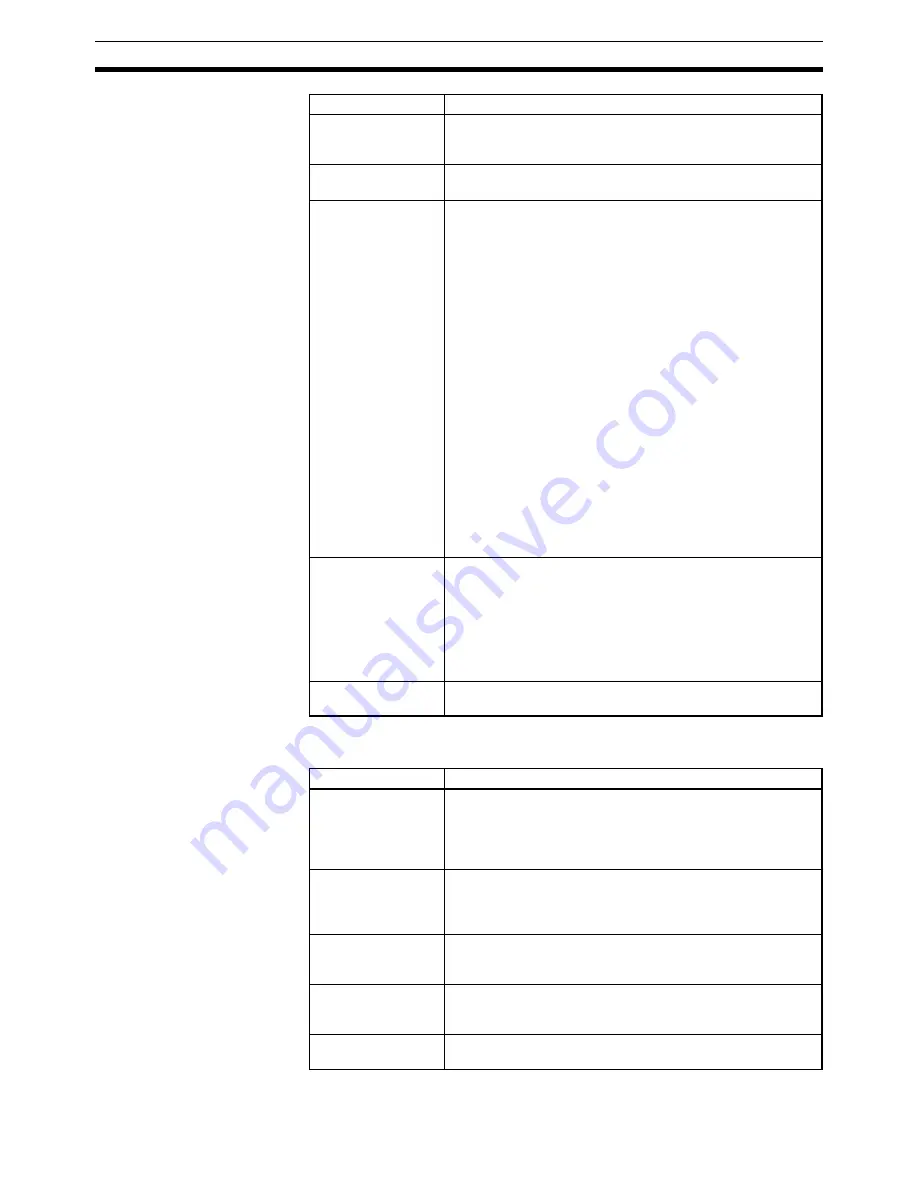
72
Overview of Version 1 Upgrades
Section 1-12
Relationship to Bits/Flags
The relationships of the electronic cam function to control bits and flags are
described in the following table.
G74/G75/G76
Enabled for electronic cam function. G75 is disabled, however,
for continuous operation after an error occurs when an oper-
and is specified.
G90/G91
None. The electronic cam function is unrelated to the coordi-
nate system.
G01 (E31) (Elec-
tronic gear or elec-
tronic cam)
In Stop Mode
When the electronic gear function is executed or when
“repeat” is set as the starting/ending condition for the elec-
tronic cam function, the next block is not executed.
In Pass Mode or In-position Check Off Mode
A second block can be preread and executed for the same
operating axis, and operation proceeds to the next block. If a
third electronic gear function or electronic cam function is exe-
cuted for the same operating axis, the operation waits for the
first electronic gear function or electronic cam function to be
completed.
Note
If the input axis or integrated axis for the electronic
gear/cam function is used as the operating axis for
another electronic gear/cam function, execute the com-
mand where the axis is not the operating axis for the
electronic gear/cam function first. These commands will
be automatically executed in this order even if they are
placed in the reverse order.
Also, if the G code commands for electronic gears/cams
serve as the input and output for each other and the
order cannot be determined, an MPG ratio overflow
error will occur.
G01 (E31) (Elec-
tronic cam/gear can-
cel)
In Stop Mode
When repeat is set as the end condition, the electronic cam
operation does not end, so these G codes cannot be exe-
cuted.
In Pass Mode or In-position Check Off Mode
The electronic cam function can be cancelled by this G-code
command.
G01 (E31) (Register
function)
Not related.
G code
Relationship to electronic cam function
Bit name
Relationship to electronic cam function
Automatic/Manual
Mode
If the mode is switched from automatic to manual during elec-
tronic cam function execution, the electronic cam function is
paused. Operation is stopped immediately, with no decelera-
tion. Continuous execution is possible if the operating axis is
not moved during the pause.
Forced Block End Bit Enabled for the electronic cam function. Operation is stopped
immediately with no deceleration. For continuous operation,
the previous operations are all cleared and execution pro-
ceeds again from the present block.
Pause Bit
Enabled for the electronic cam function. Operation is stopped
immediately with no deceleration. Continuous execution is
possible if the operating axis is not moved during the pause.
Servo-unlock Bit
Enabled for the electronic cam function. Operation is stopped
immediately with no deceleration. Continuous execution is not
possible.
Axis Operating Flag
Turns ON during electronic cam execution regardless of
inputs.
Summary of Contents for CS1W-MC221 -
Page 1: ...Motion Control Units Cat No W359 E1 04 CS1W MC221 V1 421 V1 OPERATION MANUAL ...
Page 2: ...CS1W MC221 V1 421 V1 Motion Control Units Operation Manual Revised February 2008 ...
Page 3: ...iv ...
Page 5: ...vi ...
Page 11: ...xii ...
Page 15: ...xvi ...
Page 19: ...xx ...
Page 27: ...xxviii Conformance to EC Directives 6 ...
Page 133: ...106 Installation Section 2 2 2 2 4 Dimensions CS1W MC421 CS1W MC221 ...
Page 173: ...146 Connecting Peripheral Devices Section 2 7 ...
Page 227: ...200 Command Area Section 3 6 ...
Page 351: ...324 Interface Specifics Section 5 4 ...
Page 513: ...486 Absolute Encoder Interface Specifications Section 9 7 ...
Page 575: ...548 Error Log Section 12 6 ...
Page 589: ...562 Performance Appendix A ...
Page 655: ...628 Control Bit Flag Timing Charts Appendix E ...
Page 683: ...656 Origin Search Patterns Appendix F ...
Page 685: ...658 Encoder Divider Rate and Rotation Speed for OMRON Servo Drivers Appendix G ...