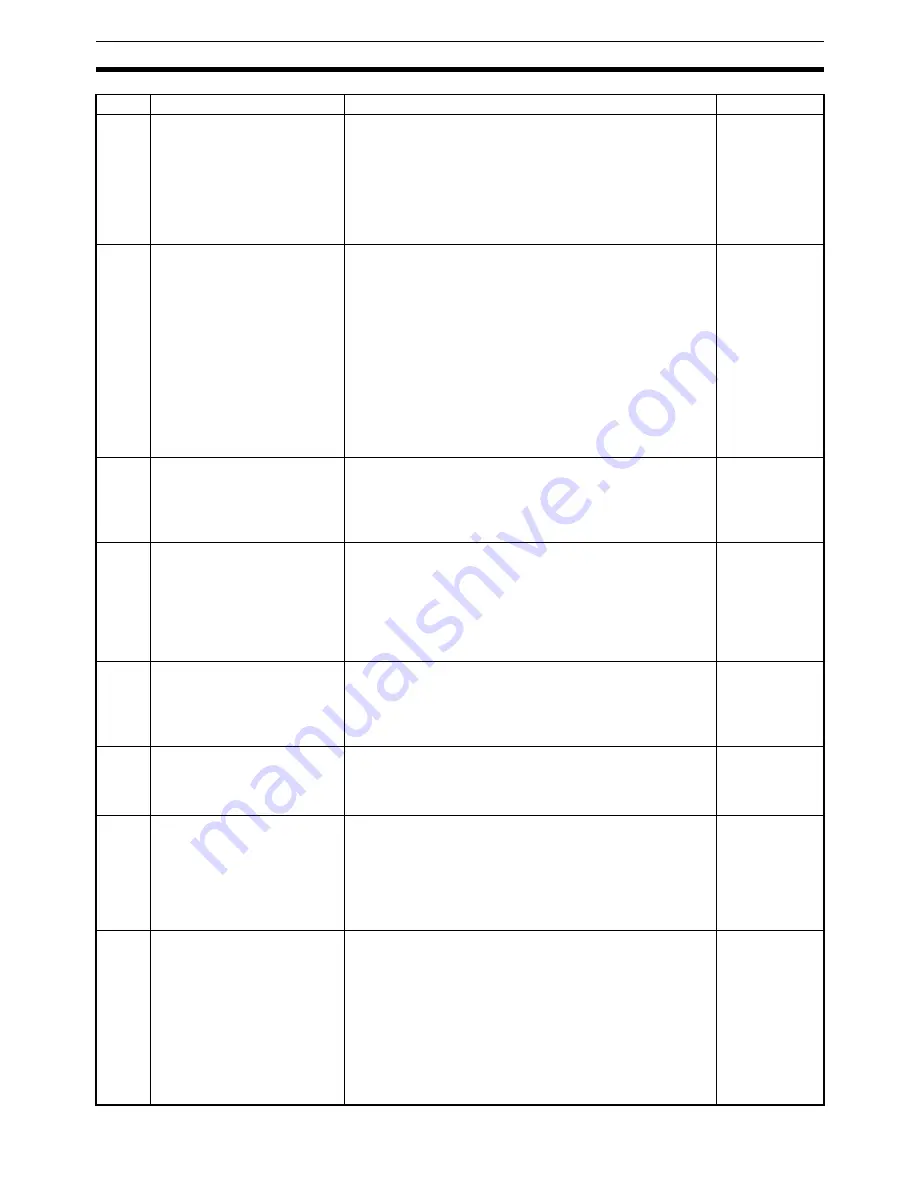
539
Task Error Codes
Section 12-4
0024
(0036)
Program number not set
(PROG No. NOT SET)
When the MC program was started from the ladder program,
the Cycle Start Bit was turned ON without turning ON the
Program Number Read Bit. Turn ON the Cycle Start Bit after
turning ON the Program Number Read Bit.
The Program Number Read Bit must be turned ON when the
Cycle Start Bit is turned ON after using the CX-Motion to add,
edit, or delete any MC programs in the task. In this case, the
program will be executed from the first block.
Deceleration
stop
0025
(0037)
Number out of range
(NUM RANGE OVER)
A numerical value exceeded the acceptable range during
execution of G04 (time value), G53 (offset value), G54
(preset value), G69 (parameter value), or G70 (number of
loops) command.
An overflow occurred when the offset value or preset value
was converted with the minimum setting unit from the system
parameters.
Correct the program or the position data. Check the setting
for the minimum setting unit parameter in the system
parameters when the error occurs in a present position
preset from the G53 or G54.
The travel amount was 0 for an axis for which a stopover was
specified when using a version-1 MC Unit.
Deceleration
stop
0026
(0038)
Negative interpolation rate
(INTER SP – DESIG)
A zero or negative value in a position data address or register
was specified for the interpolation feed rate for linear
interpolation, circular interpolation, or interrupt inching.
Correct the program or the position data so that a positive
value is used for the interpolation feed rate.
Deceleration
stop
0027
(0039)
Illegal intermediate code
(INTER CODE ERROR)
Somehow the program has been destroyed. Download the
program again and write it to the flash memory, and then turn
the power OFF and ON. The intermediate code error could
have been caused by any of the following:
The memory data might have been destroyed by noise.
The PLC (MC Unit) might have been turned OFF while
data was being written to the flash memory.
Deceleration
stop
0028
(0040)
Operating time overflow
(RUN TIME OVERRUN)
Attempted to execute a G00, G01, G02, or G03 positioning
command, but the movement to the specified target would
take too long at the specified feed rate.
Correct the program, position data, or parameters to increase
the feed rate or reduce the distance to be moved.
Deceleration
stop
0029
(0041)
Position counter overflow
(MOVE DIST OVER)
Can’t move to the target specified in a G01 command
because it is too far.
Correct the program or position data to reduce the distance
to be moved.
Deceleration
stop
002A
(0042)
Position counter overflow
during arc movement
(CIR ARC DIST OVER)
Can’t move the amount specified in a circular interpolation
command because it is too far. Either the distance between
the center and start/end point is too great, the arc length is
too great, or the distance between the start and end points is
too great.
Correct the program or data to reduce the distance to be
moved.
Deceleration
stop
002B
(0043)
Arc cannot be completed
(CIR ARC CONT ERR)
Attempted to continue circular interpolation, but couldn’t
because an axis error occurred during circular interpolation,
the circular interpolation was decelerated to a stop and then
another positioning operation such as jogging was
performed, or the circular interpolation was decelerated to a
stop and then an axis error occurred.
When this error occurs, circular interpolation cannot be
continued, so restart the program from the beginning.
Circular interpolation can be continued when the interpola-
tion is decelerated to a stop and no errors or other positioning
operations occur while the interpolation is stopped.
Deceleration
stop
Code
Error
Error Processing
Stop method
Summary of Contents for CS1W-MC221 -
Page 1: ...Motion Control Units Cat No W359 E1 04 CS1W MC221 V1 421 V1 OPERATION MANUAL ...
Page 2: ...CS1W MC221 V1 421 V1 Motion Control Units Operation Manual Revised February 2008 ...
Page 3: ...iv ...
Page 5: ...vi ...
Page 11: ...xii ...
Page 15: ...xvi ...
Page 19: ...xx ...
Page 27: ...xxviii Conformance to EC Directives 6 ...
Page 133: ...106 Installation Section 2 2 2 2 4 Dimensions CS1W MC421 CS1W MC221 ...
Page 173: ...146 Connecting Peripheral Devices Section 2 7 ...
Page 227: ...200 Command Area Section 3 6 ...
Page 351: ...324 Interface Specifics Section 5 4 ...
Page 513: ...486 Absolute Encoder Interface Specifications Section 9 7 ...
Page 575: ...548 Error Log Section 12 6 ...
Page 589: ...562 Performance Appendix A ...
Page 655: ...628 Control Bit Flag Timing Charts Appendix E ...
Page 683: ...656 Origin Search Patterns Appendix F ...
Page 685: ...658 Encoder Divider Rate and Rotation Speed for OMRON Servo Drivers Appendix G ...