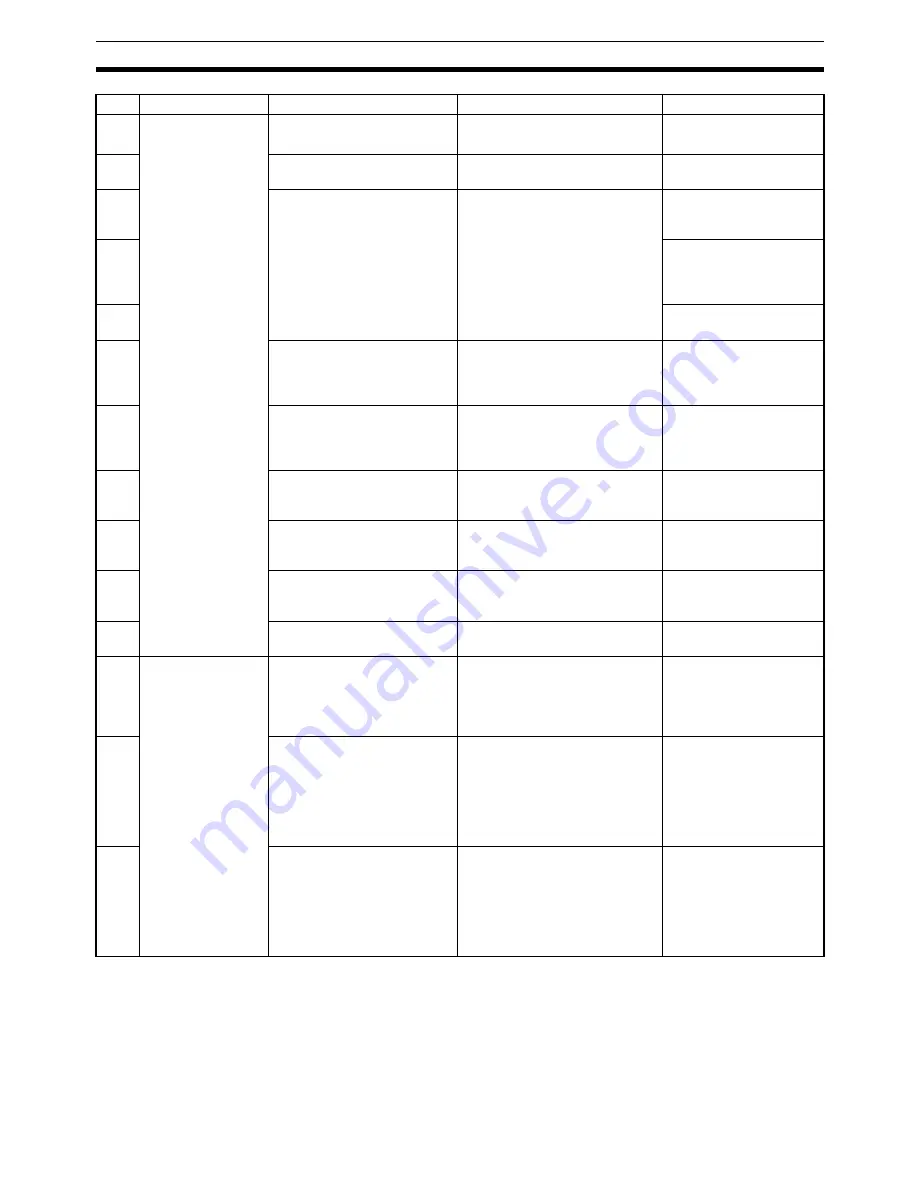
529
Troubleshooting Tables
Section 12-1
61
There is slippage in
positioning.
The slippage is not constant.
Malfunction due to noise.
Is shielded cable being used?
Use shielded cable.
62
The shield is not properly
grounded at the Servo Driver.
Check the ground wiring.
Correct the wiring.
63
The MC Unit’s output power
supply is not separated from
other power supplies.
Check whether the MC Unit’s
output power supply is
separated from other power
supplies.
Separate the MC output
power supply from other
power supplies.
64
Install a noise filter at the
primary side of the MC
Unit’s output power
supply.
65
Ground the MC Unit’s
output power supply.
66
Twisted-pair cable is not being
used for the pulse outputs.
Check whether twisted-pair
cable is being used for the pulse
outputs. (The connected voltage
is 0 V or 5/24 VDC.)
Use twisted-pair cable for
pulse outputs.
67
The cable between the MC
Unit and the Servo Driver is
not separated from other
power lines.
Check whether the cable is
separated from other power
lines.
Separate the cable from
other power lines.
68
The cable between the MC
Unit and the Servo Driver is
too long.
Check whether the cable is two
meters or less.
The maximum cable
length is two meters.
69
There is malfunctioning due to
noise from a welding
machine, inverter, etc.
Check whether there is a device
such as a welding machine or
inverter nearby.
Separate the Unit from
the noise source.
70
The RUN signal turns OFF
during operation.
Check whether the Servo
Driver’s RUN signal is turning
OFF during operation.
Turn ON the RUN signal
with the correct timing.
71
There is slippage in the
mechanical system.
Check for slippage by marking
the mechanical connections.
Tighten the connections.
72
An error has
occurred in the MC
Unit wiring.
There is an offset in the MC
Unit’s speed reference
voltage and the Servo Driver’s
speed reference input section.
---
Adjust the speed
reference offset at the
Servo Driver with the MC
Unit connected and servo
OFF.
73
The encoder signal and speed
reference wiring between the
MC Unit and the Servo Driver
is faulty or disconnected.
Set the wiring check parameter
to “no wiring check,” and check
to see if there is motor runaway.
(Perform the check with the
motor coupling disconnected.) If
runaway occurs, then there is a
wiring error.
Correct the wiring.
74
An MC Unit parameter setting
is wrong.
Set the wiring check parameter
for no wiring check, and check to
see if there is motor runaway.
(Perform the check with the
motor coupling disconnected.) If
runaway does not occur, then a
parameter setting is wrong.
Set the encoder polarity
to reverse in the MC
Unit’s machine
parameters.
No.
Problem
Probable causes
Items to check
Remedy
Summary of Contents for CS1W-MC221 -
Page 1: ...Motion Control Units Cat No W359 E1 04 CS1W MC221 V1 421 V1 OPERATION MANUAL ...
Page 2: ...CS1W MC221 V1 421 V1 Motion Control Units Operation Manual Revised February 2008 ...
Page 3: ...iv ...
Page 5: ...vi ...
Page 11: ...xii ...
Page 15: ...xvi ...
Page 19: ...xx ...
Page 27: ...xxviii Conformance to EC Directives 6 ...
Page 133: ...106 Installation Section 2 2 2 2 4 Dimensions CS1W MC421 CS1W MC221 ...
Page 173: ...146 Connecting Peripheral Devices Section 2 7 ...
Page 227: ...200 Command Area Section 3 6 ...
Page 351: ...324 Interface Specifics Section 5 4 ...
Page 513: ...486 Absolute Encoder Interface Specifications Section 9 7 ...
Page 575: ...548 Error Log Section 12 6 ...
Page 589: ...562 Performance Appendix A ...
Page 655: ...628 Control Bit Flag Timing Charts Appendix E ...
Page 683: ...656 Origin Search Patterns Appendix F ...
Page 685: ...658 Encoder Divider Rate and Rotation Speed for OMRON Servo Drivers Appendix G ...