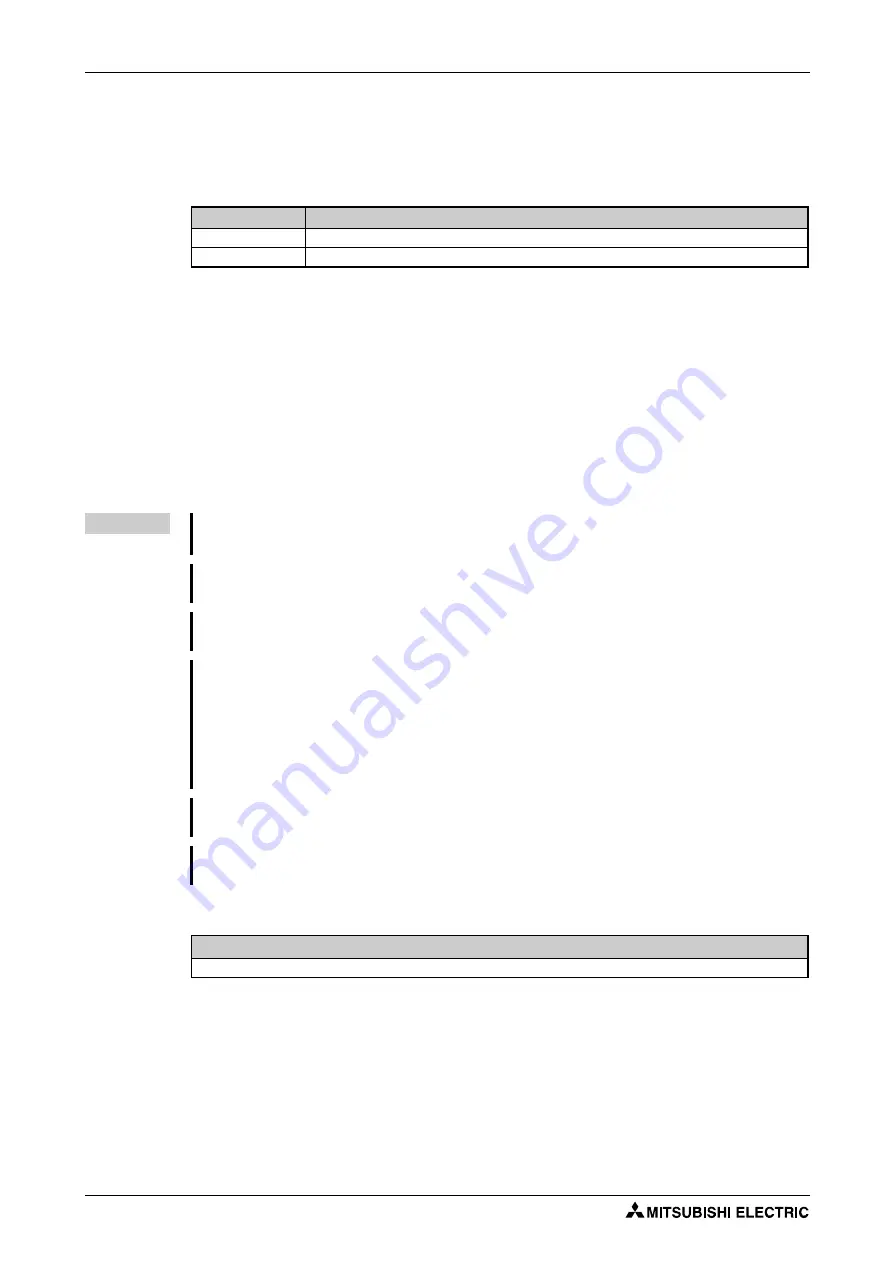
(G) Control parameters
Parameters
5 - 694
Feedback gain (Pr. 368)
●
Set Pr. 368 "Feedback gain" when the rotation is unstable or response is slow.
●
Response of the feedback will become slow when the acceleration/deceleration time is long. In
such case, increase the setting value of Pr. 368.
Overspeed detection (Pr. 285)
●
To prevent malfunction when the correct pulse signal cannot be detected from the encoder, when
[detection frequency] – [output frequency] > Pr. 285
at the time of encoder feedback control, protective function (E.MB1) will activate and the inverter
will shutoff output.
●
Overspeed detection is not performed when Pr. 285 = "9999".
Pr. 368 setting
Description
Pr. 368 > 1
Response will become faster but it may cause overcurrent or become unstable.
1 > Pr. 368
Response will become slower but it will become more stable.
Tab. 5-315:
Setting of parameter 368
NOTES
Couple the encoder on the same axis as the motor axis without any mechanical clatter, with speed
ratio of 1:1.
Encoder feedback control is not performed during the acceleration and deceleration to prevent
the unstable phenomenon such as hunting.
Encoder feedback control is performed after the output frequency has reached [set frequency] ±
[speed feedback range] once.
When following status occurs at the time of encoder feedback control operation, inverter will not
stop with an alarm, and operate with output frequency of [set frequency] ± [speed feedback
range], and will not follow the speed of the motor.
●
When the pulse signal from the encoder is lost due to a break, etc.
●
When correct pulse signal cannot be detected due to induction noise, etc.
●
When the motor is forcefully accelerated (regenerative rotation) or decelerated (motor lock)
due to large external force
Use the Inverter running (RUN) signal when releasing the brake from the motor with a brake. (The
brake may not be released when the Output frequency detection (FU) signal is used.)
Do not turn OFF the external power supply for the encoder at the time of encoder feedback con-
trol. Correct encoder feedback control will not be possible.
Parameters referred to
Pr. 81
Number of motor poles
=>
Summary of Contents for FR-A800
Page 2: ......
Page 4: ......
Page 22: ...Contents XVIII ...
Page 30: ...Related manuals Introduction 1 8 ...
Page 122: ...Connection of stand alone option units Installation and wiring 2 92 ...
Page 180: ...Basic operation procedure JOG operation Basic operation 4 32 ...
Page 934: ...Check first when you have a trouble Protective functions 6 46 ...
Page 1031: ...Appendix EC Declarations of Conformity FR A800 A 47 ...
Page 1032: ...EC Declarations of Conformity Appendix A 48 ...
Page 1033: ...Appendix EC Declarations of Conformity FR A800 A 49 ...
Page 1034: ...EC Declarations of Conformity Appendix A 50 ...
Page 1035: ...Appendix EC Declarations of Conformity FR A800 A 51 A 5 2 EMC Directive ...
Page 1036: ...EC Declarations of Conformity Appendix A 52 ...
Page 1037: ...Appendix EC Declarations of Conformity FR A800 A 53 ...
Page 1038: ...EC Declarations of Conformity Appendix A 54 ...
Page 1039: ...Appendix EC Declarations of Conformity FR A800 A 55 ...
Page 1040: ...EC Declarations of Conformity Appendix A 56 ...
Page 1041: ......