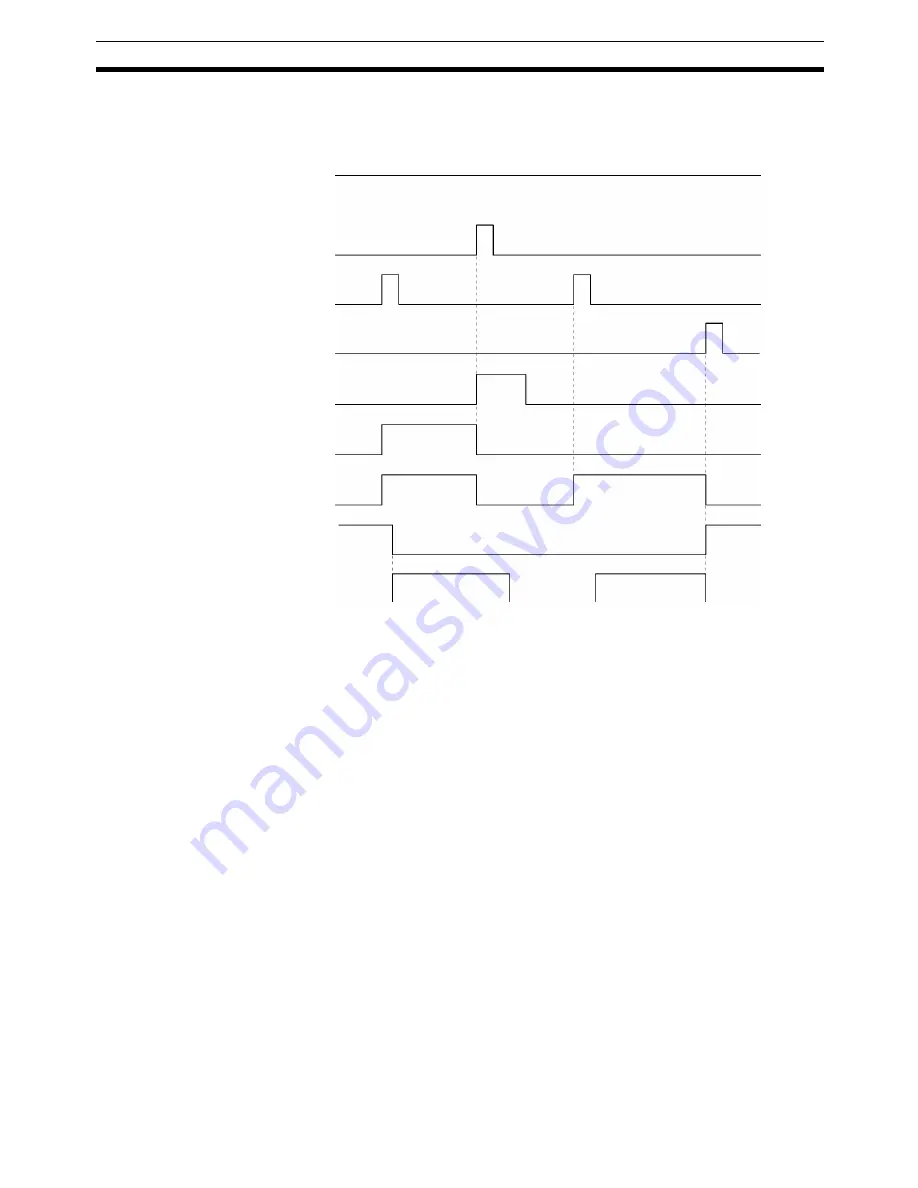
271
Interface Specifics
Section 5-4
Timing Chart
The following timing charts illustrates the operation of the above programming
example.
Note
1.
Programs can be continued even after the following operations. Before
continuing the program operation, be sure to confirm that existing condi-
tions will not cause any problem. If continuous program operation causes
a problem, do not continue the program; instead create the ladder program
so that the program will be executed from the beginning.
a) Program operation running under the Automatic Mode was stopped in-
tentionally or came to a stop by itself.
Examples:
The Cycle Start Bit was turned OFF.
An error occurred.
b) Manual commands were executed in Manual Mode.
Examples:
An origin search was executed.
Jogging was executed.
A servo lock was executed.
c)
The Cycle Start Bit was turned ON to continue operation after return-
ing to Automatic Mode.
For example, the following type of operation is possible:
The program can be temporarily suspended while moving to X10000 and
stopped at a position before the demand position, e.g., X500. The mode
can then be changed to Manual Mode and an origin search executed. After
the origin search has been completed, the mode can be changed back to
Automatic Mode to continue program operation. The program will continue
the move operation to X10000.
Automatic/Manual
Mode Bit
R1 (pause)
R2 (program start)
R3 (execution completed)
Program initialization condition
Pause
(n+3, 05)
Cycle Start Bit
(n+3, 02)
Program Execution Completed
Flag (n+15, 05)
Program Execution
Flag (n+15, 04)
High level
Summary of Contents for CS1W-MC221 -
Page 1: ...Motion Control Units Cat No W359 E1 04 CS1W MC221 V1 421 V1 OPERATION MANUAL ...
Page 2: ...CS1W MC221 V1 421 V1 Motion Control Units Operation Manual Revised February 2008 ...
Page 3: ...iv ...
Page 5: ...vi ...
Page 11: ...xii ...
Page 15: ...xvi ...
Page 19: ...xx ...
Page 27: ...xxviii Conformance to EC Directives 6 ...
Page 133: ...106 Installation Section 2 2 2 2 4 Dimensions CS1W MC421 CS1W MC221 ...
Page 173: ...146 Connecting Peripheral Devices Section 2 7 ...
Page 227: ...200 Command Area Section 3 6 ...
Page 351: ...324 Interface Specifics Section 5 4 ...
Page 513: ...486 Absolute Encoder Interface Specifications Section 9 7 ...
Page 575: ...548 Error Log Section 12 6 ...
Page 589: ...562 Performance Appendix A ...
Page 655: ...628 Control Bit Flag Timing Charts Appendix E ...
Page 683: ...656 Origin Search Patterns Appendix F ...
Page 685: ...658 Encoder Divider Rate and Rotation Speed for OMRON Servo Drivers Appendix G ...