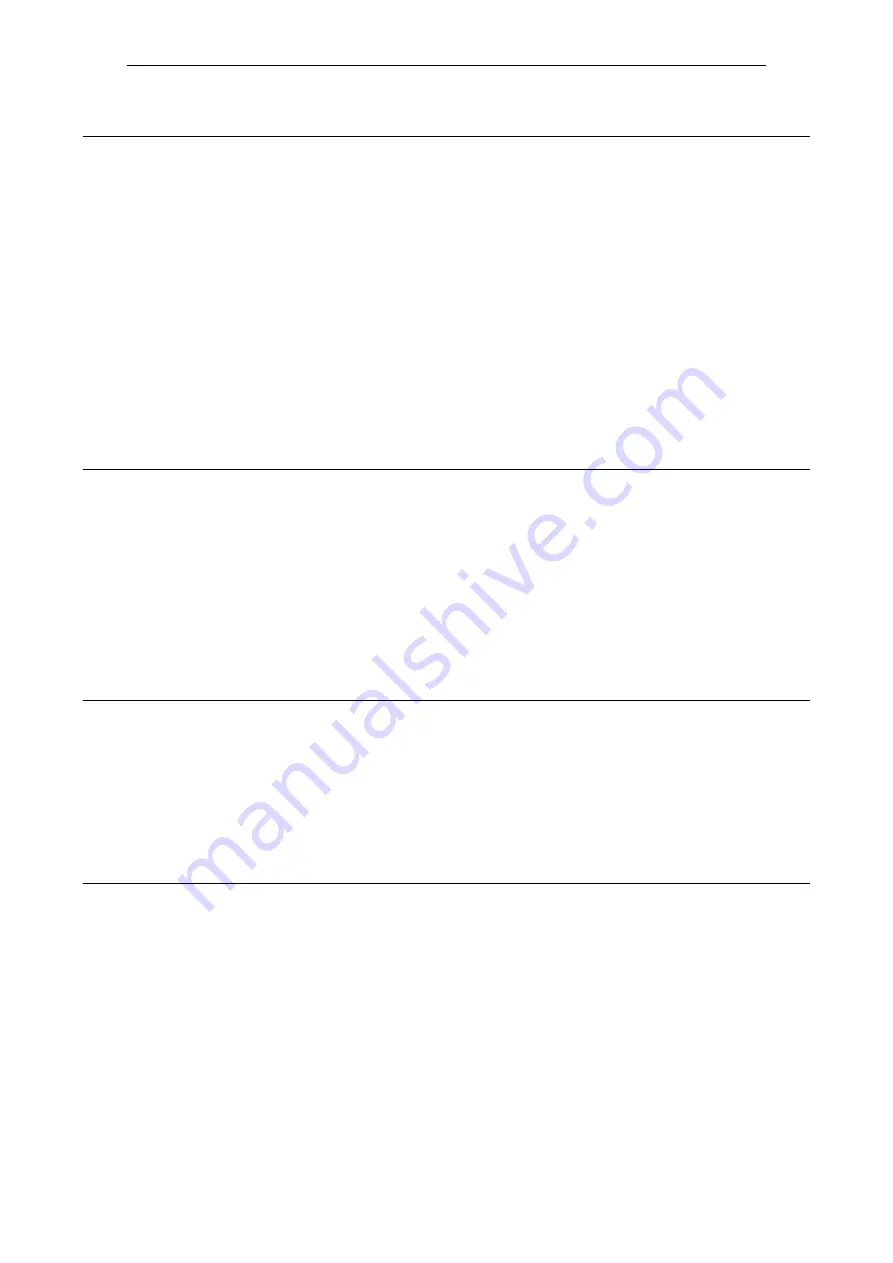
Faults and Alarms
List of faults and alarms
3-1542
© Siemens AG 2007 All Rights Reserved
SINAMICS S List Manual (LH1), 07/2007
F07432
Drive: Synchronous motor without overvoltage protection
Drive object:
SERVO
Reaction:
OFF2 (OFF1)
Acknowledge:
IMMEDIATELY
Cause:
Under voltage conditions, a synchronous motor can generate an overvoltage condition that can destroy the drive sys-
tem.
Fault value (r0949, interpret hexadecimal):
Associated Drive Data Set (DDS).
Remedy:
Overvoltage protection can be implemented in the following ways:
- limit the maximum speed (p1082) without any additional protection.
The maximum speed without protection is calculated as follows:
Rotary motors: p1082 [rpm] <= 11.695 * p0297/p0316 [Nm/A]
Linear motors: p1082 [m/min] <= 73.484 * p0297/p0316 [N/A]
- use a voltage protection module (VPM) in conjunction with the function "Safe Torque Off" (p9601, p9801).
When a fault condition exists, the VPM short-circuits the motors. During the short-circuit, the pulses must be can-
celed - this means that the terminals for the function "Safe Torque Off" must be connected to the VPM.
When using a VPM, p0643 must be set to 1.
- activating the internal voltage protection (IVP) with p1231 = 3.
See also: p0643 (Overvoltage protection for synchronous motors), p1231 (Armature short-circuit / DC brake config-
uration)
F07433
Drive: Closed-loop control with encoder is not possible as the encoder has not been
unparked
Drive object:
SERVO
Reaction:
NONE (OFF1, OFF2, OFF3)
Acknowledge:
IMMEDIATELY
Cause:
The changeover to closed-loop control with encoder is not possible as the encoder has not been unparked.
Remedy:
- check whether the encoder firmware supports the "parking" function (r0481.6 = 1).
- upgrade the firmware.
Note:
For long-stator motors (p3870.0 = 1), the following applies:
The encoder must have completed the unparking procedure (r3875.0 = 1) before a changeover can be made to
closed-loop control with encoder. The encoder is unparked with a 0/1 edge at BI: p3876 and remains unparked until
a 0 signal is again present.
F07434
Drive: It is not possible to change the direction using p1821 with the pulses enabled
Drive object:
SERVO, VECTOR
Reaction:
OFF2
Acknowledge:
IMMEDIATELY
Cause:
A drive data set was selected - with the pulses enabled - that has a different parameterized direction (p1821). It is
only possible to change the motor direction using p1821 when the pulses are inhibited.
Remedy:
- change over the drive data set with the pulses inhibited.
- ensure that the changeover to a drive data set does not result in the motor direction of rotation being reversed (i.e.
for these drive data sets, the same value must be in p1821).
See also: p1821 (Direction reversal rotating field)
F07435 (N)
Drive: Setting the ramp-function generator for sensorless vector control
Drive object:
SERVO, VECTOR
Reaction:
OFF2 (IASC / DCBRAKE, NONE, OFF1, OFF3)
Acknowledge:
IMMEDIATELY
Cause:
During operation with sensorless vector control (r1407.1) the ramp-function generator was stopped (p1141) or
bypassed (p1122). An internal setting command of the ramp-function generator output caused the set setpoint speed
to be frozen or was not able to be realized.