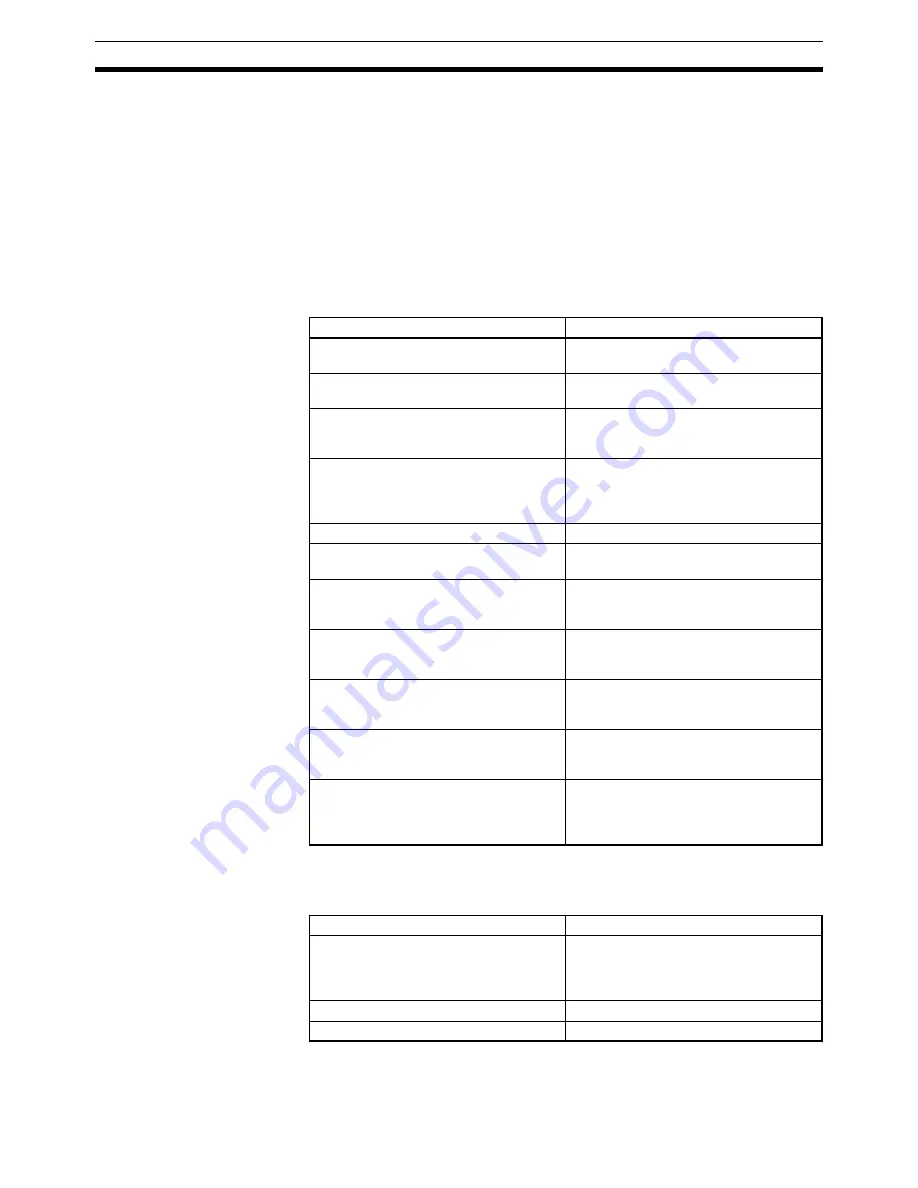
154
System Parameters
Section 3-3
The desired reference coordinate system can be set using a G code.
G50: Reference coordinate system
G51: Workpiece coordinate system
It is easier to use the workpiece origin offset change code (G53) for multiple
positioning in the same pattern. This is because coordinate parameter set-
tings will not change if the workpiece origin is changed from a G language
program.
Feed-rate Parameters
Feed-rate parameters are used to set the maximum feed, maximum interpola-
tion feed and other rate settings, acceleration and deceleration time settings,
acceleration and deceleration curve type settings, and the MPG ratio/elec-
tronic gear setting for each axis.
Zone Parameters
The following values are set as zone parameters. A zone is a specified range
for each axis. If the present position is in a zone, then the zone flag in the PLC
interface area will turn ON (1). A maximum of 8 zones can be set per axis.
Parameter name
Function
Maximum feed rate
Sets the maximum feed rate in PTP
operation.
Maximum interpolation feed rate
Sets the maximum feed rate in
interpolation operation.
High-speed origin search feed rate
When an origin search is executed, it is
performed at this feed rate until an origin
proximity sensor input is received.
Low-speed origin search feed rate
When an origin search is executed, it is
performed at this feed rate until phase Z
is detected after an origin proximity
sensor input is received.
Maximum jog feed rate
Sets the maximum jog feed rate.
Acceleration/deceleration curve
Specifies whether the acceleration/decel-
eration curve is trapezoidal or S-shaped.
Acceleration time
Sets the time required to accelerate from
zero to the maximum feed rate in PTP
operation.
Deceleration time
Sets the time required to decelerate from
the maximum feed rate to zero in PTP
operation.
Interpolation acceleration time
Sets the time required to accelerate from
zero to the maximum interpolation feed
rate in interpolation operation.
Interpolation deceleration time
Sets the time required to decelerate from
the maximum interpolation feed rate to
zero in interpolation operation.
MPG ratio (1 to 4)/electronic gear (1 to 4) A maximum of four ratios can be set for
pulses when an MPG or sync encoder is
used (numerator and denominator set
separately).
Parameter name
Function
Zone specification
Sets whether or not to use the zone
function and it sets the timing that will
make the zone setting valid if the function
is used.
Negative zone setting
Sets the lower limit of the zone.
Positive zone setting
Sets the upper limit of the zone.
Summary of Contents for CS1W-MC221 -
Page 1: ...Motion Control Units Cat No W359 E1 04 CS1W MC221 V1 421 V1 OPERATION MANUAL ...
Page 2: ...CS1W MC221 V1 421 V1 Motion Control Units Operation Manual Revised February 2008 ...
Page 3: ...iv ...
Page 5: ...vi ...
Page 11: ...xii ...
Page 15: ...xvi ...
Page 19: ...xx ...
Page 27: ...xxviii Conformance to EC Directives 6 ...
Page 133: ...106 Installation Section 2 2 2 2 4 Dimensions CS1W MC421 CS1W MC221 ...
Page 173: ...146 Connecting Peripheral Devices Section 2 7 ...
Page 227: ...200 Command Area Section 3 6 ...
Page 351: ...324 Interface Specifics Section 5 4 ...
Page 513: ...486 Absolute Encoder Interface Specifications Section 9 7 ...
Page 575: ...548 Error Log Section 12 6 ...
Page 589: ...562 Performance Appendix A ...
Page 655: ...628 Control Bit Flag Timing Charts Appendix E ...
Page 683: ...656 Origin Search Patterns Appendix F ...
Page 685: ...658 Encoder Divider Rate and Rotation Speed for OMRON Servo Drivers Appendix G ...