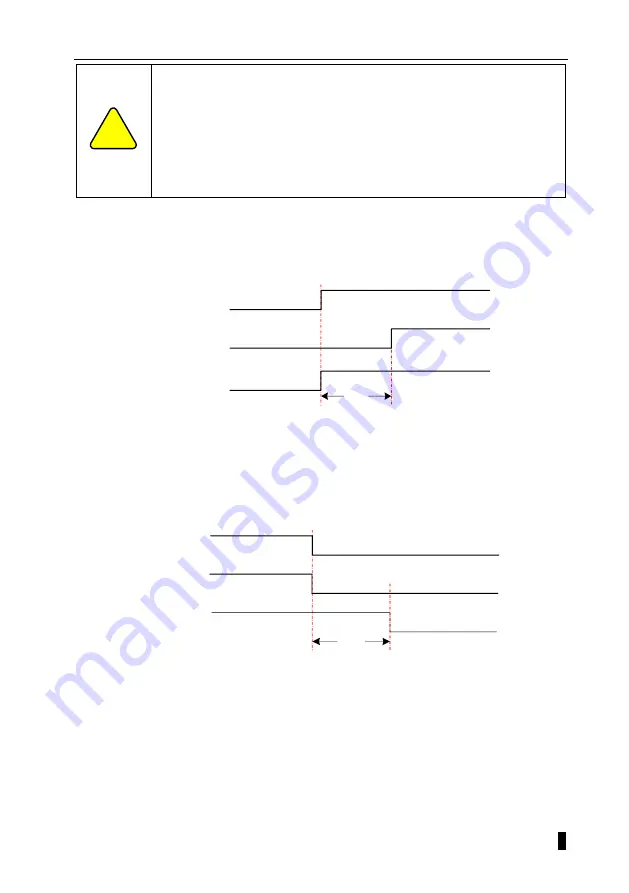
SD710 Series Servo Drive User Manual Chapter 5 Commissioning and Operation
7
● Non
-polarity of the holding coil.
● Servo enable (S
-ON) should be turned off after the servo motor is stopped.
● The brake may click when the motor with the built
-in brake is running, but there is no functional
effect.
● When the holding coil is energized (holding brake open
state), flux leakage may occur at the
shaft end, etc. Be careful when using instruments such as magnetic sensors near the motor.
● The brake mechanism is a non
-energy-activated fixed special mechanism that cannot be used
for dynamic braking purposes and is used only when the servo motor is held in a stopped state.
(1) Holding Signal (/BK) ON at Motor Start
When the servo motor starts, you can set the delay time (Pn00B) for the motor to release the holding brake as a way to
control the time from when the servo receives the ON signal to when the motor actually enters the energized state.
ON
OFF
ON(
release
)
OFF
Servo ON
/S-ON
Motor power
on state
Braking
output
/Bk
Pn00B
Motor power
off
Motor power
on
Fig. 5.5 Timing diagram of the motor start/ BK signal ON
(2) Holding Brake Signal (/BK) OFF Operation When the Motor Stops Locking
When the servo motor is stopped, the holding brake signal (/BK) and the servo enable signal (/S-ON) are turned off at
the same time.The time from when the servo enable signal (/S-ON) is turned off to when the motor actually enters the
non-energized state can be changed by setting Pn008.
Servo ON
Motor power
on state
Braking
output
Motor power
off
Motor power
on
ON
OFF
ON
OFF
/S-ON
/Bk
Pn008
Figure 5.6 Timing diagram of motor stop lockout when/BK signal is OFF
(3) The Holding Signal (/BK) is Turned off When the Motor is running.
When an alarm occurs during servomotor rotation, the servomotor stops and the holding brake signal (/BK) is OFF. In
this case, the holding brake signal (/BK) output time can be adjusted by setting the brake command output speed value
(Pn010) and "Servo OFF - brake command wait time" (Pn009).
!