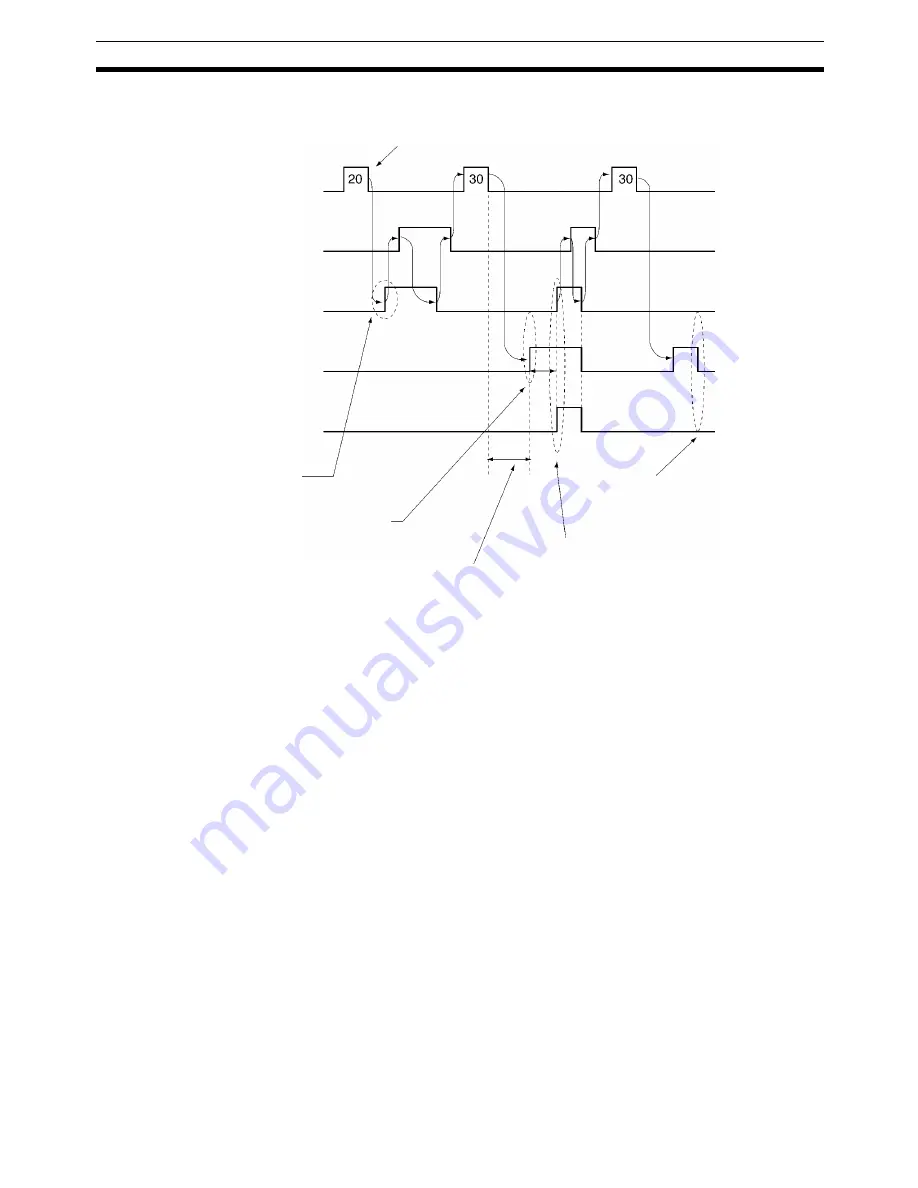
363
Present Position Preset
Section 6-17
Error Flag will turn ON. If that occurs, the data transferred up to that point will
be discarded.
Note
The MC Unit does not monitor the time from when it receives the automatic
loading command until the Autoloading Flag turns ON. There may be cases
where the power to the personal computer is turned OFF or a cable is discon-
nected, so monitor this time from the ladder program.
6-17 Present Position Preset
Overview
Mode:
Manual;
Method:
Command Area designation
The present position preset function is used to preset the preset position to
any given value. With previous MC Unit models, it was executed from the PLC
Interface Area, but with the MC221 and MC421 it is executed by an IOWR
instruction using the Command Area. It can only be used in Manual Mode,
and will be ignored if used in Automatic Mode.
After the present position has been preset, the reference origin is established
automatically, so there is no need to execute an origin search. It is also possi-
ble to set the present position as the origin by using the present position pre-
set function to set the present position to “0.”
!Caution
When present position preset is executed for an axis for which an absolute
encoder is used, only the present position stored in the MC Unit will be preset.
The present position stored in the absolute encoder will not be preset, and it
will be automatically updated with the next servo-lock.
Job number
Automatic loading command
(IOWR instruction)
Autoloading Flag
(n+10, 04; n+18, 04)
When automatic loading is completed
normally.
Autoloading Error Reset Bit
(n, 05)
Autoloading Error Flag
(n+10, 05; n+18, 05)
Autoloading Time Up Flag
(n+10, 15; n+18, 15)
10 s
Monitor the time from the ladder program. (See note.)
When an error is detected during
automatic loading.
The time is monitored from when CX-Motion receives
the job number and automatic loading is executed.
If communications are not restarted by the time the
Autoloading Time Up time set in the system parame-
ters (10 s in this case) has elapsed (e.g., because of
a cable disconnection, noise, etc.), the data trans-
ferred up to this point will be discarded.
Summary of Contents for CS1W-MC221 -
Page 1: ...Motion Control Units Cat No W359 E1 04 CS1W MC221 V1 421 V1 OPERATION MANUAL ...
Page 2: ...CS1W MC221 V1 421 V1 Motion Control Units Operation Manual Revised February 2008 ...
Page 3: ...iv ...
Page 5: ...vi ...
Page 11: ...xii ...
Page 15: ...xvi ...
Page 19: ...xx ...
Page 27: ...xxviii Conformance to EC Directives 6 ...
Page 133: ...106 Installation Section 2 2 2 2 4 Dimensions CS1W MC421 CS1W MC221 ...
Page 173: ...146 Connecting Peripheral Devices Section 2 7 ...
Page 227: ...200 Command Area Section 3 6 ...
Page 351: ...324 Interface Specifics Section 5 4 ...
Page 513: ...486 Absolute Encoder Interface Specifications Section 9 7 ...
Page 575: ...548 Error Log Section 12 6 ...
Page 589: ...562 Performance Appendix A ...
Page 655: ...628 Control Bit Flag Timing Charts Appendix E ...
Page 683: ...656 Origin Search Patterns Appendix F ...
Page 685: ...658 Encoder Divider Rate and Rotation Speed for OMRON Servo Drivers Appendix G ...