sensorless vector control settings. It will cause a failure.
●
In the system with a PM motor, the inverter power must be turned ON before closing the
contacts of the contactor at the output side.
E
CAUTION:
●
Before starting operation, confirm and adjust the parameters. A failure to do so may cause
some machines to make unexpected motions.
Summary of Contents for FR-A800
Page 2: ......
Page 4: ......
Page 22: ...Contents XVIII ...
Page 30: ...Related manuals Introduction 1 8 ...
Page 122: ...Connection of stand alone option units Installation and wiring 2 92 ...
Page 180: ...Basic operation procedure JOG operation Basic operation 4 32 ...
Page 934: ...Check first when you have a trouble Protective functions 6 46 ...
Page 1031: ...Appendix EC Declarations of Conformity FR A800 A 47 ...
Page 1032: ...EC Declarations of Conformity Appendix A 48 ...
Page 1033: ...Appendix EC Declarations of Conformity FR A800 A 49 ...
Page 1034: ...EC Declarations of Conformity Appendix A 50 ...
Page 1035: ...Appendix EC Declarations of Conformity FR A800 A 51 A 5 2 EMC Directive ...
Page 1036: ...EC Declarations of Conformity Appendix A 52 ...
Page 1037: ...Appendix EC Declarations of Conformity FR A800 A 53 ...
Page 1038: ...EC Declarations of Conformity Appendix A 54 ...
Page 1039: ...Appendix EC Declarations of Conformity FR A800 A 55 ...
Page 1040: ...EC Declarations of Conformity Appendix A 56 ...
Page 1041: ......