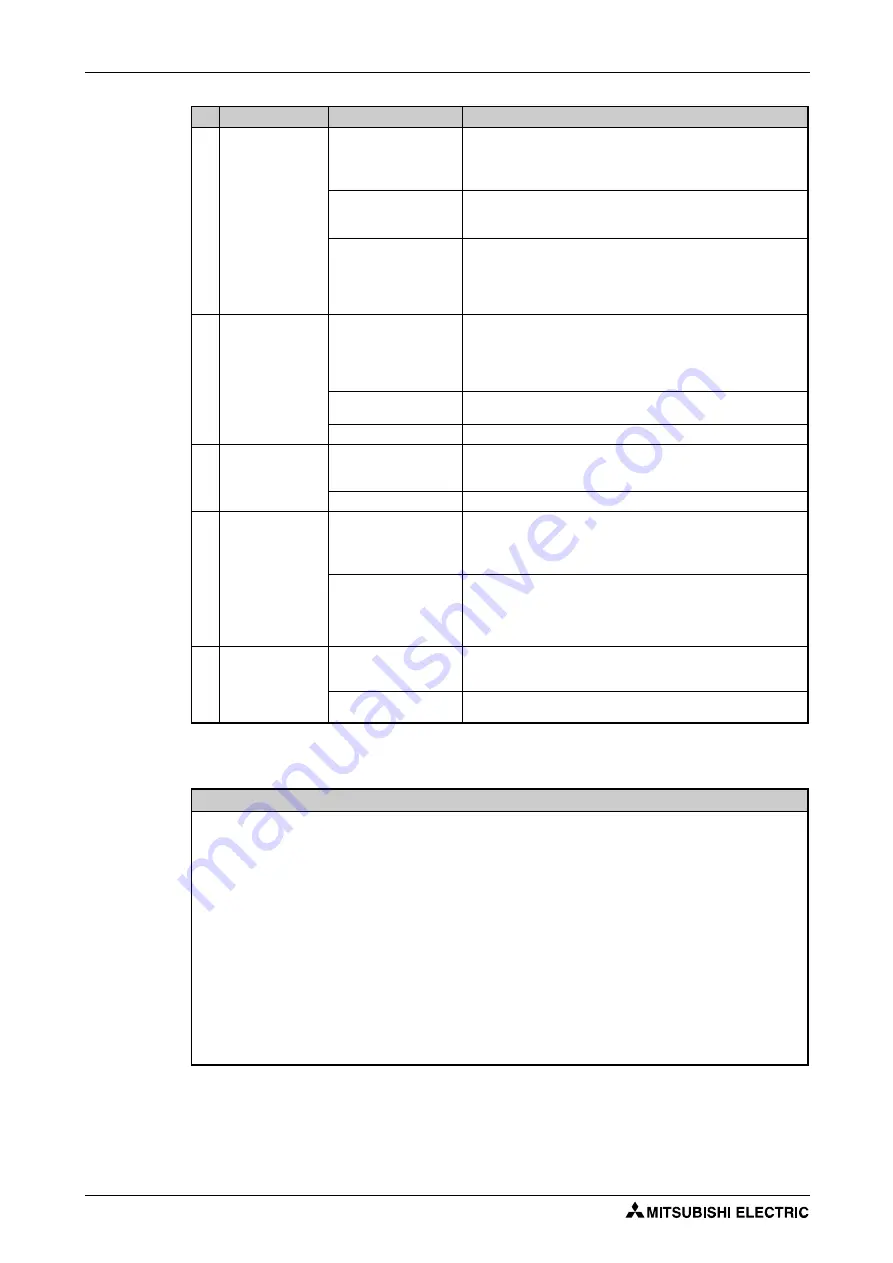
Speed control under Real sensorless vector control, vector control, PM sensorless vector control
Parameters
5 - 108
4
Motor speed
fluctuates.
Speed command varies.
앫
Check that the speed command sent from the controller is
correct. (Take EMC measures.)
앫
Set Pr. 72 "PWM frequency selection" lower.
앫
Set Pr. 822 "Speed setting filter 1" higher (page 5-399).
Torque shortage.
앫
Raise the torque limit.
(Refer to the torque limit for speed control on page 5-84.)
앫
Perform speed feed forward control.
Speed control gain is not
suitable for the machine.
(Resonance occurs.)
앫
Perform easy gain tuning.
앫
Adjust Pr. 820 "Speed control P gain 1" and Pr. 821 "Speed
control integral time 1".
앫
Perform speed feed forward control or model adaptive speed
control.
5
Hunting (vibration
or acoustic noise)
occurs in the motor
or the machine.
Speed control gain is too
high.
앫
Perform easy gain tuning.
앫
Set Pr. 820 "Speed control P gain 1" lower and Pr. 821 "Speed
control integral time 1" higher.
앫
Perform speed feed forward control or model adaptive speed
control.
Torque control gain is
too high.
앫
Set Pr. 824 "Torque control P gain 1 (current loop proportional
gain)" lower.
Motor wiring is incorrect.
앫
Check the wiring.
6
Acceleration/
deceleration time is
different from the
setting.
Torque shortage.
앫
Raise the torque limit.
(Refer to the torque limit for speed control on page 5-84.)
앫
Perform speed feed forward control.
Load inertia is too high.
앫
Set acceleration/deceleration time suitable for the load.
7
Machine movement
is unstable.
Speed control gain is not
suitable for the machine.
앫
Perform easy gain tuning.
앫
Adjust Pr. 820 and Pr. 821.
앫
Perform speed feed forward control or model adaptive speed
control.
Response is slow
because of the inverter's
acceleration/
deceleration time
setting.
앫
Set the optimum acceleration/deceleration time.
8
Rotation ripple
occurs during the
low-speed
operation.
High carrier frequency is
affecting the motor
rotation.
앫
Set Pr. 72 "PWM frequency selection" lower.
Speed control gain is too
low.
앫
Set Pr. 820 "Speed control P gain 1" higher.
Parameters referred to
Pr. 3
Base frequency
=>
Pr. 19
Base frequency voltage
=>
Pr. 72
PWM frequency selection
=>
Pr. 80
Motor capacity
=>
Pr. 81
Number of motor poles
=>
Pr. 125
Terminal 2 frequency setting gain frequency
=>
Pr. 126
Terminal 4 frequency setting gain frequency
=>
Pr. 359
Encoder rotation direction
=>
Pr. 369
Number of encoder pulses
=>
Pr. 822
Speed setting filter 1
=>
Pr. 824
Torque control P gain 1 (current loop proportional gain)
=>
Pr. 851
Control terminal option-Number of encoder pulses
=>
Pr. 852
Control terminal option-Encoder rotation direction
=>
No. Condition
Cause
Countermeasure
Tab. 5-39:
Troubleshooting (2)
Summary of Contents for FR-A800
Page 2: ......
Page 4: ......
Page 22: ...Contents XVIII ...
Page 30: ...Related manuals Introduction 1 8 ...
Page 122: ...Connection of stand alone option units Installation and wiring 2 92 ...
Page 180: ...Basic operation procedure JOG operation Basic operation 4 32 ...
Page 934: ...Check first when you have a trouble Protective functions 6 46 ...
Page 1031: ...Appendix EC Declarations of Conformity FR A800 A 47 ...
Page 1032: ...EC Declarations of Conformity Appendix A 48 ...
Page 1033: ...Appendix EC Declarations of Conformity FR A800 A 49 ...
Page 1034: ...EC Declarations of Conformity Appendix A 50 ...
Page 1035: ...Appendix EC Declarations of Conformity FR A800 A 51 A 5 2 EMC Directive ...
Page 1036: ...EC Declarations of Conformity Appendix A 52 ...
Page 1037: ...Appendix EC Declarations of Conformity FR A800 A 53 ...
Page 1038: ...EC Declarations of Conformity Appendix A 54 ...
Page 1039: ...Appendix EC Declarations of Conformity FR A800 A 55 ...
Page 1040: ...EC Declarations of Conformity Appendix A 56 ...
Page 1041: ......