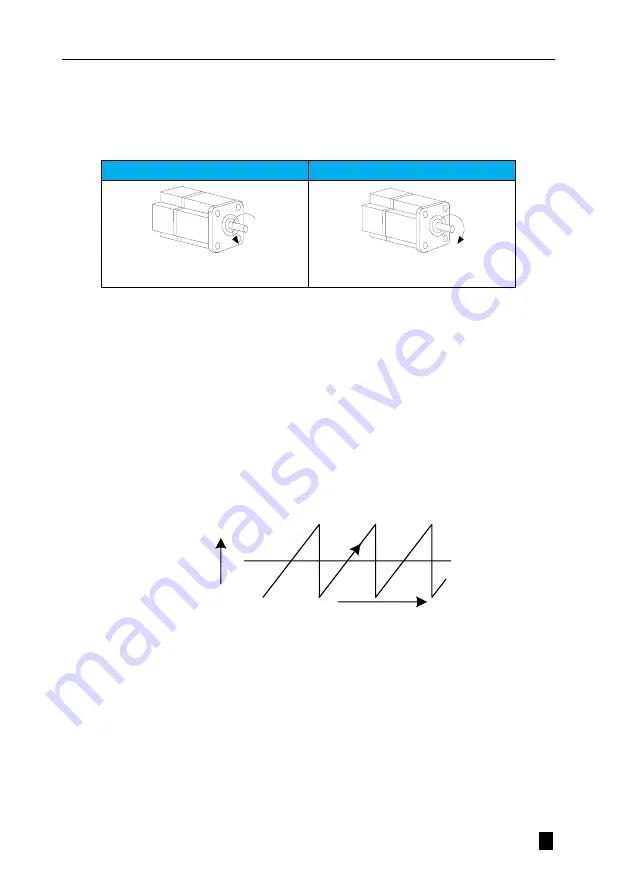
SD710 Series Servo Drive User Manual Chapter 5 Commissioning and Operation
42
Figure 5.47 Typical mechanical device
After the number of turns already rotated, the absolute value multi-turn position information will overflow.
For this, the corresponding position control requires the use of absolute multi-turn upper limits for the corresponding
restriction process.
Explanation of terms
Forward
Reverse
Facing the shaft end, the motor rotates
counterclockwise (CCW)
Facing the shaft end, the motor rotates
clockwise (CW)
5.7.2 Related principles
The general multi-turn absolute encoder shows a count range of [-32768, +32767], as shown below: When the motor is
in positive rotation and running for a long time, the number of rotations of the encoder changes to a maximum value of
+32767; when the rotation continues, then the data overflows. When the power is reapplied after the overflow, the multi-
turn value is no longer appropriate for the absolute coordinate system.
For example
: in a transmission system with transmission ratio n:m=1:5 (i.e., the motor rotates 5 turns and the turntable
rotates 1 turn), when the multi-turn value of the absolute position coordinate zero position is 0 and the single turn value
is 0, the encoder multi-turn data will overflow after the turntable rotates about 6554 turns, theoretically the motor rotates
32770 turns and the turntable rotates 6554 turns, at this time the motor multi-turn data overflows 3 turns and the
encoder multi-turn At this time, the motor multi-turn data overflowed by 3 turns, the encoder multi-turn feedback value
becomes -32766, at this time, the upper computer system operation, then the zero point position of the rotary table has
been offset.
0
Rotate
data
+32767
-32768
Motor rotation
number
Forward
Figure 5.48 Encoder positive revolution overflow
When the upper limit of the number of revolutions is used, it is possible to keep the number of revolutions of the motor
and the number of revolutions of the turntable from trailing in the relationship of the integer ratio.
Still using the above example, for a drive system with a ratio of n:m = 1:5 (i.e., 5 revolutions of the motor and 1
revolution of the rotary table), the table coordinates are no longer affected by the encoder multi-turn overflow when the
upper limit of revolutions is set to 5.