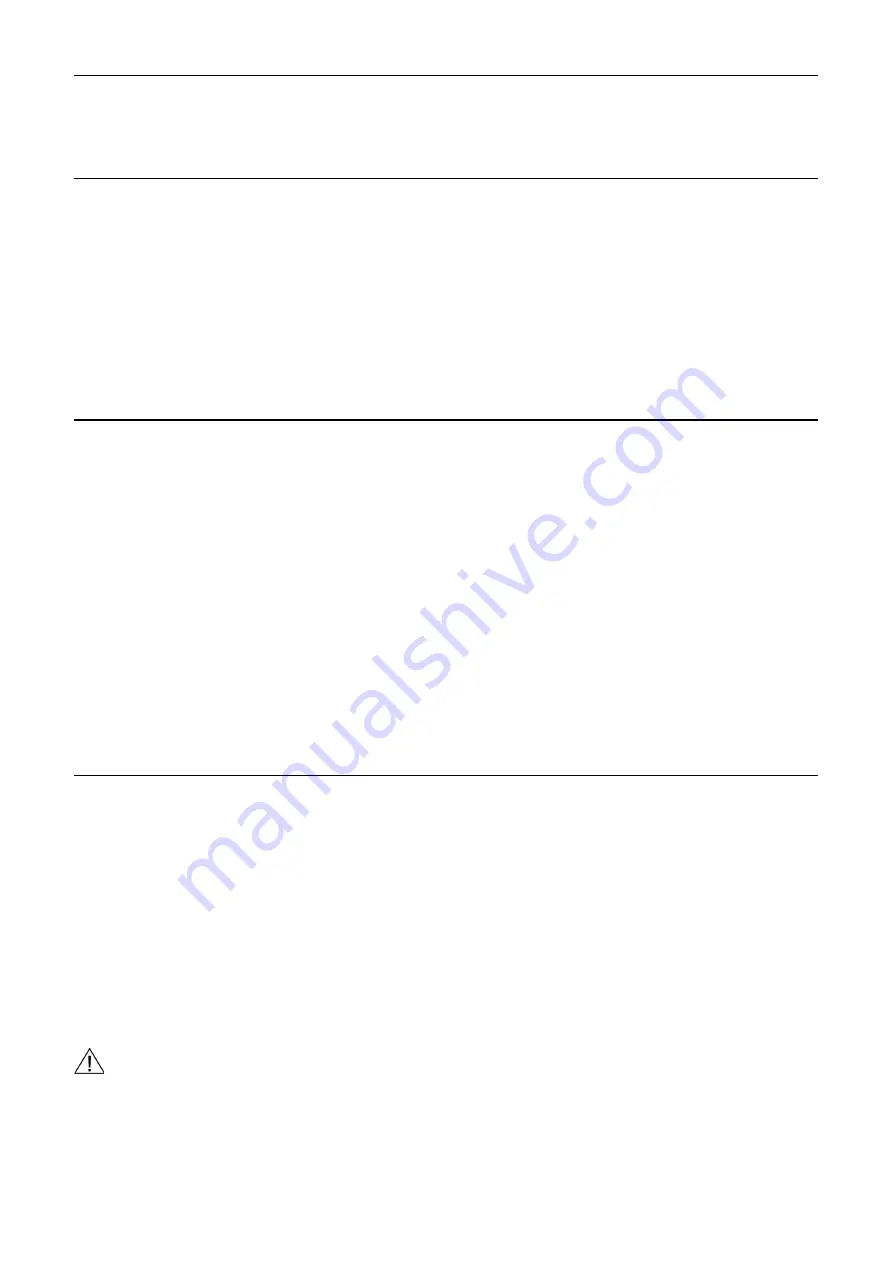
2 Parameters
2.2 List of parameters
SINAMICS G120 CU250S-2 Control Units
384
List Manual, 09/2017, A5E33842890
Dependency:
Refer to: p0432, p0433, p2505
Note:
The gearbox factor between the encoder shaft and the motor shaft is set using p0432 and p0433.
Description:
Sets the load revolutions for the gearbox factor between the motor shaft and load shaft.
Gearbox factor = motor revolutions (p2504) / load revolutions (p2505)
Dependency:
Refer to: p0432, p0433, p2504
Note:
The gearbox factor between the encoder shaft and the motor shaft is set using p0432 and p0433.
Description:
Sets the neutral length units LU per load revolution.
Therefore, for a rotary encoder, a reference is established between the physical arrangement and the neutral length
units LU used in the drive.
Example:
Rotary encoder, ballscrew with 10 mm/revolution, 10 mm should be broken down to units of µm (i.e. 1 LU = 1 µm).
--> One load revolution corresponds to 10000 LU
--> p2506 = 10000
Note:
The position controller can only process position setpoints in the interpolator clock cycle (IPO clock cycle) in integer
length units (LU, Length Unit). This is the reason that speed setpoints that are not a multiple integer of 1 LU per IPO
clock cycle can only be realized as an average. The result speed setpoint steps are especially noticeable for a high
loop gain or when the precontrol is active. Increasing p2506 counteracts this behavior.
Description:
Activates the adjustment and display of the status of the adjustment for absolute encoders.
Value:
0:
Error occurred while adjusting
1:
Absolute encoder not adjusted
2:
Absolute encoder not adjusted and encoder adjustment initiated
3:
Absolute encoder adjusted
Dependency:
Refer to: p2525, p2598, p2599, p2733
Caution:
For rotating absolute encoders, when adjusting, a range is set up symmetrically around zero with half of the encoder
range, within which the position must be re-established after switch-off/switch-on. In this range, it is only permissible
that the encoder overflows.
After the adjustment has been completed, it must be guaranteed that the range is not exited. The reason for this is
that outside the range, there is no clear reference any longer between the encoder actual value and mechanical
system.
p2505[0...n]
LR motor/load load revolutions / Mot/load load rev
CU250S_V (Position
control)
CU250S_V_CAN
(Position control)
CU250S_V_DP
(Position control)
CU250S_V_PN
(Position control)
Access level:
1
Calculated:
-
Data type:
Integer32
Can be changed:
C(25)
Scaling:
-
Dyn. index:
DDS, p0180
Unit group:
-
Unit selection:
-
Func. diagram:
4010, 4704, 4711
Min Max
Factory
setting
-1048576 1048576 1
p2506[0...n]
LR length unit LU per load revolution / LU per load rev
CU250S_V (Position
control)
CU250S_V_CAN
(Position control)
CU250S_V_DP
(Position control)
CU250S_V_PN
(Position control)
Access level:
1
Calculated:
-
Data type:
Unsigned32
Can be changed:
C(25)
Scaling:
-
Dyn. index:
DDS, p0180
Unit group:
-
Unit selection:
-
Func. diagram:
4010
Min Max
Factory
setting
1 [LU]
2147483647 [LU]
10000 [LU]
p2507[0...n]
LR absolute encoder adjustment status / Abs_enc_adj stat
CU250S_V (Position
control)
CU250S_V_CAN
(Position control)
CU250S_V_DP
(Position control)
CU250S_V_PN
(Position control)
Access level:
1
Calculated:
-
Data type:
Integer16
Can be changed:
U, T
Scaling:
-
Dyn. index:
EDS, p0140
Unit group:
-
Unit selection:
-
Func. diagram:
4010
Min Max
Factory
setting
0 3 1