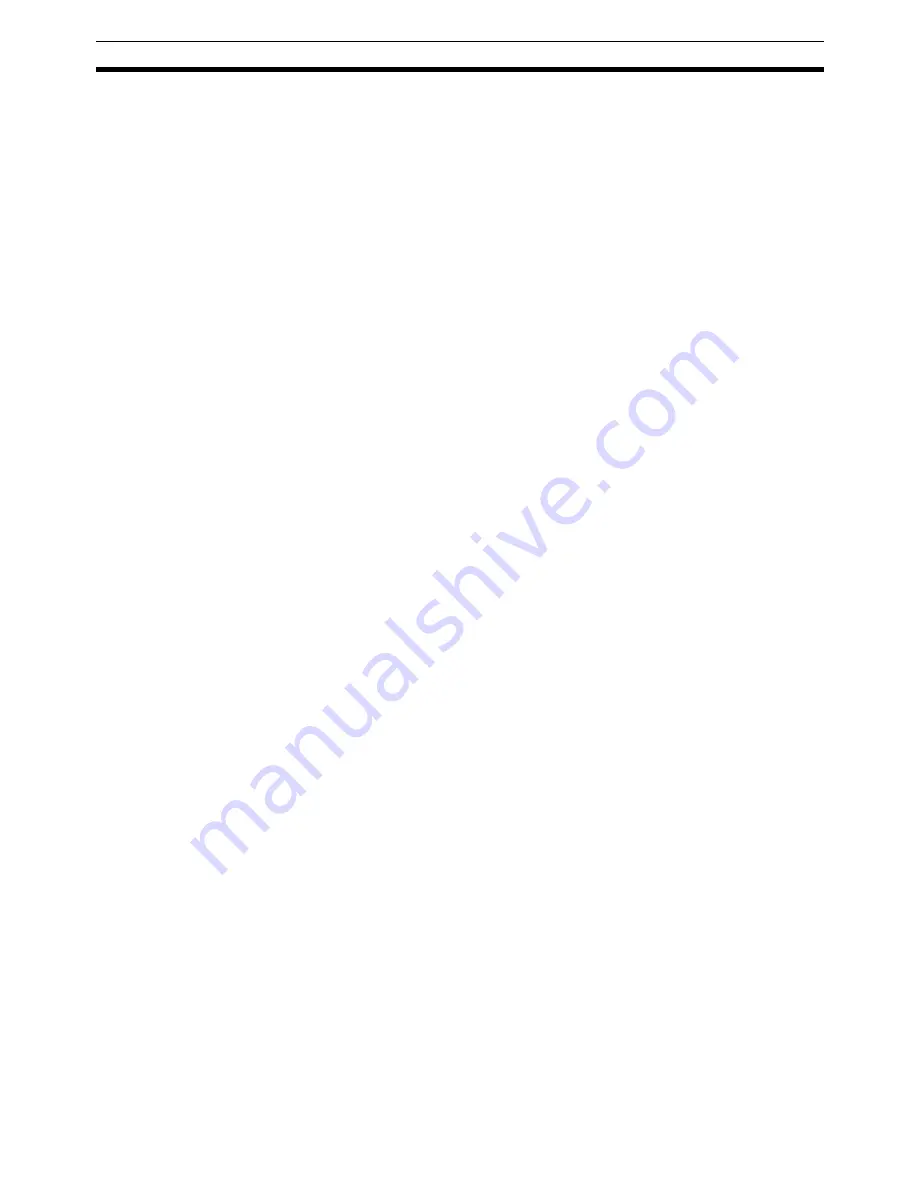
519
Considerations When Starting Up the MC Unit
Section 11-3
Maximum Number of
Motor Revolutions
Set the rated number of revolutions for the motor (generally the catalog value).
Note
1.
There is a difference between the acceleration/deceleration times set in
the MC Unit and the Servo Driver. The MC Unit acceleration/deceleration
time defines the time for accelerating and decelerating until the MC Unit’s
maximum feed rate or interpolation speed reference. The Servo Driver ac-
celeration/deceleration time, in contrast, sets the delay time for accelerat-
ing to the speed reference that is given. When the Servo Driver
acceleration/deceleration time is set, it lowers the gain for the system, so
do not make this setting when using a Servo Driver in combination with an
MC Unit.
2.
When an S-curve is set in the MC Unit and a software start is set in the
Servo Driver, it puts the MC outputs through a filter and the gain is ex-
tremely decreased. Set both the S-curve and software start may produce
faulty operation.
Transferring and Saving
Data
When using CX-Motion to transfer data to the MC Unit, select Save/Transfer
(Computer
→
MC). Parameters, position data, programs, and so on, are
transferred between a file (on a floppy or hard disk) and the MC Unit, so they
must be saved or the MC Unit will operate using the old data. After transfer-
ring the data, be sure to save it to flash memory before turning OFF the
power.
If the machine parameters or Unit parameters are changed and transferred, a
system setup error will occur. It can be cleared by turning OFF the power and
restarting the Unit. The error will appear to be cleared by just executing an
error reset, but internally the old system parameters will remain in effect. The
program cannot be correctly transferred while this condition persists, so when-
ever a system setup error occurs, be sure to turn OFF the power and use the
Restart Bit in the CPU Unit to restart the Unit. Then transfer the program after
the restart.
Backing Up Data to Flash
Memory
With the CS1W-MC421 and CS1W-MC221, memory is backed up to flash
memory following the transfer of system parameters and other data. The data
in flash memory is always reloaded when the MC Unit is started. If data is not
written to flash memory, it will be valid only until the power is turned OFF, so
be sure to save it to flash memory after transferring it if it is required.
11-3-2 Considerations When Starting Up or Making Adjustments
Adjusting the Wiring
Check Parameters
An error may occur if the wiring check parameters are left at their default set-
tings. These settings are made assuming a suitable load, but the load in the
actual system may be different and a wiring error may be incorrectly detected.
If a wiring error does occur, refer to
2-5 Wiring Check Troubleshooting
and
adjust the wiring check parameters.
11-3-3 Changing the Teaching Box Mode for Trial Operation
When the Teaching Box is connected to the MC Unit, it first goes into T. BOX
LIMITED mode, in which only monitoring is possible. To execute the program
or jog, the mode must be switched to either T. BOX RESERVED or T. BOX
ENABLED. The operating mode can be changed only from the Teaching Box
itself.
For the procedure for changing the Teaching Box mode to either T. BOX
RESERVED or T. BOX ENABLED, refer to
Changing the Mode to T. BOX
RESERVED
in
11-2-2 Checking Operation from the Teaching Box
.
Summary of Contents for CS1W-MC221 -
Page 1: ...Motion Control Units Cat No W359 E1 04 CS1W MC221 V1 421 V1 OPERATION MANUAL ...
Page 2: ...CS1W MC221 V1 421 V1 Motion Control Units Operation Manual Revised February 2008 ...
Page 3: ...iv ...
Page 5: ...vi ...
Page 11: ...xii ...
Page 15: ...xvi ...
Page 19: ...xx ...
Page 27: ...xxviii Conformance to EC Directives 6 ...
Page 133: ...106 Installation Section 2 2 2 2 4 Dimensions CS1W MC421 CS1W MC221 ...
Page 173: ...146 Connecting Peripheral Devices Section 2 7 ...
Page 227: ...200 Command Area Section 3 6 ...
Page 351: ...324 Interface Specifics Section 5 4 ...
Page 513: ...486 Absolute Encoder Interface Specifications Section 9 7 ...
Page 575: ...548 Error Log Section 12 6 ...
Page 589: ...562 Performance Appendix A ...
Page 655: ...628 Control Bit Flag Timing Charts Appendix E ...
Page 683: ...656 Origin Search Patterns Appendix F ...
Page 685: ...658 Encoder Divider Rate and Rotation Speed for OMRON Servo Drivers Appendix G ...