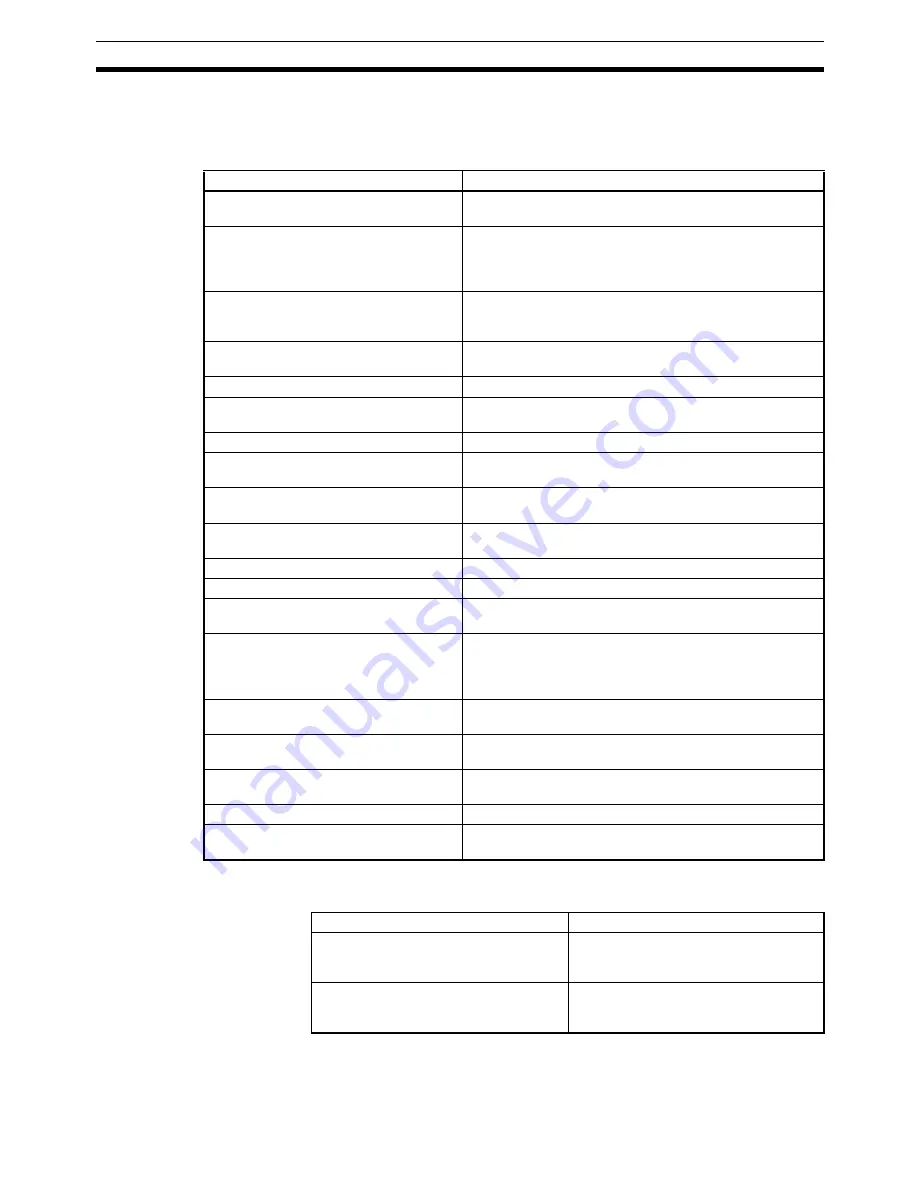
153
System Parameters
Section 3-3
Machine Parameters
Machine parameters determine the minimum unit setting, rotation direction,
stop method, and other machine configuration settings, as well as the operat-
ing procedure and type of servomotor used. The parameters are set for each
axis that is used (X, Y, Z and U axes).
Coordinate Parameters
Coordinate parameters are used to set the offset for each axis from the
machine origin or the reference origin.
The machine origin is the origin set at origin search and is where the encoder
counter reads zero. It is set from the absolute origin setting when an absolute
encoder is used.
Parameter name
Function
Minimum unit setting
Specifies the minimum unit for the machine system
settings: 1, 0.1, 0.01, 0.001. 0.0001.
Axis Mode/display unit
Specifies Normal Feed Mode or Unlimited Feed Mode at
Axis Mode and specifies the unit that will be used when
monitoring the present position: mm, inches, degrees,
pulses.
Rotation direction
Specifies whether the motor will rotate in forward or reverse
when the command voltage to the servomotor driver is
positive (+).
Emergency/limit input stopping methods
Specifies the stopping method used when an emergency
stop or limit input is received.
Encoder ABS/INC
Sets the type of encoder used.
Encoder resolution
Sets the number of encoder pulses output (encoder fre-
quency dividing ratio) when the servomotor rotates once.
Encoder ratio
Sets the encoder ratio: 1, 2 or 4
Encoder polarity
Sets whether the encoder will advance in phase A or phase
B when the servomotor is rotating in the forward direction.
Pulse rate
Sets how much the axis will move per feedback pulse
(numerator/denominator, set individually).
Max. motor frequency
Sets the number of servomotor rotations with a speed
reference of 10 V applied.
Positive (+) or negative (–) software limit
Sets the limit monitored in the software.
Origin search method
Sets the origin search operation mode.
Origin search direction
Sets whether to move in the positive or negative direction
when performing an origin search.
Origin deceleration method
Sets whether to use the origin proximity input signal or to
use the limit input signal as the origin proximity input signal
and it sets the deceleration method used when a limit input
signal is detected.
Origin proximity input logic
Sets whether the origin proximity input is normally open or
normally closed.
Wiring check
Decide to whether or not to perform wiring check at the time
of servo lock.
Wiring check time
Sets the time from test pulse output until the feedback
pulse is checked.
Wiring check pulses
Sets the number of test pulses in the wiring check.
ABS encoder default setting
The ABS encoder default setting is displayed when it is exe-
cuted.
Parameter name
Function
Reference origin offset value
Origin position in the reference
coordinate system (offset from the
machine origin)
Workpiece origin offset value
Origin position in the workpiece
coordinate system (offset from the
reference origin)
Summary of Contents for CS1W-MC221 -
Page 1: ...Motion Control Units Cat No W359 E1 04 CS1W MC221 V1 421 V1 OPERATION MANUAL ...
Page 2: ...CS1W MC221 V1 421 V1 Motion Control Units Operation Manual Revised February 2008 ...
Page 3: ...iv ...
Page 5: ...vi ...
Page 11: ...xii ...
Page 15: ...xvi ...
Page 19: ...xx ...
Page 27: ...xxviii Conformance to EC Directives 6 ...
Page 133: ...106 Installation Section 2 2 2 2 4 Dimensions CS1W MC421 CS1W MC221 ...
Page 173: ...146 Connecting Peripheral Devices Section 2 7 ...
Page 227: ...200 Command Area Section 3 6 ...
Page 351: ...324 Interface Specifics Section 5 4 ...
Page 513: ...486 Absolute Encoder Interface Specifications Section 9 7 ...
Page 575: ...548 Error Log Section 12 6 ...
Page 589: ...562 Performance Appendix A ...
Page 655: ...628 Control Bit Flag Timing Charts Appendix E ...
Page 683: ...656 Origin Search Patterns Appendix F ...
Page 685: ...658 Encoder Divider Rate and Rotation Speed for OMRON Servo Drivers Appendix G ...