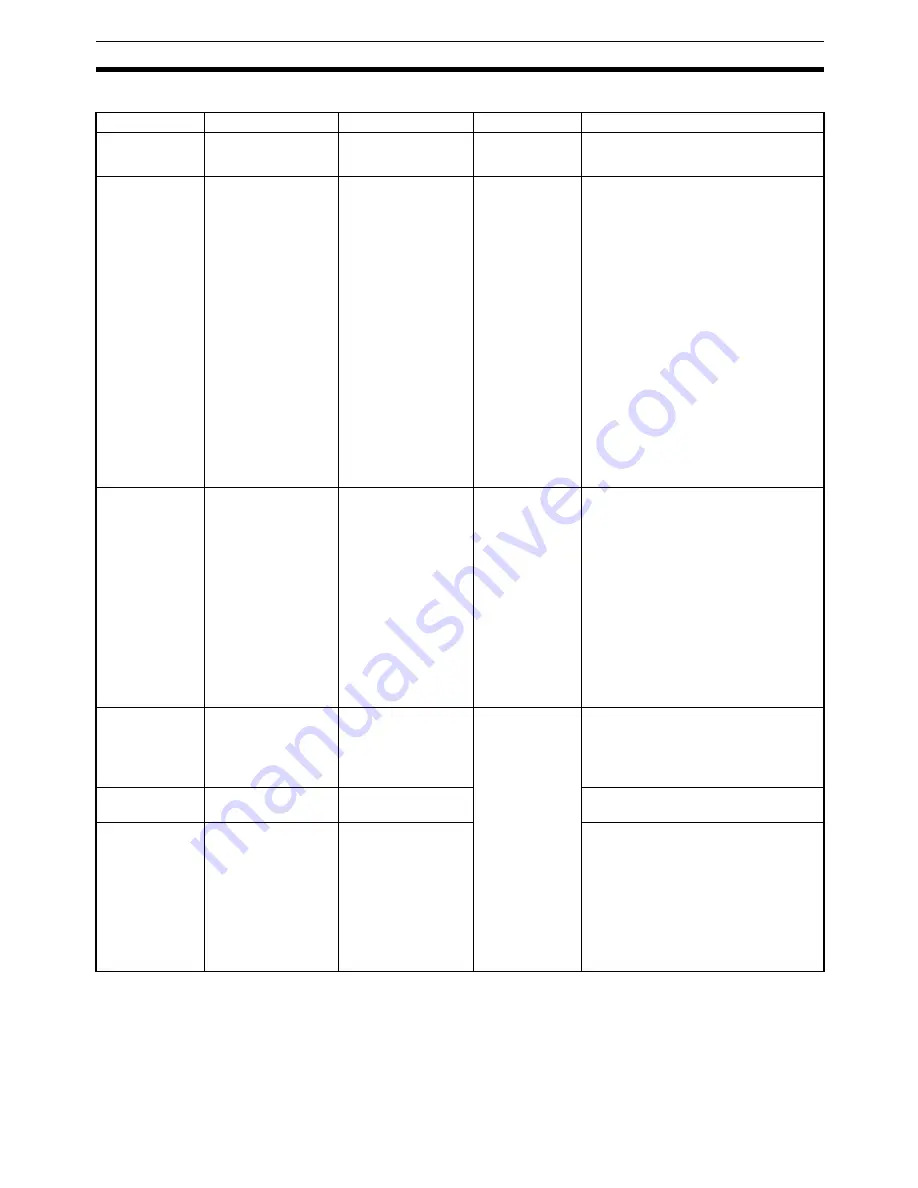
67
Overview of Version 1 Upgrades
Section 1-12
Operand Table
Data name
Data range
Unit
Description
First address
Function number
2
Note
Integers only
---
Specifies the function number.
Electronic cam function: 2
+1
Input axis
1st digit
0: MPG
1: X
2: Y
3: Z
4: U
2nd digit
0: Encoder
1: Position com-
mand value
Note
Integers only
---
Specifies the input axis for the elec-
tronic cam function. Either the encoder
or position command values can be
specified.
References the speed (p/2 ms) in each
control cycle (2 ms) and is not affected
by other input axis attributes (origin sta-
tus, errors, etc.). With input axis back-
lash compensation, there is no effect if
the position command value is used,
but there is if an encoder is used.
Note
1. MPG position command values can-
not be set.
2. The same axis as the operating axis
and integrated axis cannot be speci-
fied.
3. An axis from a separate task can be
specified.
+2
Integrated axis
0: None
1: X
2: Y
3: Z
4: U
Note
Integers only
---
Specifies the axis (position command
values) for adding outputs to electronic
cam function outputs.
References the speed (p/2 ms) in each
control cycle (2 ms) and is not affected
by other integrated axis attributes (ori-
gin status, errors, backlash compensa-
tion, etc.).
Note
1. The same axis as the operating axis
and input axis cannot be specified.
2. An axis from a separate task can be
specified.
+3
Stroke width
0 to 39,999,999
Pulses
mm
deg
inch
(See note 1.)
Specifies the operating axis stroke
width (i.e., the operating axis travel dis-
tance per cam rotation).
This value will be the standard for the
cam table data (stroke ratio).
+4
Cam rotation dis-
tance
0.0001 to
39,999,999
Specifies the distance of a single rota-
tion (360
°
) of the input axis.
+5
Cam start position
0 to 39,999,999
Sets the position to which the operating
axis is to move using the input axis
position. This is the parameter that
shifts the cam table phase. When cam
operation is started, the operation
begins from the angle in the cam table
that corresponds to this position.
Note
A value smaller than the cam
rotation distance must be set.
Summary of Contents for CS1W-MC221 -
Page 1: ...Motion Control Units Cat No W359 E1 04 CS1W MC221 V1 421 V1 OPERATION MANUAL ...
Page 2: ...CS1W MC221 V1 421 V1 Motion Control Units Operation Manual Revised February 2008 ...
Page 3: ...iv ...
Page 5: ...vi ...
Page 11: ...xii ...
Page 15: ...xvi ...
Page 19: ...xx ...
Page 27: ...xxviii Conformance to EC Directives 6 ...
Page 133: ...106 Installation Section 2 2 2 2 4 Dimensions CS1W MC421 CS1W MC221 ...
Page 173: ...146 Connecting Peripheral Devices Section 2 7 ...
Page 227: ...200 Command Area Section 3 6 ...
Page 351: ...324 Interface Specifics Section 5 4 ...
Page 513: ...486 Absolute Encoder Interface Specifications Section 9 7 ...
Page 575: ...548 Error Log Section 12 6 ...
Page 589: ...562 Performance Appendix A ...
Page 655: ...628 Control Bit Flag Timing Charts Appendix E ...
Page 683: ...656 Origin Search Patterns Appendix F ...
Page 685: ...658 Encoder Divider Rate and Rotation Speed for OMRON Servo Drivers Appendix G ...