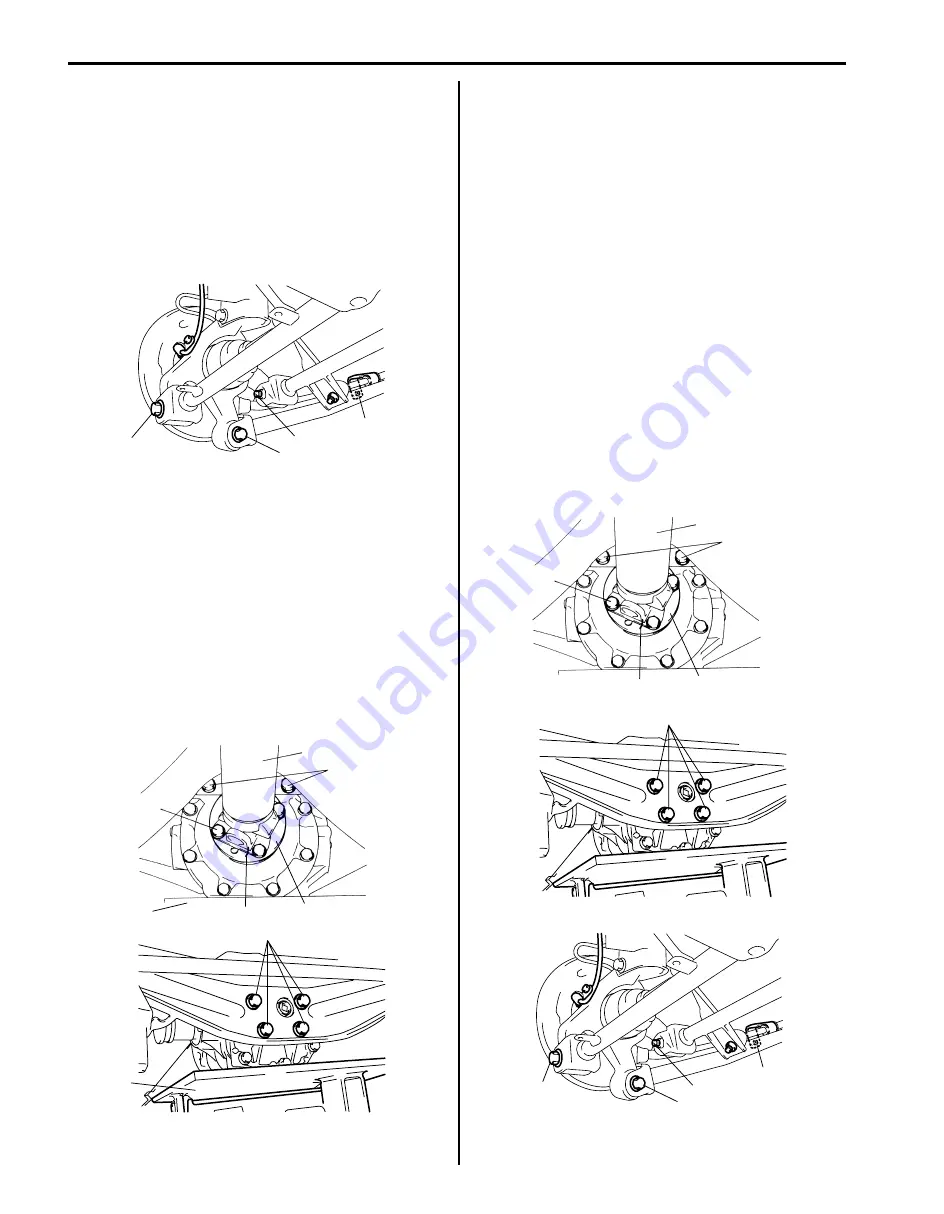
3B-5 Differential:
Rear Differential Assembly Dismounting and
Remounting
S3RH0A3206004
Dismounting
1) Hoist vehicle and remove wheels.
2) Drain oil from rear differential. Refer to “Rear
3) Remove parking brake wire mounting bolt (1), rear
control rod outer bolts (2) and rear trailing rod rear
bolt (3).
4) Remove rear drive shafts referring to “Rear Drive
Shaft Removal and Installation in Section 3A”.
5) Place jack (4) so that differential assembly will not
tilt.
6) Apply match marks (6) to companion flange (7) and
propeller shaft (3).
7) Remove 4 propeller shaft flange bolts (1) from rear
differential, and then pull out propeller shaft (3) from
rear differential.
8) Remove differential front mounting bracket bolts (2).
9) Remove differential rear mounting bracket bolts (5).
10) Lower jack (4) with rear differential assembly.
Remounting
Reverse dismounting procedure for remounting noting
the following points.
• Install propeller shaft (1) to companion flange (2)
aligning match marks (3).
• Tighten each bolt to specified torque.
Tightening torque
Differential front mounting bracket bolts (a): 50
N·m (5.0 kgf-m, 36.5 lb-ft)
Differential rear mounting bracket bolts (b): 50
N·m (5.0 kgf-m, 36.5 lb-ft)
Propeller shaft flange bolts (c): 23 N·m (2.3 kgf-
m, 17.0 lb-ft)
Rear control rod outer bolts (d): 90 N·m (9.0 kgf-
m, 65.0 lb-ft)
Rear trailing rod rear bolts (e): 90 N·m (9.0 kgf-m,
65.0 lb-ft)
Parking cable wire mounting bolts (f): 10 N·m (1.0
kgf-m, 7.5 lb-ft)
Rear drive shaft nuts: 175 N·m (17.5 kgf-m, 126.5
lb-ft)
Wheel nuts: 85 N·m (8.5 kgf-m, 61.5 lb-ft)
• Pour hypoid gear oil as specified referring to “Rear
1
2
3
2
I3RH01322014-01
5
4
3
2
1
4
6
7
I3RH0A320004-01
(b)
1
(a)
(c)
3
2
I3RH0A320005-01
(f)
(d)
(e)
(d)
I3RH01322017-01
Summary of Contents for Liana RH413
Page 2: ......
Page 4: ......
Page 6: ......
Page 336: ...1K 4 Exhaust System...
Page 456: ...3D 4 Propeller Shafts...
Page 553: ...Automatic Transmission Transaxle 5A 5 4WD I3RH0A510002 01 1 Transfer...
Page 1044: ...8B 119 Air Bag System...
Page 1049: ...Table of Contents 9 v Roof Molding Components 9M 1 Splash Guard If Equipped Components 9M 2...
Page 1278: ...9M 3 Exterior Trim...
Page 1300: ...Prepared by 1st Ed Nov 2003 2nd Ed Feb 2007...
Page 1301: ...19 mm 99500 54G10 01E 99500 54G10 01E SERVICE MANUAL VOLUME 1 OF 2 SERVICE MANUAL VOL 1 OF 2...
Page 1302: ...27 mm 99500 54G10 01E 99500 54G10 01E SERVICE MANUAL VOLUME 2 OF 2 SERVICE MANUAL VOL 2 OF 2...