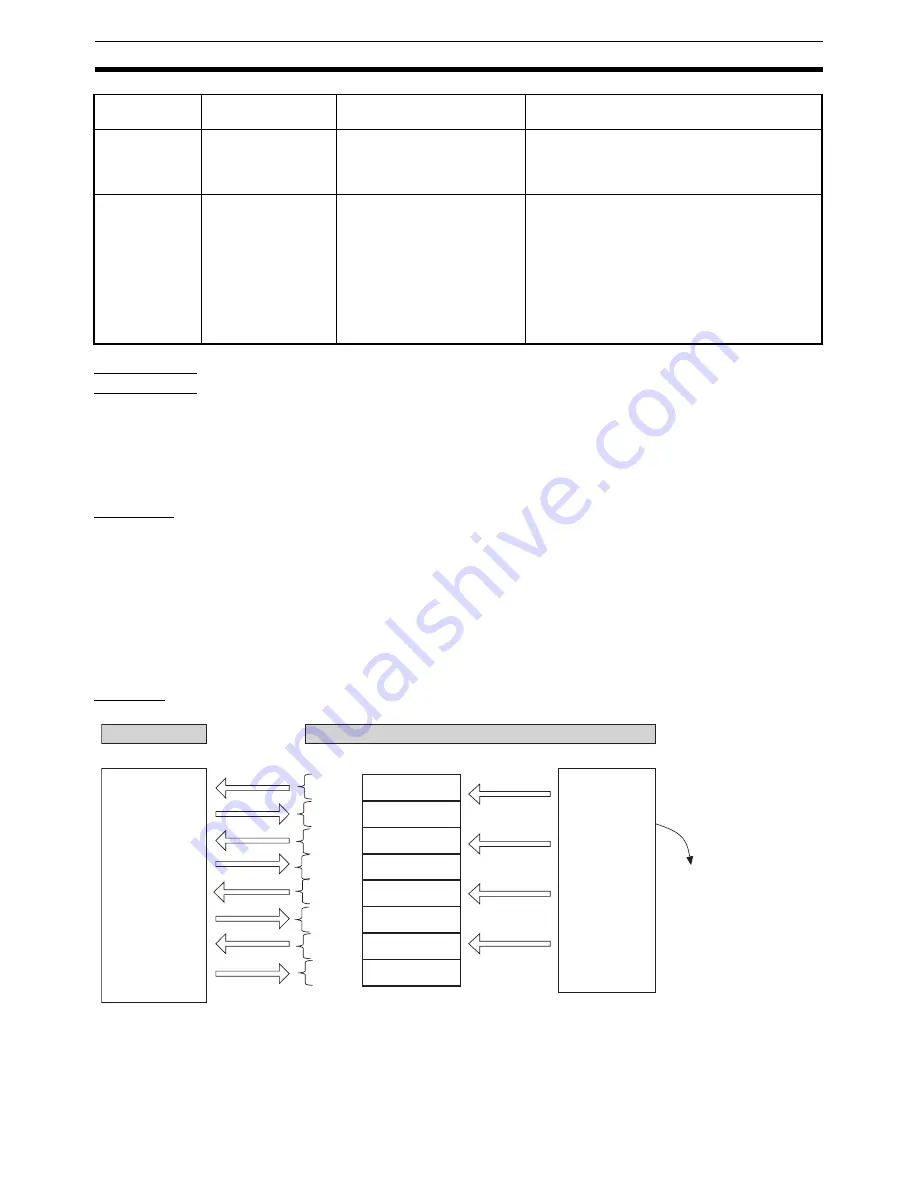
88
Overview of Version 1 Upgrades
Section 1-12
Application
Precautions
• The linked traverse function is enabled from when the program is exe-
cuted from the start after the customized functions have been enabled.
• When the rotational speed [p/s] is lower than the traverse axis speed [p/
s]), unevenness can occur in the speed of the traverse axis. Adjust the
pulse rate if unevenness occurs.
1-12-1-7
Memory Link Function
Overview
Position data addresses A1970 to A1985 can be allocated to user-specified
addresses in I/O memory in the CIO, DM, or EM Areas. This reduces the work
required to write ladder programs because this position data is automatically
transferred between the CPU Unit and MC Unit without any special program-
ming.
The data is exchanged at the same time as the CIO Area words allocated to
the MC Unit. Data can also be changed (from MC Unit position data to CPU
Unit only) when positioning with travel distances set with the stopover func-
tion.
Settings
Waveform
Triangular control
The acceleration/deceleration
time is maintained for each
block and the speed is
decreased.
Triangular control is performed for the linked
G32 commands.
Performance
Minimum operating
time per block
None
Note
Passing, however, will
not be performed if the
time is the same or
below the minimum
pass time.
2 ms
Note
If the time is less than 2 m, an error will
occur (added axis speed exceeded) and
the rotating axis will decelerate to a stop.
The traverse axis will stop after the accu-
mulated pulses have been consumed.
When this error occurs, continuous opera-
tion cannot be continued (a traverse con-
tinuation error will occur).
Classification
Functionality
Normal traverse operation
in Pass Mode (for reference)
Linked traverse (customized function)
CIO, DM, or
EM Area
A1970
A1971
A1972
A1973
A1974
A1975
A1976
A1977
A1978
A1979
A1980
A1981
A1982
A1983
A1984
A1985
PLC
A0000 to A1999
Cyclic refresh
MC Unit
Output data area 1
Input data area 1
Copied on
stopover output
(1) Addresses set
with IOWR
instruction.
Settings made
separately for
each area.
Output data area 2
Input data area 2
Output data area 3
Input data area 3
Output data area 4
Input data area 4
(2) Addresses
set with A1986
and A1989 for
each area.
See (2) A1986
to A1989
below for an
explanation.
Summary of Contents for CS1W-MC221 -
Page 1: ...Motion Control Units Cat No W359 E1 04 CS1W MC221 V1 421 V1 OPERATION MANUAL ...
Page 2: ...CS1W MC221 V1 421 V1 Motion Control Units Operation Manual Revised February 2008 ...
Page 3: ...iv ...
Page 5: ...vi ...
Page 11: ...xii ...
Page 15: ...xvi ...
Page 19: ...xx ...
Page 27: ...xxviii Conformance to EC Directives 6 ...
Page 133: ...106 Installation Section 2 2 2 2 4 Dimensions CS1W MC421 CS1W MC221 ...
Page 173: ...146 Connecting Peripheral Devices Section 2 7 ...
Page 227: ...200 Command Area Section 3 6 ...
Page 351: ...324 Interface Specifics Section 5 4 ...
Page 513: ...486 Absolute Encoder Interface Specifications Section 9 7 ...
Page 575: ...548 Error Log Section 12 6 ...
Page 589: ...562 Performance Appendix A ...
Page 655: ...628 Control Bit Flag Timing Charts Appendix E ...
Page 683: ...656 Origin Search Patterns Appendix F ...
Page 685: ...658 Encoder Divider Rate and Rotation Speed for OMRON Servo Drivers Appendix G ...