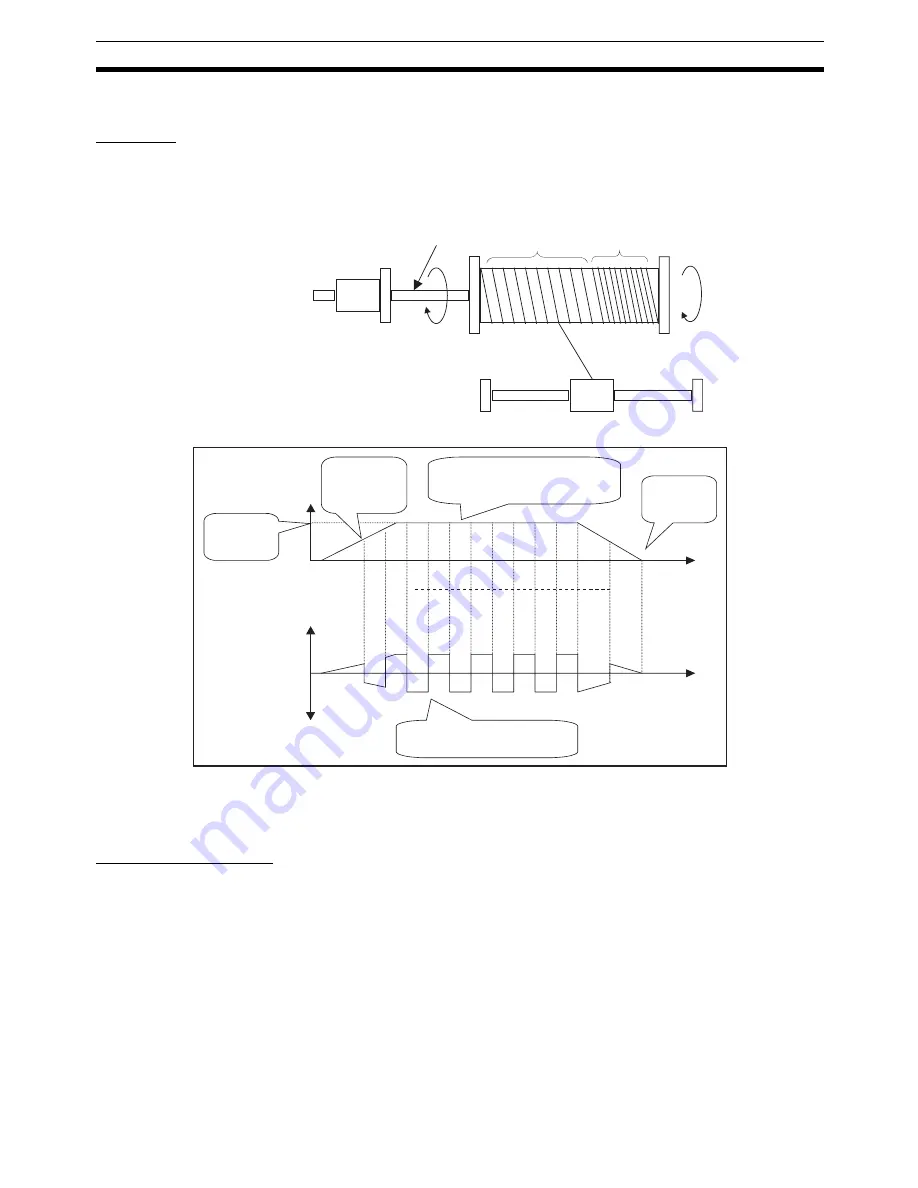
83
Overview of Version 1 Upgrades
Section 1-12
1-12-1-6
Linked Traverse Function
Overview
This function is used to link and execute G32 (TRAVERSE) programmed in
multiple blocks.
Linking G32 (TRAVERSE) commands with different parameters, such as pitch
(number of winds) and winding width, enables complex winding control opera-
tions, such as changing the pitch for a single workpiece.
Linked G32 commands are executed in Stop Mode using the speed designa-
tion in the first block with G32. For the rotating axis (X/Y) designations, the
number of windings (rotations) per layer or the pitch can be specified.
Application Example
X axis, Unit: degree; Y axis, Unit: mm
N001 G63 A1990=111
Function enabled with pitch specification and
start specification
N002 G63 A1991=540
Start specification = 540 degrees (1.5 rota-
tions)
N003 G32 X
−
0.1234 Y1.234 F360 O180 L1Direction of rotation = Negative,
Direction of traverse axis = Posi-
tive
Pitch = 0.1234
Winding width = 1.234 mm
Speed = 360 degrees/s (1 rota-
tion/s)
End specification = 180 degrees
Winding (rotating) axis
Traverse axis
G32 pitch a
G32 pitch b
+1 +2
Rotating axis (X/Y)
Traverse axis (Y/U)
Speed
Speed
M/D designation
in first block is
valid.
Block +n
Time
Time
First block
Speed of F
designation in
first block is
valid.
Acceleration/
deceleration
specified in system
parameters
Add travel distance for G32 in multiple blocks.
(Each vertical dotted line is 1 block.)
Traverse axis will operate in sync with the
rotating axis according to Y/U designations,
the O designation, and the L designation.
Summary of Contents for CS1W-MC221 -
Page 1: ...Motion Control Units Cat No W359 E1 04 CS1W MC221 V1 421 V1 OPERATION MANUAL ...
Page 2: ...CS1W MC221 V1 421 V1 Motion Control Units Operation Manual Revised February 2008 ...
Page 3: ...iv ...
Page 5: ...vi ...
Page 11: ...xii ...
Page 15: ...xvi ...
Page 19: ...xx ...
Page 27: ...xxviii Conformance to EC Directives 6 ...
Page 133: ...106 Installation Section 2 2 2 2 4 Dimensions CS1W MC421 CS1W MC221 ...
Page 173: ...146 Connecting Peripheral Devices Section 2 7 ...
Page 227: ...200 Command Area Section 3 6 ...
Page 351: ...324 Interface Specifics Section 5 4 ...
Page 513: ...486 Absolute Encoder Interface Specifications Section 9 7 ...
Page 575: ...548 Error Log Section 12 6 ...
Page 589: ...562 Performance Appendix A ...
Page 655: ...628 Control Bit Flag Timing Charts Appendix E ...
Page 683: ...656 Origin Search Patterns Appendix F ...
Page 685: ...658 Encoder Divider Rate and Rotation Speed for OMRON Servo Drivers Appendix G ...