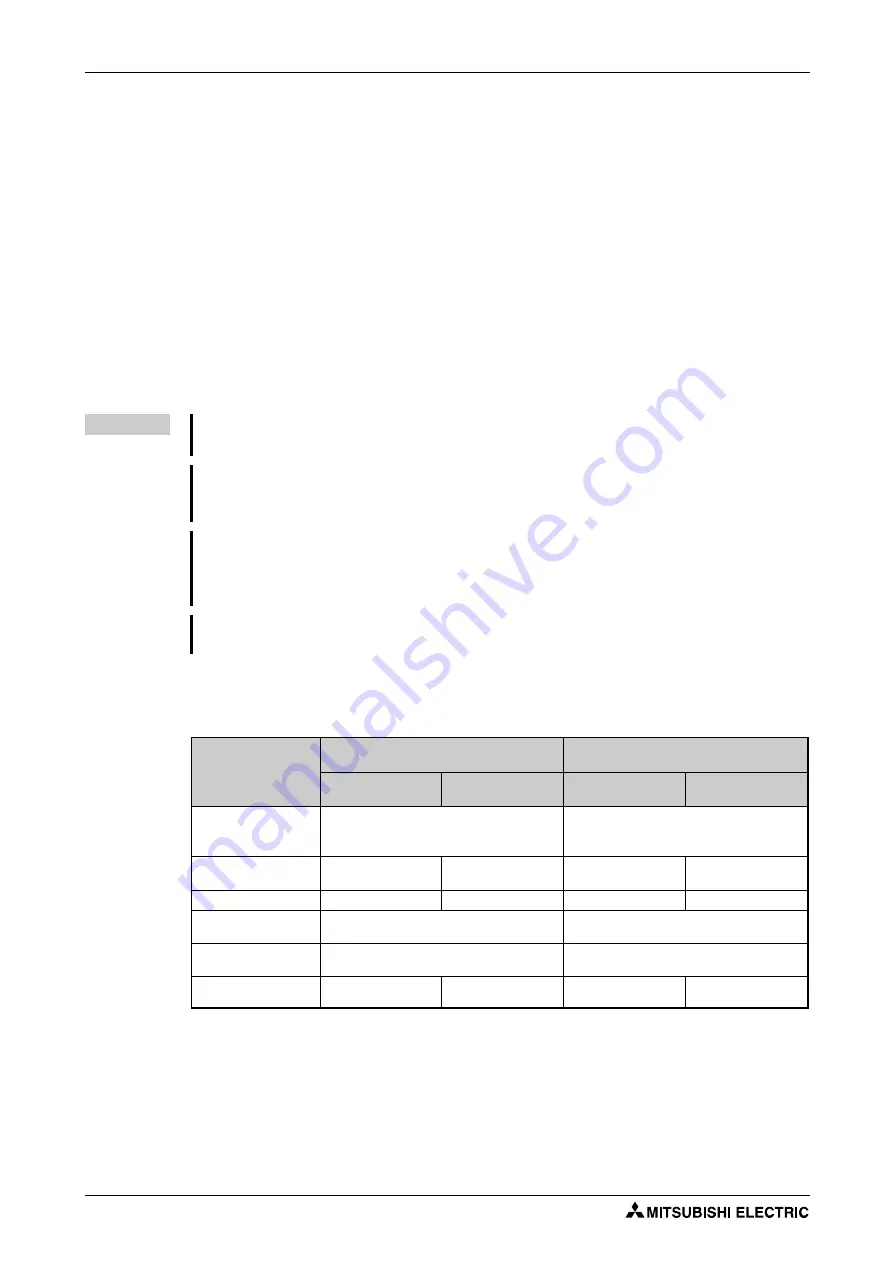
(A) Application parameters
Parameters
5 - 492
Setting the stop-on-contact control
●
Make sure that the inverter is in External or Network operation mode. (Refer to page 5-263.)
●
Select either Real sensorless vector control (speed control) or Advanced magnetic flux vector
control.
●
Set "1, 3, 11 or 13" in Pr. 270 "Stop-on contact/load torque high-speed frequency control selection".
●
Set the output frequency for stop-on-contact control in Pr. 6 "Multi-speed setting (low speed)".
Set the frequency as low as possible (about 2 Hz). If a frequency higher than 30 Hz is set, it operates
with 30 Hz.
●
When both the RT and RL signals are switched ON, the inverter enters the stop-on-contact control,
and operation is performed at the frequency set in Pr. 6 independently of the preceding speed.
●
Setting Pr. 270 = "11 or 13" disables stall prevention stop (E.OLT) during stop-on-contact control
(with both RL and RT signals ON).
Function switching of stop-on-contact control selection
When RL and RT are ON, Pr. 49 "Second stall prevention operation frequency" is invalid.
NOTES
By increasing the Pr. 275 setting, the low-speed (stop-on-contact) torque increases, but overcur-
rent fault (E.OC
첸
) may occur or the machine may oscillate in stop-on-contact status.
The stop-on-contact function is different from the servo-lock function, and if used to stop or hold a
load for an extended period, this function can cause the motor to overheat.
After a stop, immediately switch to a mechanical brake to hold the load.
Under the following operating conditions, the stop-on-contact function is invalid:
PU operation (Pr. 79), JOG operation (JOG signal), PU + External operation (Pr. 79), PID control
function operation (Pr. 128), Remote setting function operation (Pr. 59), Automatic acceleration/
deceleration (Pr. 292), Start time tuning, Orientation control function operation
When performing stop-on-contact control during encoder feedback control, encoder feedback
control is invalid due to a transition to the stop-on-contact control mode.
Main functions
Normal operation
(either RL or RT is OFF or both are OFF)
Stop-on-contact control
(both RL and RT are ON)
Real sensorless
vector control
Advanced magnetic
flux vector control
Real sensorless
vector control
Advanced magnetic
flux vector control
Output frequency
Multi-speed,
0 to 5 V, 0 to 10 V
4 to 20 mA, etc.
Pr. 6 setting
Stall prevention
operation level
—
Pr. 22 setting
—
The smaller value set in
either Pr. 22 or Pr. 48.
Torque limit level
Pr. 22 setting
—
Pr. 22 setting
—
Excitation current low-
speed scaling factor
—
The current is compensated by Pr. 275
(50 to 300%) setting from normal operation.
Carrier frequency
Pr. 72 setting
When output frequency is 3 Hz or lower, Pr. 276
setting (Pr. 72 when Pr. 276 = "9999")
Fast-response current
limit
—
Enabled
—
Disabled
Tab. 5-207:
Function switching of stop-on-contact control selection
Summary of Contents for FR-A800
Page 2: ......
Page 4: ......
Page 22: ...Contents XVIII ...
Page 30: ...Related manuals Introduction 1 8 ...
Page 122: ...Connection of stand alone option units Installation and wiring 2 92 ...
Page 180: ...Basic operation procedure JOG operation Basic operation 4 32 ...
Page 934: ...Check first when you have a trouble Protective functions 6 46 ...
Page 1031: ...Appendix EC Declarations of Conformity FR A800 A 47 ...
Page 1032: ...EC Declarations of Conformity Appendix A 48 ...
Page 1033: ...Appendix EC Declarations of Conformity FR A800 A 49 ...
Page 1034: ...EC Declarations of Conformity Appendix A 50 ...
Page 1035: ...Appendix EC Declarations of Conformity FR A800 A 51 A 5 2 EMC Directive ...
Page 1036: ...EC Declarations of Conformity Appendix A 52 ...
Page 1037: ...Appendix EC Declarations of Conformity FR A800 A 53 ...
Page 1038: ...EC Declarations of Conformity Appendix A 54 ...
Page 1039: ...Appendix EC Declarations of Conformity FR A800 A 55 ...
Page 1040: ...EC Declarations of Conformity Appendix A 56 ...
Page 1041: ......