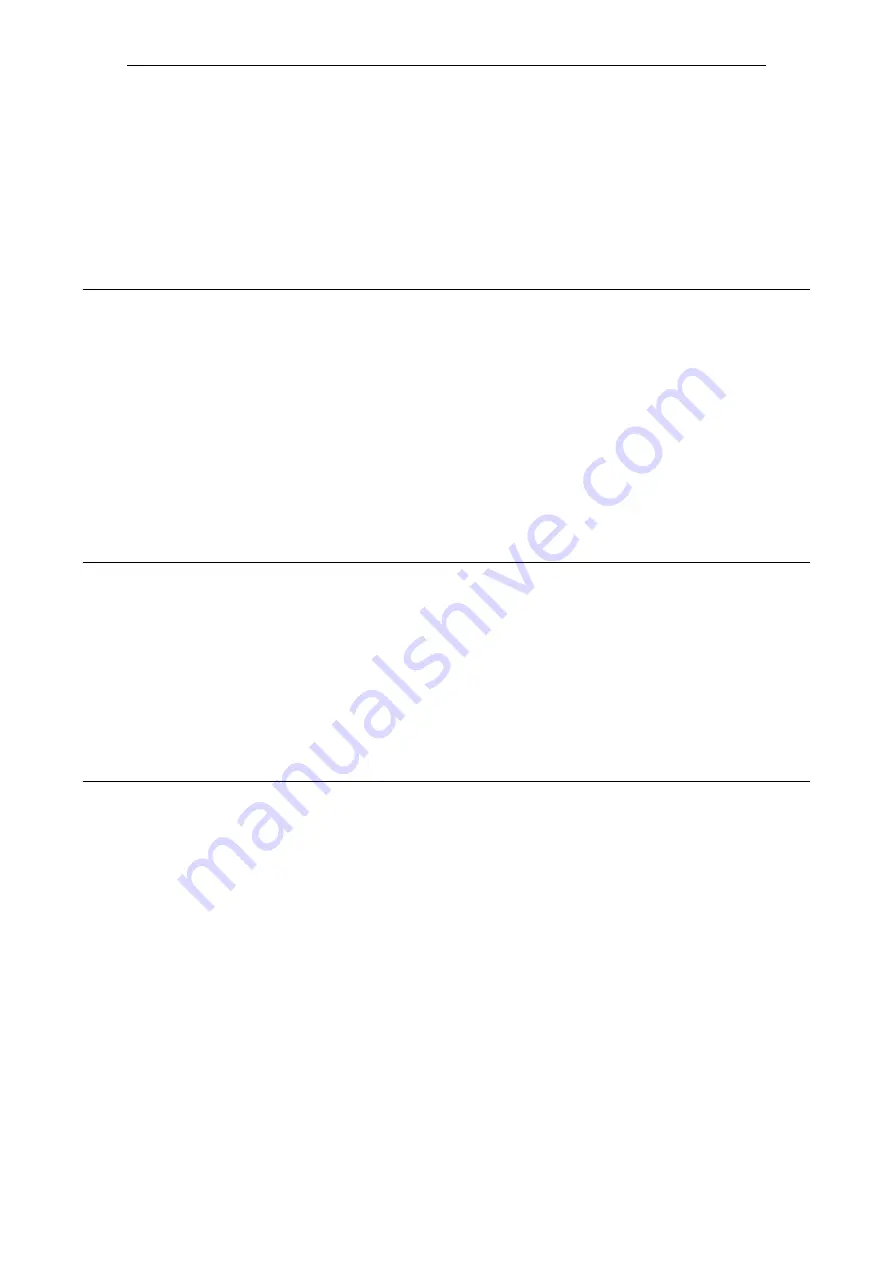
Faults and Alarms
List of faults and alarms
3-1562
© Siemens AG 2007 All Rights Reserved
SINAMICS S List Manual (LH1), 07/2007
2: For a linear axis, the position tracking was activated for the load and measuring gearbox.
3: Position tracking cannot be activated because there is more than one data set (p0180).
4: A linear encoder is being used.
See also: p0404 (Encoder configuration effective), p0411 (Measuring gearbox, configuration)
Remedy:
- use an absolute encoder.
- if necessary, de-select the position tracking (p0411 for the measuring gearbox, p2720 for the load gearbox).
- use a Control Unit with sufficient NVRAM.
Reaction upon A:
NONE
Acknowl. upon A:
NONE
F07556
Measuring gearbox: Position tracking, maximum actual value exceeded
Drive object:
SERVO, VECTOR
Reaction:
NONE
Acknowledge:
IMMEDIATELY
Cause:
When the position tracking of the measuring gearbox is configured, the drive/encoder identifies a maximum possible
absolute position actual value (r0483) that cannot be represented within 32 bits.
Maximum value: p0408 * p0412 * 2^p0419
Fault value (r0949, interpret decimal):
Low word low byte: Encoder data set number
Low word high byte: Component number
See also: p0408 (Rotary encoder pulse No.), p0412 (Measuring gearbox, rotary absolute gearbox, revolutions, vir-
tual), p0419 (Fine resolution absolute value Gx_XIST2 (in bits))
Remedy:
- reduce the fine resolution (p0419).
- reduce the multiturn resolution (p0412).
See also: p0412 (Measuring gearbox, rotary absolute gearbox, revolutions, virtual), p0419 (Fine resolution absolute
value Gx_XIST2 (in bits))
A07557 (F)
Encoder 1: Reference point coordinate not in the permissible range
Drive object:
SERVO, VECTOR
Reaction:
NONE
Acknowledge:
NONE
Cause:
The reference point coordinate received when adjusting the encoder via connector input CI:p2599 lies outside the
half of the encoder range and cannot be set as actual axis position.
Fault value (r0949, interpret decimal):
Limit value (absolute value) for the reference point coordinate.
Remedy:
Set the reference point coordinate less than the limit value specified in the fault value.
See also: p2598 (EPOS reference point coordinate, signal source)
Reaction upon F:
OFF1 (OFF2, OFF3)
Acknowl. upon F:
IMMEDIATELY
A07558 (F)
Encoder 2: Reference point coordinate not in the permissible range
Drive object:
SERVO, VECTOR
Reaction:
NONE
Acknowledge:
NONE
Cause:
The reference point coordinate received when adjusting the encoder via connector input CI:p2599 lies outside the
half of the encoder range and cannot be set as actual axis position.
Fault value (r0949, interpret decimal):
Limit value (absolute value) for the reference point coordinate.
Remedy:
Set the reference point coordinate less than the limit value specified in the fault value.
See also: p2598 (EPOS reference point coordinate, signal source)
Reaction upon F:
OFF1 (OFF2, OFF3)
Acknowl. upon F:
IMMEDIATELY