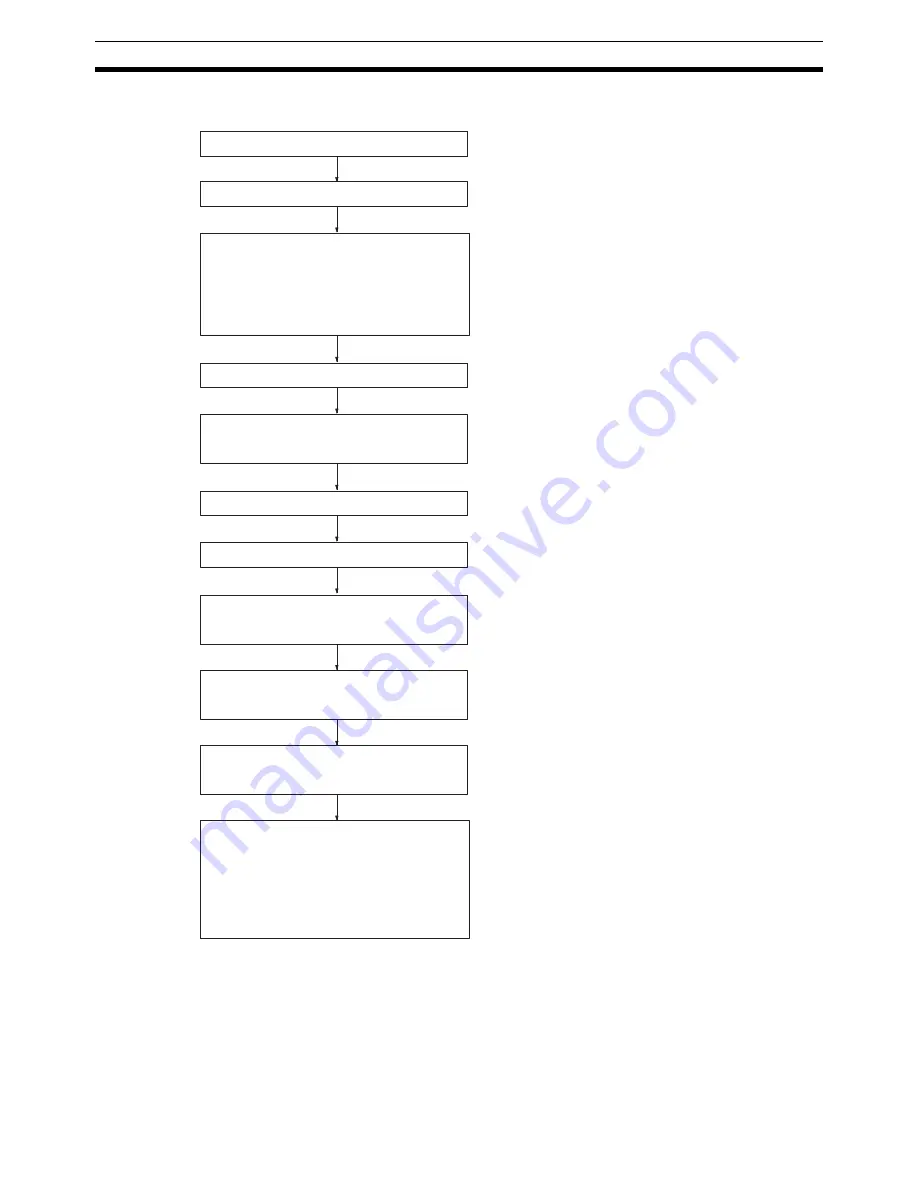
42
Basic Operating Procedure
Section 1-10
1-10 Basic Operating Procedure
Install the Unit.
Set the unit number.
Connections and wiring
Connect the Programming Device
(CX-Motion and CX-Programmer). Connect
the Teaching Box. Wire the I/O connectors.
Connect the servo driver. Connect the servo
driver to the servomotor.
Turn ON the power to the PLC
.
Create the I/O table using the
CX-Programmer or another Programming
Device.
Determine the number of tasks.
Use the CX-Motion to set the system parame-
ters, transfer them to the MC Unit, and back
them up to flash memory.
Use the CX-Motion to create an MC program
(G language), transfer it to the MC Unit, and
back it up to flash memory.
Create a CPU Unit ladder diagram program
and transfer it to the CPU Unit. Use
CX-Programmer.
Trial operation
Perform MC monitoring.
Check servo-lock, origin search, jogging, etc.
Check MC program operation. (Set manual/
automatic switch to automatic, and press the
start button.) Use CX-Motion or the Teaching
Box.
Refer to
Refer to
and to the
CX-Motion Online Help.
Change Teaching Box messages.
Refer to
Refer to the
CX-Programmer Operation
Manual
(W414 or W425).
Refer to the
CX-Motion Online Help
and to
Refer to the
CX-Motion Online Help
and to
Refer to the
CX-Programmer Operation
Manual
(W414 or W425).
Refer to
SECTION 2 Installation
Refer to
SECTION 2 Installation
Refer to
SECTION 2 Installation
2-7 Connecting Peripheral Devices
3-2 Determining the Task Configuration
3-3 System Parameters
3-6 Command Area
SECTION 11 Getting Started
Summary of Contents for CS1W-MC221 -
Page 1: ...Motion Control Units Cat No W359 E1 04 CS1W MC221 V1 421 V1 OPERATION MANUAL ...
Page 2: ...CS1W MC221 V1 421 V1 Motion Control Units Operation Manual Revised February 2008 ...
Page 3: ...iv ...
Page 5: ...vi ...
Page 11: ...xii ...
Page 15: ...xvi ...
Page 19: ...xx ...
Page 27: ...xxviii Conformance to EC Directives 6 ...
Page 133: ...106 Installation Section 2 2 2 2 4 Dimensions CS1W MC421 CS1W MC221 ...
Page 173: ...146 Connecting Peripheral Devices Section 2 7 ...
Page 227: ...200 Command Area Section 3 6 ...
Page 351: ...324 Interface Specifics Section 5 4 ...
Page 513: ...486 Absolute Encoder Interface Specifications Section 9 7 ...
Page 575: ...548 Error Log Section 12 6 ...
Page 589: ...562 Performance Appendix A ...
Page 655: ...628 Control Bit Flag Timing Charts Appendix E ...
Page 683: ...656 Origin Search Patterns Appendix F ...
Page 685: ...658 Encoder Divider Rate and Rotation Speed for OMRON Servo Drivers Appendix G ...