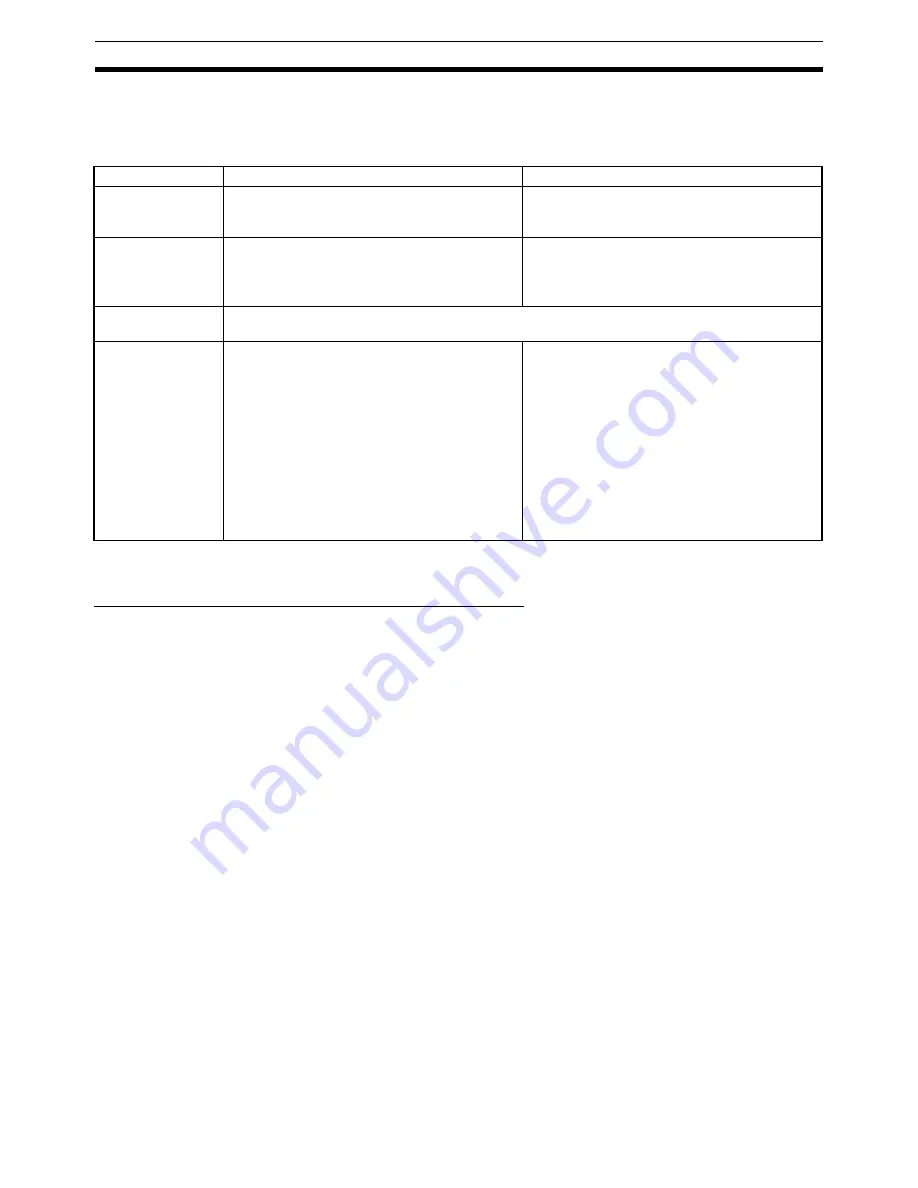
134
Failsafe Circuits
Section 2-4
2-4-1
Failsafe Principles
The MC Unit handles failsafe measures as described in the following table.
Applications examples are provided in the following sections.
2-4-2
Failures in the Command System
Stopping the Motor with an Error Counter Warning
Error Counter Warnings
The Error Counter Warning Flag will be turned ON to notify the CPU Unit if the
number of pulses in the error counter exceeds the value set as the Error
Counter Warning Value in the System Parameters. The Error Counter Warn-
ing Flag can be monitored in the ladder program to handle errors if they occur.
Use the following procedure to set the Error Counter Warning Value.
1,2,3...
1.
Move the system in trial operation and check the number of pulses that ac-
cumulate in the error counter.
2.
After confirming the maximum number of pulses in the error counter, set
the Error Counter Warning Value in the System Parameters to between
10% and 20% higher than the maximum number.
Refer to
Error Counter Function Selection Bit
in
5-4-1 System Controls
for
more information.
Item
Failure in the command system
Failure in the feedback system
Outline
Movements are not performed at the command
speed or in the desired direction.
Movement occurs for stop commands or
movement is not performed in the desired
direction.
Location of failure
Digital-to-analog circuits or analog power circuits
in the MC Unit.
Analog-to-digital circuits in Servo Drive, wiring of
command systems, etc.
Motor encoder, encoder cable, Servo Drive
encoder circuit, MC Unit encoder circuit.
Failsafe measures
Installing sensors in dangerous locations to stop the mechanical system by turning OFF the Servo
Drive main circuits.
Remarks
Machine movements can be determined from the
amount of movement in the encoder, which in
turn can be determined by the value of the error
counter. The following measures can thus be
taken.
Creating a system that will stop the motor for the
error counter warning function.
Creating a system that will stop the motor for the
error counter overflow function.
If the command from the MC Unit is within a
range determined to be, zones can be set and
used to sop the motor.
If the feedback system fails, it will not be possible
to determine the position of the mechanical
system, e.g., the amount of encoder movement
will be 0 even though the machine is moving.
Here, hardware measures, such as sensors to
stop movement, are required.
Summary of Contents for CS1W-MC221 -
Page 1: ...Motion Control Units Cat No W359 E1 04 CS1W MC221 V1 421 V1 OPERATION MANUAL ...
Page 2: ...CS1W MC221 V1 421 V1 Motion Control Units Operation Manual Revised February 2008 ...
Page 3: ...iv ...
Page 5: ...vi ...
Page 11: ...xii ...
Page 15: ...xvi ...
Page 19: ...xx ...
Page 27: ...xxviii Conformance to EC Directives 6 ...
Page 133: ...106 Installation Section 2 2 2 2 4 Dimensions CS1W MC421 CS1W MC221 ...
Page 173: ...146 Connecting Peripheral Devices Section 2 7 ...
Page 227: ...200 Command Area Section 3 6 ...
Page 351: ...324 Interface Specifics Section 5 4 ...
Page 513: ...486 Absolute Encoder Interface Specifications Section 9 7 ...
Page 575: ...548 Error Log Section 12 6 ...
Page 589: ...562 Performance Appendix A ...
Page 655: ...628 Control Bit Flag Timing Charts Appendix E ...
Page 683: ...656 Origin Search Patterns Appendix F ...
Page 685: ...658 Encoder Divider Rate and Rotation Speed for OMRON Servo Drivers Appendix G ...