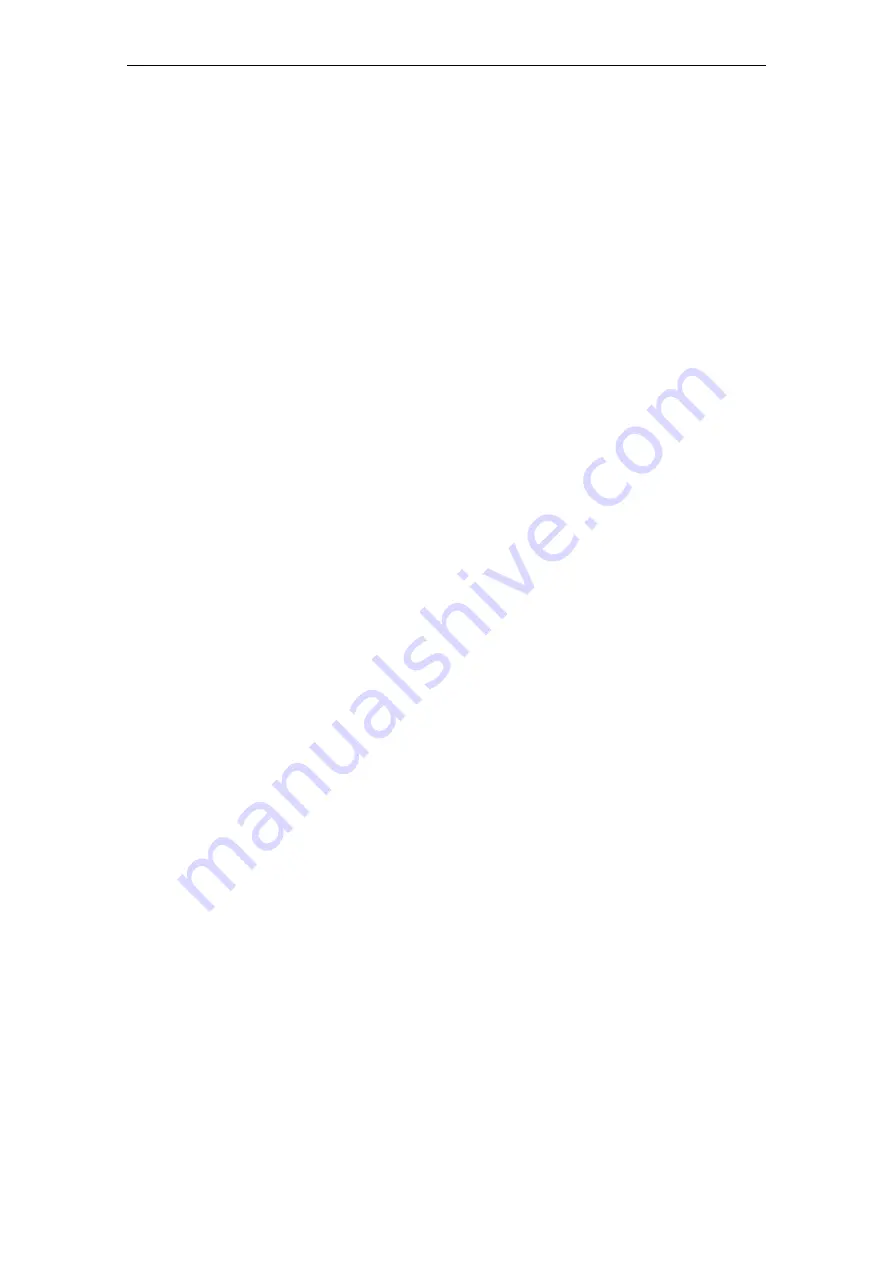
Faults and Alarms
List of faults and alarms
3-1596
© Siemens AG 2007 All Rights Reserved
SINAMICS S List Manual (LH1), 07/2007
125: Cable resistance greater than the total resistance.
126: Series inductance greater than the total leakage inductance.
127: Identified leakage inductance negative.
128: Identified stator resistance negative.
129: Identified rotor resistance negative.
130: Drive data set changeover during the motor data identification routine.
140: The setpoint channel inhibits both directions of rotation.
160: Accelerating when determining kT, moment of inertia or reluctance torque too short or the accelerating time is
too long.
173: Internal problem.
180: Identification speed (maximum speed, rated speed, 0.9 * p0348) less than p1755.
190: Speed setpoint not equal to zero.
191: An actual speed of zero is not reached.
192: Speed setpoint not reached.
193: Inadmissible motion of the motor when identifying the voltage emulation error.
194: Supplementary torque (r1515) not equal to zero.
195: Closed-loop torque control active.
200, 201: Not possible to identify the voltage emulation error characteristic of the drive converter (p1952, p1953).
Remedy:
Re fault value = 0:
Check whether motor is correctly connected. Observe config. (star-delta).
Re fault value = 1 ... 40:
- check whether motor data have been correctly entered into p0300, p0304 - p0311.
- is there an appropriate relationship between the motor power rating and that of the Motor Module? The ratio of the
Motor Module to the rated motor current should not be less than 0.5 and not be greater than 4.
- check motor config. (star-delta).
Re fault value = 2:
For parallel circuits: Check the motor winding system in p7003.
If, for power units connected in parallel, a motor is specified with a single-winding system (p7003 = 0), although a
multi-winding system is being used, then a large proportion of the stator resistance is interpreted as feeder cable
resistance and entered in p0352.
Re fault value = 4, 7:
Check whether inductances are correctly entered in p0233 and p0353.
Check whether motor was correctly connected (star/delta).
Re fault value = 50:
Reduce current controller sampling rate.
Re fault value = 101:
Increase current limit (p0640) or torque limit (p1520, p1521).
Check current controller gain (p1715).
Reduce current controller sampling time (p0115).
It may be impossible to completely identify the L characteristic, as required current amplitude is too high.
Suppress meas. (p1909, p1959).
Re fault value = 102, 104:
Reduce current limit (p0640).
Check current controller P gain.
Suppress meas. (p1909, p1959).
Re fault value = 103:
Increase external moment of inertia (if possible).
Reduce current controller sampling time (p0115).
Suppress meas. (p1909, p1959).
Re fault value 110:
Before rotating measurement, traverse motor over zero mark.
Re fault value 111:
It is possible that encoder does not have zero mark. Correct setting in p0404.Bit15.
Encoder pulse number was incorrectly entered. Correct setting in p408.
If zero mark signal is defective, replace encoder.
Re fault value 112:
Upgrade encoder software.
Re fault value = 113:
Check the limits (p0640, p1520, p1521, p1530, p1531), correct the zero values.
Re fault value 120:
Check current controller P gain (p1715) and if required, reduce.
Increase pulse frequency (p1800).