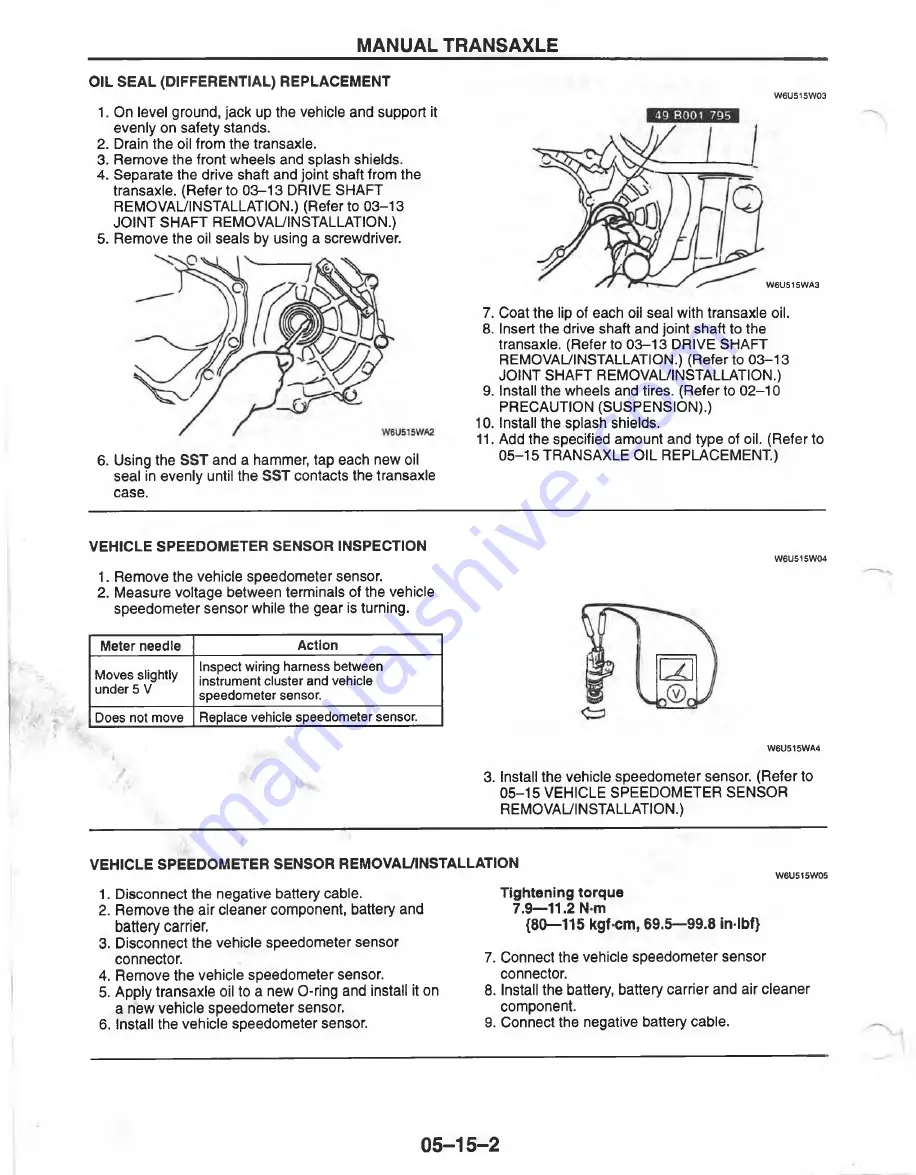
MANUAL TRANSAXLE
OIL SEAL (DIFFERENTIAL) REPLACEMENT
1. On level ground, jack up the vehicle and support it
evenly on safety stands.
2. Drain the oil from the transaxle.
3. Remove the front wheels and splash shields.
4. Separate the drive shaft and joint shaft from the
transaxle. (Refer to 03-13 DRIVE SHAFT
REMOVAL/INSTALLATION.) (Refer to 03-13
JOINT SHAFT REMOVAL/INSTALLATION.)
5. Remove the oil seals by using a screwdriver.
6. Using the
SST
and a hammer, tap each new oil
seal in evenly until the
SST
contacts the transaxle
case.
7. Coat the lip of each oil seal with transaxle oil.
8. Insert the drive shaft and joint shaft to the
transaxle. (Refer to 0 3 -1 3 DRIVE SHAFT
REMOVAL/INSTALLATION.) (Refer to 0 3 -1 3
JOINT SHAFT REMOVAL/INSTALLATION.)
9. Install the wheels and tires. (Refer to 02-10
PRECAUTION (SUSPENSION).)
10. Install the splash shields.
11. Add the specified amount and type of oil. (Refer to
05-15 TRANSAXLE OIL REPLACEMENT.)
VEHICLE SPEEDOMETER SENSOR INSPECTION
1. Remove the vehicle speedometer sensor.
2. Measure voltage between terminals of the vehicle
speedometer sensor while the gear is turning.
Meter needle
Action
Moves slightly
under 5 V
Inspect wiring harness between
instrument cluster and vehicle
speedometer sensor.
Does not move
Replace vehicle speedometer sensor.
W 6 U 5 1 S W 0 4
W 6 U 5 1 5 W A 4
3. Install the vehicle speedometer sensor. (Refer to
05-15 VEHICLE SPEEDOMETER SENSOR
REMOVAL/INSTALLATION.)
VEHICLE SPEEDOMETER SENSOR REMOVAL/INSTALLATION
1. Disconnect the negative battery cable.
2. Remove the air cleaner component, battery and
battery carrier.
3. Disconnect the vehicle speedometer sensor
connector.
4. Remove the vehicle speedometer sensor.
5. Apply transaxle oil to a new O-ring and install it on
a new vehicle speedometer sensor.
6. Install the vehicle speedometer sensor.
W 6 U 5 1 5 W 0 5
T ig h te n in g to rq u e
7.9— 11.2 N m
{80— 115 kgf cm, 69.5— 99.8 in-lbf}
7. Connect the vehicle speedometer sensor
connector.
8. Install the battery, battery carrier and air cleaner
component.
9. Connect the negative battery cable.
W 6 U 5 1 5 W 0 3
W 6 U 5 1 5 W A 3
0 5 -1 5 -2
Summary of Contents for MX-6 1998
Page 1: ......
Page 501: ...STARTING SYSTEM 3 If not as specified replace the starter interlock switch 01 19 3...
Page 803: ...MANUAL TRANSAXLE W 6 U 5 1 5 W A C 05 15 7...
Page 934: ...CONTROL SYSTEM CONTROL SYSTEM STRUCTURAL VIEW W6U740WA0 07 40 2...
Page 983: ...SERVICE TOOLS 08 60 SERVICE TOOLS 08 RESTRAINTS S S T 08 60 1 08 RESTRAINTS SST 08 60 1...