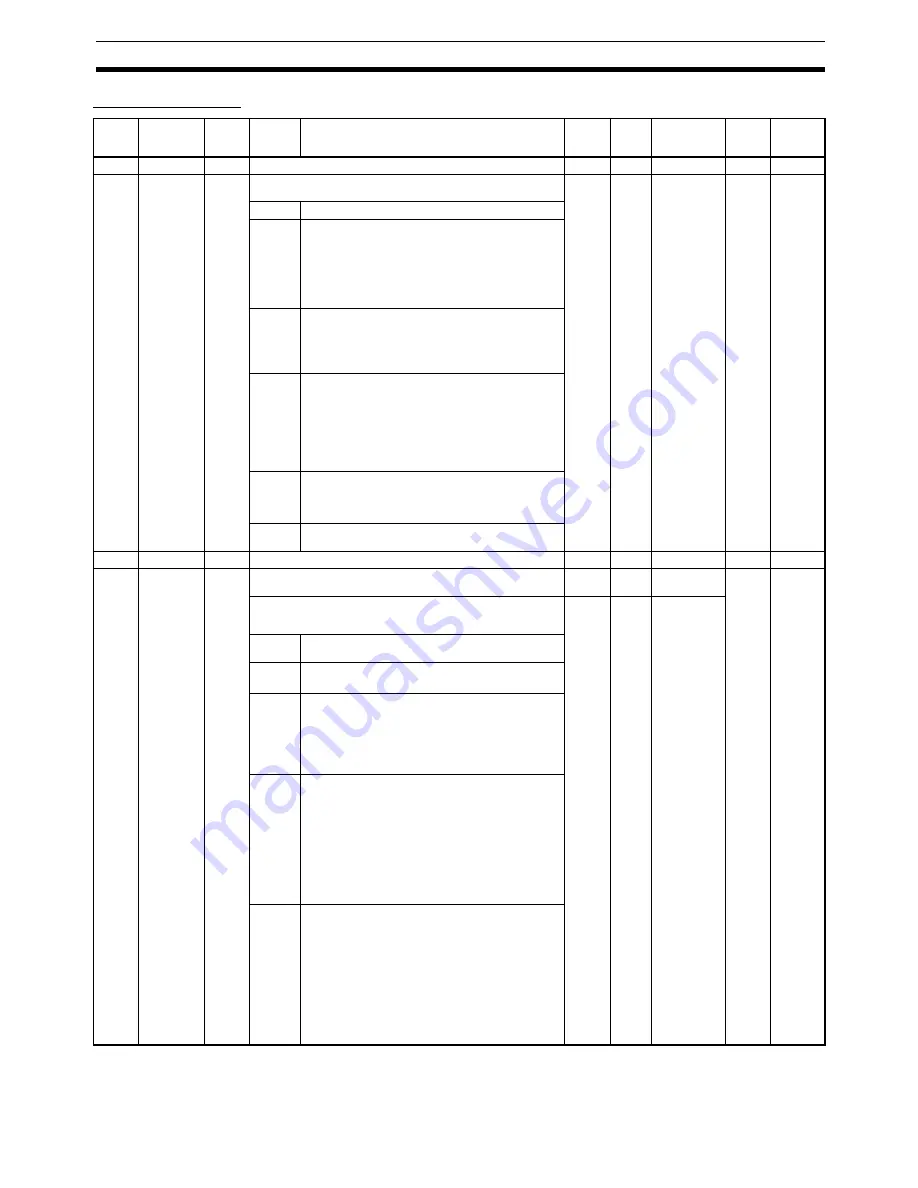
117
Servo Parameter Area
Section 4-5
Parameter Tables
Param-
eter
No.
Parameter
name
Param-
eter
size
Setting
Explanation
Default
setting
Unit
Setting
range
Enable
setting
Details
Pn000
Reserved
---
Do not change.
1
---
---
---
Pn001
Default Dis-
play
2
Selects the data to be displayed on the 7-segment LED display on
the front panel.
0
---
0 to 4
Online
0
Normal status ("--" Servo OFF, "00" Servo ON)
1
Indicates the machine angle from 0 to FF hex.
0 is the zero position of the encoder. The angle
increases when the Servomotor turns forward.
The count continues from "0" after exceeding "FF".
When using an incremental encoder, the display shows
"nF" (not Fixed) until detecting the zero position on the
encoder after the control power is turned ON.
2
Indicates the electrical angle from 0 to FF hex.
0 is the position where the inductive voltage on the U
phase reaches the position peak. The angle increases
when the Servomotor turns forward.
The count continues from "0" after exceeding "FF".
3
Indicates the number (total) of MECHATROLINKII com-
munications errors from 0 to FF hex.
The communications error count (total) saturates at the
maximum of FFFFh. "h" appears only for the lowest
byte. The count continues from "00" after exceeding
"FF".
Note
The communications error count (total) is
cleared by turning OFF the control power.
4
Indicates the setting on the rotary switch (node address
value) loaded at startup, in decimal.
This value does not change even if the rotary switch is
turned after startup.
5 to
32767
Reserved (Do not set.)
Pn002
Reserved
---
Do not change.
0
---
---
---
Pn003
Torque
Limit Selec-
tion
2
Selects the torque limit function, or the torque feed-forward func-
tion during speed control.
1
---
---
Online
Settings
can be
changed
when the
axes are
stopped
(Busy
Flag for
each axis
= 0).
• Torque Limit Selection
For torque control, always select Pn05E. For position control and
speed control, select the torque limit as follows.
1
---
1 to 5
1
Use Pn05E as the limit value for forward and reverse
operations.
2
Forward: Use Pn05E.
Reverse: Use Pn05F.
3
Switch limits by torque limit values and input signals
from the network.
Limit in forward direction:
PCL is OFF = Pn05E, PCL is ON = Pn05F
Limit in reverse direction:
NCL is OFF = Pn05E, NCL is ON = Pn05F
4
Forward: Use Pn05E as limit.
Reverse: Use Pn05F as limit.
Only in speed control, torque limits can be switched by
torque limit values from the network as follows:
Limit in forward direction:
Use Pn05E command or option command value 1,
whichever is smaller.
Limit in reverse direction:
Use Pn05F command or option command value 2,
whichever is smaller.
5
Forward: Use Pn05E as limit.
Reverse: Use Pn05F as limit.
Only in speed control, torque limits can be switched by
torque limit values and input signals from the network
as follows:
Limit in forward direction:
PCL is OFF = Pn05E, PCL is ON = Pn05E command
or option command value 1, whichever is smaller.
Limit in reverse direction:
NCL is OFF = Pn05F, NCL is ON = Pn05F command
or option command value 2, whichever is smaller.
Содержание CJ1W-NC271 - 12-2009
Страница 2: ......
Страница 4: ...iv ...
Страница 6: ...vi ...
Страница 22: ...xxii ...
Страница 58: ...30 Starting Operation Section 2 2 ...
Страница 244: ...216 Axis Operating Input Memory Areas Section 4 8 ...
Страница 264: ...236 Transferring Servo Parameters Section 5 3 ...
Страница 396: ...368 Linear Interpolation Section 9 7 ...
Страница 648: ...620 List of Error Codes Appendix D ...
Страница 674: ...646 Additional Functions for the CJ1W NCF71 MA Appendix F ...
Страница 684: ...656 Index ...
Страница 686: ...658 Revision History ...