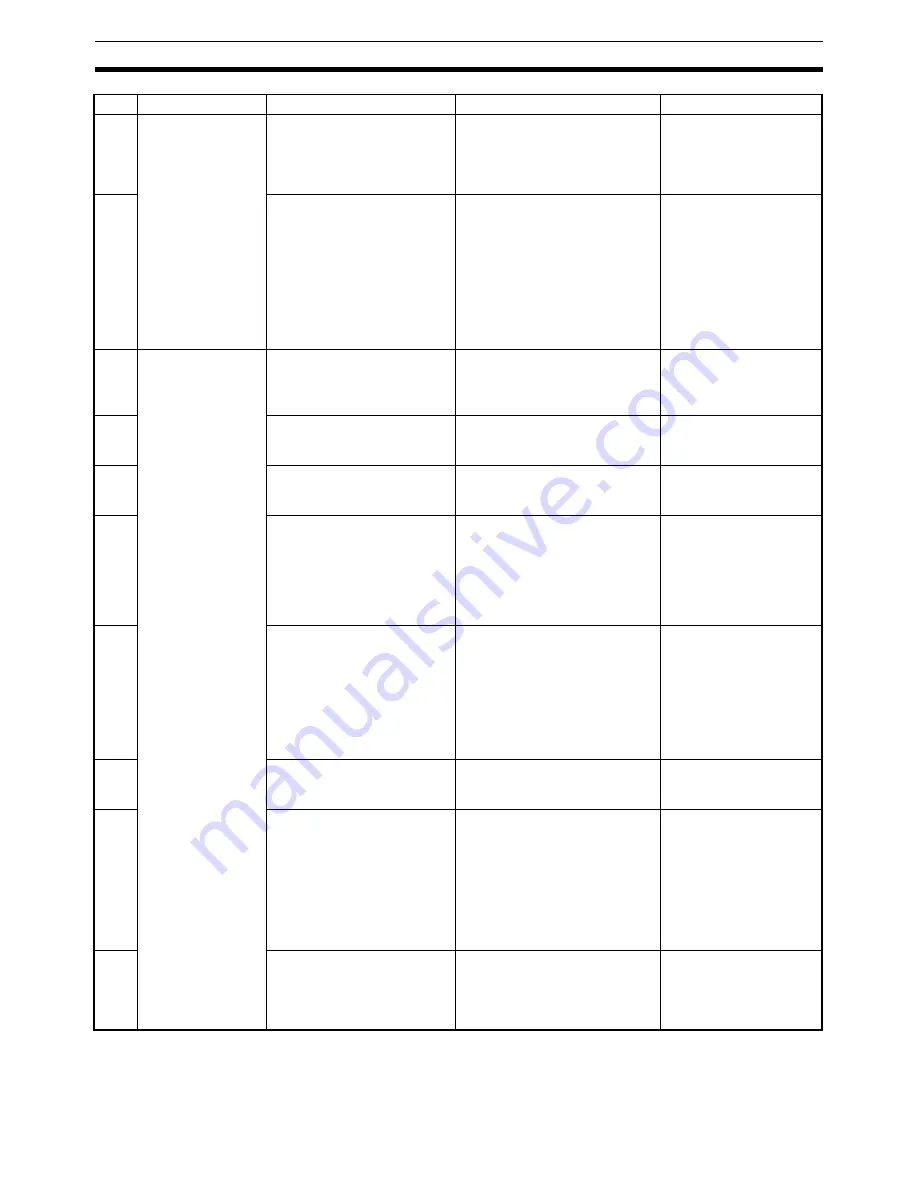
526
Troubleshooting Tables
Section 12-1
31
The origin
established by the
origin search
sometimes
changes.
There is some looseness in
couplings or other mechanical
connections.
Check whether there is any
deviation from the markings at
the couplings between the motor
and axes, or at any other
connections.
Tighten up the
connections.
32
There is no phase-Z margin.
Monitor the phase-Z margin. If
the value is near the
Servomotor’s encoder
resolution x the ratio (1, 2, or 4),
or near zero, a deviation of one
motor revolution may occur at
the time of the origin search due
to even a minute change in the
timing of sensor inputs.
Remove the motor
coupling and adjust it by
about a 1/4 turn, so that
the phase-Z margin
pulses will be about 1/2
of the Servomotor’s
encoder resolution x the
ratio (1, 2, or 4), and then
try executing the origin
search again.
33
Motor rotation is
unstable.
The parameters are set
incorrectly.
Check the MC Unit parameters
with the CX-Motion.
Set the parameters
correctly, transfer them to
the MC Unit, and write
them to flash memory.
34
The Servo Motor power lines
and encoder lines are wired
incorrectly.
Check the Servo Motor power
lines and encoder lines.
Correct the wiring.
35
The speed reference
(XOUT/YOUT) polarity is
wrong.
Check the speed reference
wiring.
Correct the wiring.
36
There is eccentricity in the
couplings connecting the
Servomotor axis and the
mechanical system. There
may be loose screws or load
torque fluctuation due to the
meshing of pulley gears.
Check the machinery. Try turning
the motor with no load (i.e., with
the machinery removed from the
coupling).
Adjust the machinery.
37
The gain adjustment is insuffi-
cient.
---
Execute Servomotor
autotuning.
Manually adjust the
Servomotor gain.
Adjust the servo
parameters with either
the CX-Motion or the
Teaching Box.
38
The wrong Servomotor is
selected (so it cannot be
adjusted).
Check the torque and inertia
ratings and select another
Servomotor.
Change to a suitable
Servomotor.
39
The Servomotor bearings are
damaged.
Turn OFF the Servo Driver
power. If the Servomotor has a
brake, turn ON the brake power
supply and release the brake,
and then manually turn the
motor’s output axis with the
motor’s power line disconnected
(because the dynamic brake
may be applied).
Replace the Servomotor.
40
The Servomotor windings are
disconnected.
With a tester, check resistance
between the Servomotor’s U, V,
and W power lines. There should
be a proper balance between the
line resistances.
Replace the Servomotor.
No.
Problem
Probable causes
Items to check
Remedy
Summary of Contents for CS1W-MC221 -
Page 1: ...Motion Control Units Cat No W359 E1 04 CS1W MC221 V1 421 V1 OPERATION MANUAL ...
Page 2: ...CS1W MC221 V1 421 V1 Motion Control Units Operation Manual Revised February 2008 ...
Page 3: ...iv ...
Page 5: ...vi ...
Page 11: ...xii ...
Page 15: ...xvi ...
Page 19: ...xx ...
Page 27: ...xxviii Conformance to EC Directives 6 ...
Page 133: ...106 Installation Section 2 2 2 2 4 Dimensions CS1W MC421 CS1W MC221 ...
Page 173: ...146 Connecting Peripheral Devices Section 2 7 ...
Page 227: ...200 Command Area Section 3 6 ...
Page 351: ...324 Interface Specifics Section 5 4 ...
Page 513: ...486 Absolute Encoder Interface Specifications Section 9 7 ...
Page 575: ...548 Error Log Section 12 6 ...
Page 589: ...562 Performance Appendix A ...
Page 655: ...628 Control Bit Flag Timing Charts Appendix E ...
Page 683: ...656 Origin Search Patterns Appendix F ...
Page 685: ...658 Encoder Divider Rate and Rotation Speed for OMRON Servo Drivers Appendix G ...