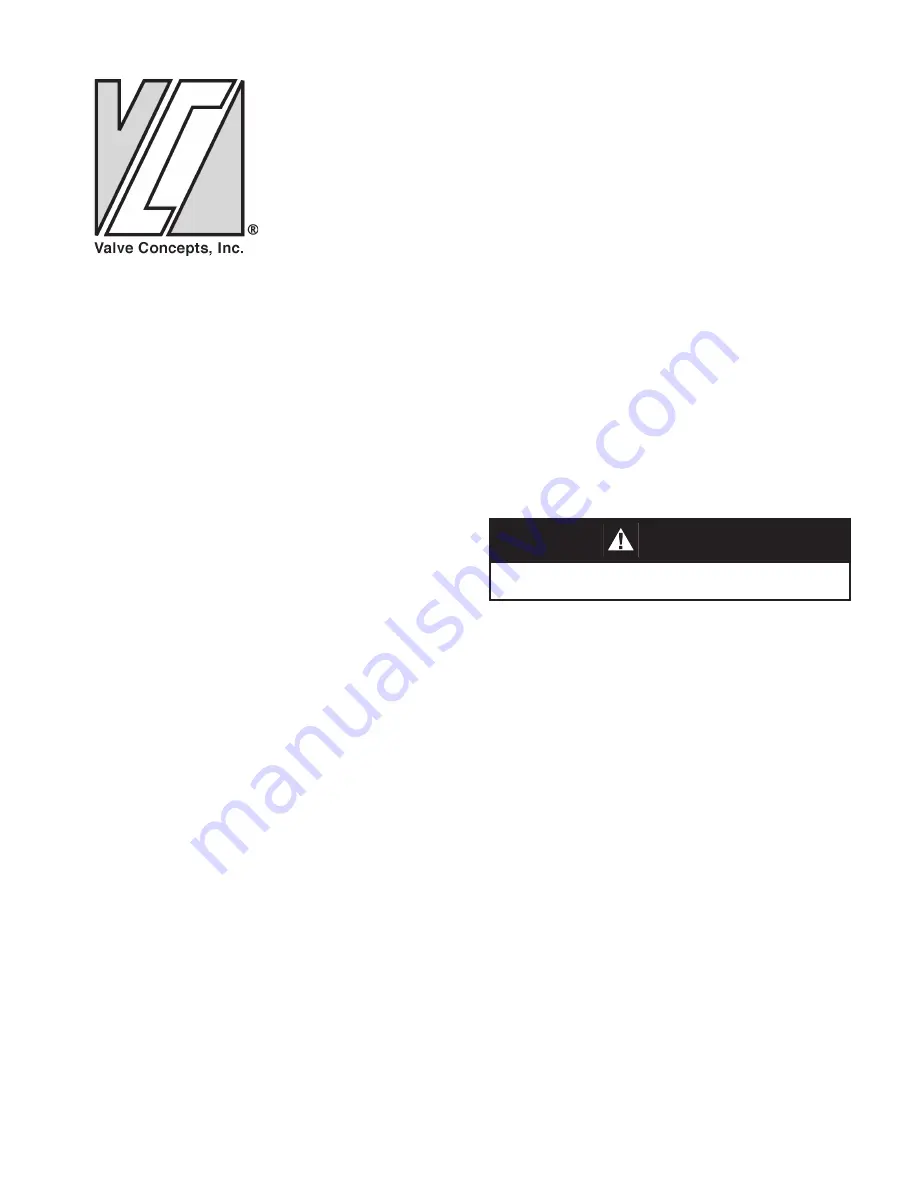
INSTALLATION, OPERATION AND MAINTENANCE MANUAL (IOM)
IOM-1078
02-20
SECTION I
I. DESCRIPTION AND SCOPE
Model 1078
Vacu-Gard Pilot Operated Blanketing Valve
Clean out blanket gas supply lines prior to valve
installation to get rid of dirt, sand, loose scales and
other foreign particles trapped in the piping. This is
particularly true for new tanks and/or new piping. One
way to accomplish this is to blow out the lines from the
supply side up to the connection to the Vacu-Gard inlet.
SECTION III
III. INSTALLATION
It is always good practice to install a main line filter
upstream of any tank blanketing valve. The element
should be approximately 5-40 microns with a flow ca-
pacity at least equal to or greater than that of the Vacu-
Gard.
The valve should be installed in the normal upright po-
sition. The inlet is horizontal and the outlet is vertical
downward. An optional horizontal outlet is available for
the remote sensing design only. All outlet piping from
the valve body to the vessel must be at least as large
or larger than the outlet port in the body. Keep piping as
short as possible for best valve performance.
The Model 1078 Vacu-Gard is a pilot operated
blanketing valve intended for installation on top of
medium to large storage tanks. Available with either
FNPT or flange end connections, 1” size available with
SECTION II
II. PRIOR TO INSTALLATION
150 lb. integral cast flanges. 1” size valve bodies are
cast 316 stainless steel (CF3M). 2” size valve bodies
are available in cast carbon steel (WCB) or stainless
steel (CF3M). All sizes have 316 SST Trim.
CAUTION
Follow your company’s safety procedures to avoid
injury to personnel or damage to equipment.
For Remote Sensing:
The sense line should be a 1/2” O.D. tube (or larger)
and the length should not exceed fifteen feet. Longer
lengths may be used with larger diameter sense lines.
The sense line should slope downward from the pilot to
the tank to allow condensate, if any, to drain back into
the tank. (The sense port is the port on the side of the
pilot body marked with an “S”. A “tee” may be added to
the sense port for gauging pressure in the vessel.)
For Dip-Tube Sensing:
The integral dip-tube line must protrude into the tank at
least 6” below the roof.
NOTE:
The port at the end of the main valve body op-
posite the inlet is not a sense port. This port should not
be used for pressure gauging since the pressure at this
point may be higher than the maximum tank pressure
and may cause damage to the gauge.
ISO Registered Company