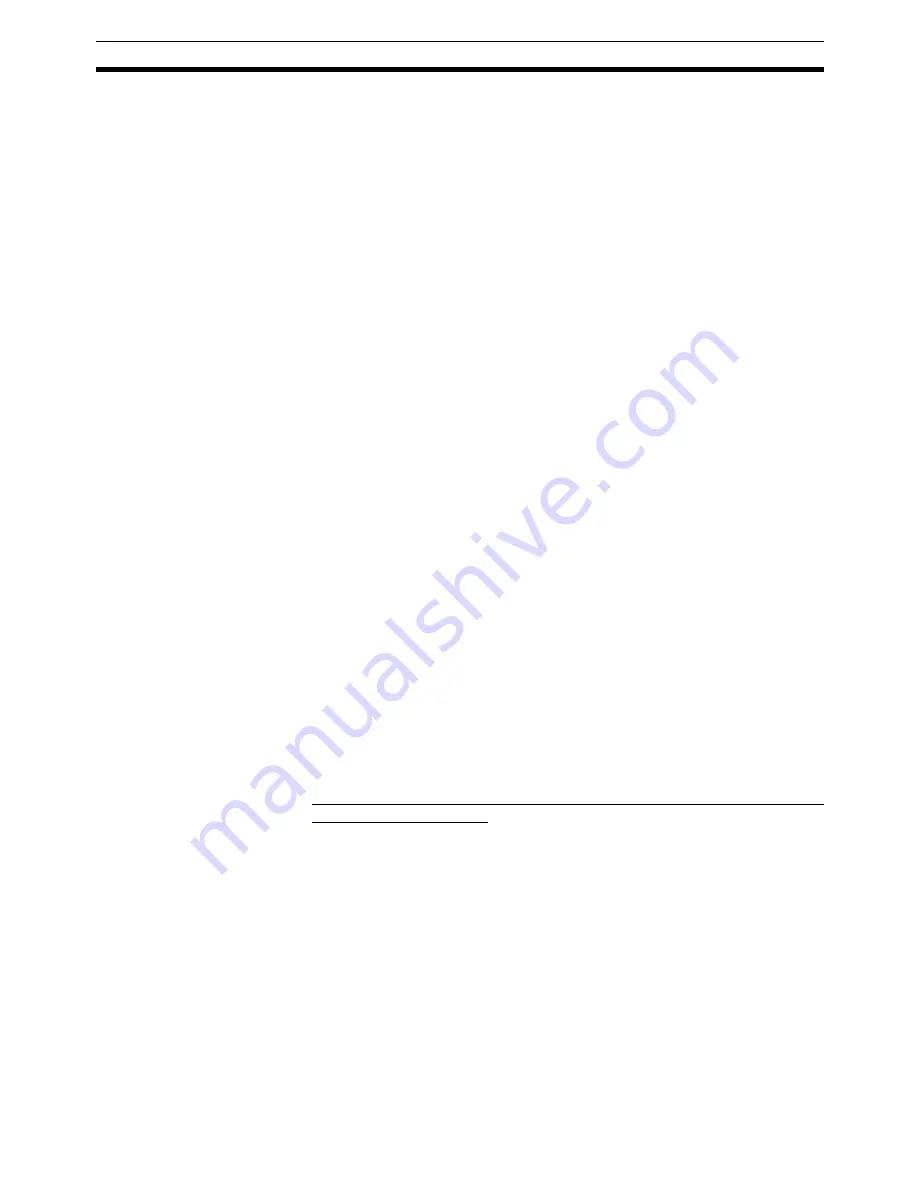
63
Overview of Version 1 Upgrades
Section 1-12
N010 G71 N009/A1010<30 ....... Waits until present position of X axis reaches
30 or higher.
N011 G63 A1004=11 ................. Changes gear ratio denominator to 11.
Etc.
Application Precautions
Note
(1) When the electronic gear function is executed in Stop Mode, there is no
operation completion, so the axis command for the next block is not exe-
cuted and the program does not end.
(2) Be careful of the execution timing when using G code commands for syn-
chronized control functions in more than one task. There is only one E
register, E31, that is used in the G code commands for synchronized con-
trol functions. When specifying the first position data address, be sure
that another address is not being specified in E31 in another task. Inter-
locking between tasks will be necessary.
Also, when in Stop Mode, operand table values indirectly referenced by
register E31 for the G01 operating axis (E31) must be held until the elec-
tronic gear function begins operating. When in Pass Mode or In-position
Check Off Mode, hold the values until operation moves to the next block
after the electronic gear function.
• The electronic gear function and the electronic cam function cannot be
simultaneously executed for the same operating axis. One of them must
be ended using the electronic cam/gear cancel function (CANCEL).
• When using customized functions other than synchronized control func-
tions (i.e., the memory link, linked traverse, or high-speed general-pur-
pose output functions), make sure that the position data for the respective
functions in the operand table do not overlap. For information on position
data for customized functions, refer to
Appendix A
.
• There may be cases where operations by input axes and integrated axes
do not function normally. For details, refer to
Appendix B
.
• Input axis speed (high and low) must be checked to ensure that operating
axis speed does not exceed the maximum feed rate.
• When an MPG or axis feedback (encoder) is used for the input axis, input
axis oscillation may affect the operating axis. If backlash compensation is
set for the operating axis, oscillation will occur in the backlash compensa-
tion range. The larger the backlash, the greater the oscillation becomes.
Note
It is recommended that a higher resolution encoder be used for the input axis
than for the operating axis.
• The gear ratio (numerator and denominator) must be set in pulses. Even if
the unit is set to millimeters, degrees, or inches in the parameters, the val-
ues must be converted to pulse units for the gear ratio numerator (output)
and gear ratio denominator (input) in the electronic gear function's oper-
and table.
• If the master axis and slave axis are switched and then the slave axis is
operated by the electronic gear function with respect to the master axis
encoder, the servomotor's present position will always have an error of
several pulses, and the calculation of the travel distance will gradually
deviate. This will require separate programming for position compensa-
tion.
• When the electronic gear function is executed, the override function for
the operating axis is disabled.
Summary of Contents for CS1W-MC221 -
Page 1: ...Motion Control Units Cat No W359 E1 04 CS1W MC221 V1 421 V1 OPERATION MANUAL ...
Page 2: ...CS1W MC221 V1 421 V1 Motion Control Units Operation Manual Revised February 2008 ...
Page 3: ...iv ...
Page 5: ...vi ...
Page 11: ...xii ...
Page 15: ...xvi ...
Page 19: ...xx ...
Page 27: ...xxviii Conformance to EC Directives 6 ...
Page 133: ...106 Installation Section 2 2 2 2 4 Dimensions CS1W MC421 CS1W MC221 ...
Page 173: ...146 Connecting Peripheral Devices Section 2 7 ...
Page 227: ...200 Command Area Section 3 6 ...
Page 351: ...324 Interface Specifics Section 5 4 ...
Page 513: ...486 Absolute Encoder Interface Specifications Section 9 7 ...
Page 575: ...548 Error Log Section 12 6 ...
Page 589: ...562 Performance Appendix A ...
Page 655: ...628 Control Bit Flag Timing Charts Appendix E ...
Page 683: ...656 Origin Search Patterns Appendix F ...
Page 685: ...658 Encoder Divider Rate and Rotation Speed for OMRON Servo Drivers Appendix G ...