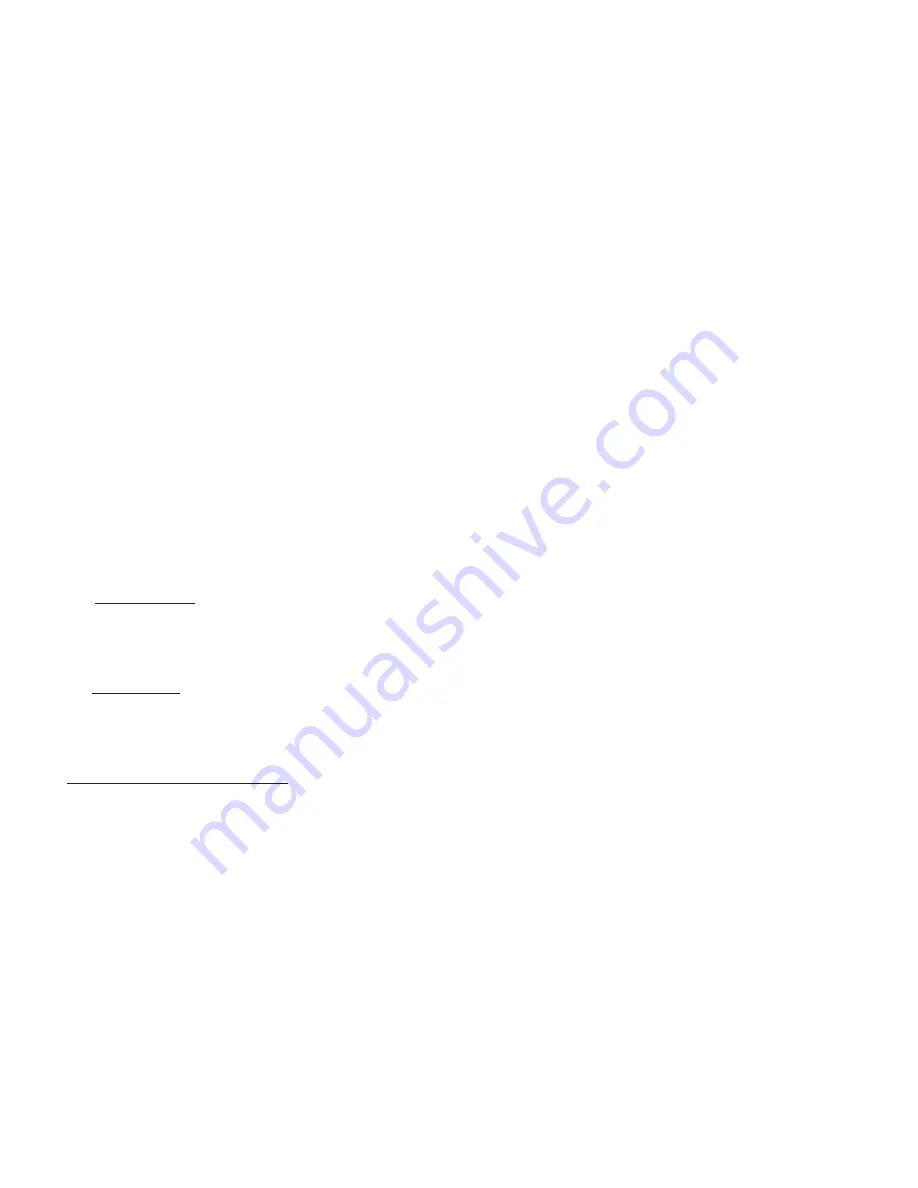
6
IOM-1078
PILOT INTERNALS:
Install new o-ring (35) around the
groove adjacent to the threads on pilot mount (37)(for
1” SIZE); on pilot connector (47) (on 2” SIZE). Install
o-ring (21) around the outside groove of the spindle
(20). Install o-ring (22) in the internal groove at the
lower end of the spindle.
NOTE:
O-RINGS MUST BE
ORDERED FROM THE FACTORY.
Position spacer (26) on top of the pilot mount /
connector. Insert the spring (25) and guide pin (24) into
the spindle (20) and place these parts into the center
of the spacer with the small end of spindle oriented up.
Lower the pilot body over the top of the spindle. Ensure
that the top of the spindle enters into the small opening
in the center of the body.
NOTE:
The lower diaphragm
case may not have been removed from the pilot body.
Press down on the top of the pilot body or center of the
lower diaphragm case and slowly and evenly rotate CW
to engage the threads on the pilot mount or connector
to the pilot body. It is not necessary to use any tool to
ensure a tight seal between the pilot body and the pilot
mount / connection.
NOTE:
The inlet for the pilot body should be in-line and
directly above the inlet of the main body. If the pilot
ports need re-positioning:
For 1” SIZE:
Loosen the cap screws (11) of the
mounting plate and turn the pilot mount to orient the
pilot ports in the proper direction. Re-tighten the cap
screws to 13-15 ft-lbs.
For 2” SIZE:
Use a combination of tightening the
pilot connector (47) onto the piston housing (124) and/
or rotating the piston housing one bolt hole. Tighten the
cap screws to 15-18 ft-lbs.
For DIAPHRAGM ASSEMBLY:
Install center bolt
(17) in a vise with the threaded end up. Install one
bolt gasket (18) between the center bolt and the lower
support plate (16) as shown on the drawing.
NOTE:
The support plate should be install with the smooth
side up.
Lay the diaphragm (13) on top of the lower support
plate.
NOTE:
Place diaphragm with the flute facing up
for pressure set point or facing down for vacuum set
point.
An identical gasket (18) is used between the upper
surface of the sense diaphragm (13) and the bottom
side of the upper support plate (16).
NOTE:
The
support plate should be install with the smooth side
down. This is to ensure a tight squeeze on both sides
of the sense diaphragm to effect a tight seal.
Install washers (33), lockwasher (12) and nut (015).
Torque nut 13-15 ft-lbs. Place the diaphragm assembly
on the lower case and align the bolt holes. Align the
holes in the ring gasket (14) and place it on top of the
diaphragm assembly. Position spring (7) in the center
of the diaphragm assembly.
NOTE:
Washers are used to center the lower end of
the spring. It may sometimes be necessary to “thread”
the spring onto the washer or onto spring button (6).
You will find that turning the end of the spring in one
direction against the spring button or washers will tend
to close the coils and make installation more difficult.
However, turning the spring in the opposite direction
will tend to open the coils for easier installation.
Apply anti-seize compound to the recess in the spring
button (6) and set spring button on top of the spring.
Align the match marks between the upper and lower
cases and place the upper diaphragm case assembly
on top of the ring gasket (14).
NOTE:
The vent outlet
for the upper case should align with the pilot body’s
inlet.
Install cap screws,(11), washers (12) and nuts (15).
Tighten to 13 - 15 ft-lbs. Thread adjusting screw (2)
with jam nut (3) into the spring bonnet (5). Install
closing cap (1).
Reconnect all tubing, Ensure all tubing is clean and
unobstructed.